大型のAGV2つが対になって、メインラインの横方向から接近していくのだが、詳しく見ると、エンジンを積んだAGVがメインラインに入り、後方からハンガーが追いかけてくる様子がわかる。そして、AGVがハンガーの位置を確認して動きを同期。
さらに、リアサスペンションなどを搭載する対のAGVが、前のAGVとの距離をセンサーで感知してメインラインとシンクロさせる仕組みだ。
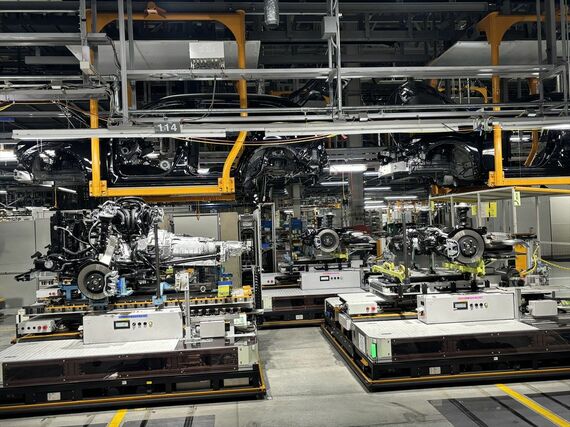
現在、ラージ商品群では、ガソリンエンジン、ディーゼルエンジン、マイルドハイブリッド、プラグインハイブリッドがあり、視察中も各種パワートレインが混流していた。
ここに、2027年に量産予定のEVも入ってくることになる。ただし、EVは電池を含めて重量がかさむため、AGVの仕様も耐荷重100kg以上へ改良する可能性があるという。
EV向け電池のモジュール化とパック化は、防府と広島の中間に位置する山口県岩国市の新設工場からH2に納入する。
電池セルは、パナソニックエナジーの関西圏内工場からくる予定だ。同セルは、スバルの自社EVでも活用される。

今後、H2で大型AGVがさらに増えるとなれば、そのメンテナンスの必要性も高まるが、これについては各工程の作業者が10人で担当設備の「自主保全活動」を行い、マツダ社内で完結させる仕組みづくりを敷く。
ソフトウェアの「書き込み」も形を変えて
最後のポイント・その4は、「ファクトリーOTA」。
車両に搭載するさまざまなECUに対して、いわゆるOTA(Over The Air)を活用する。工場内にWi-Fi環境を整備して、ソフトウェアの書き込みを行うのだ。
これまでのECUは、サプライヤー側で多様な仕様のソフトウェアをインストールしたうえで納入されていた。
それを、各種ECUで共有するベースのソフトウェアのみを書き込んだ状態で納入してもらい、それから先は工場内で行う仕組みとした。Wi-Fiは、機器設置場所の周辺36m先まで通信できるという。
無料会員登録はこちら
ログインはこちら