カルビー「本気の全社DX」で判明した意外な最適解 全社データをつなぐキモは現場社員のノウハウ
トップ主導で動き出したDX化だが、徐々に現場スタッフ発案による仕組みも増えてきた。生産状況を見える化したデジタルサイネージはその一例だ。DX推進部や情報システム部はITツールの勉強会を開き、マニュアル動画も作成するなど現場のサポートを進めた。
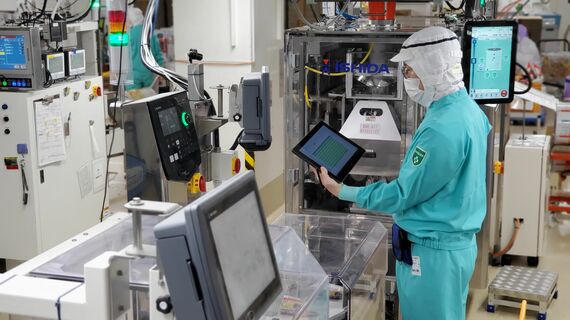
日々の工場業務も、データで振り返ることができるようになった。昨日の成果を翌日に確認し、歩留まりが悪化していると「次はここを変えてみよう」とほぼリアルタイムで業務改善に取り組む。
AIを用いた事例もある。ポテトチップス原料のばれいしょは、北海道の貯蔵庫から高品質のAランクのいもを送っても、工場に届いたときにはB、Cランクが混じるなど品質が落ちることがあった。いもの品質が落ちれば生産できる製品の量も減ってしまう。事前に不良具合を予測するAIモデルを現場とDXチームが一緒に作るなど、アイデアを徐々に具現化していった。
定番商品はAIで需要予測
主に3~4カ月先の定番商品の需要予測にも、AIを活用している。開発までに約2年を要したが、ベテランの生産計画担当者が予測するような精度に近づいてきた。予測を基に、現場の業務を組み立てる活動を始めている。
さまざまな改善活動を通して気づいたのは、現場のスタッフが主導する重要性だ。「他社からデータ人材を送り込んでも効果はない。現場がわかる社員が課題意識を持ってデータを扱えるようにする。時間がないと困っている社員も多いが、やる気を引き出してDXを軌道に乗せていく」と森山氏は語る。
ノウハウはほかの工場にも展開し、最終的に2025年に稼働予定の「せとうち広島工場」に結集する予定。しかし湖南工場のメンバーは、なぜか新工場をライバル視して「広島工場を抜く」と意気込んでいるという。ITベンダーから教わる最初のフェーズを経て、社員自らが最適解を考えるようになった。
無料会員登録はこちら
ログインはこちら