メインラインに目を移すと、車体それぞれが大きな台車(トラバーサー)に乗った状態で動いていることがわかる。
従来の工場のように、床にベルトコンベアを埋め込むのではなく、床上にモーターとレールを敷くことで、ラインの長さを自由に変更できるようにしているのだ。
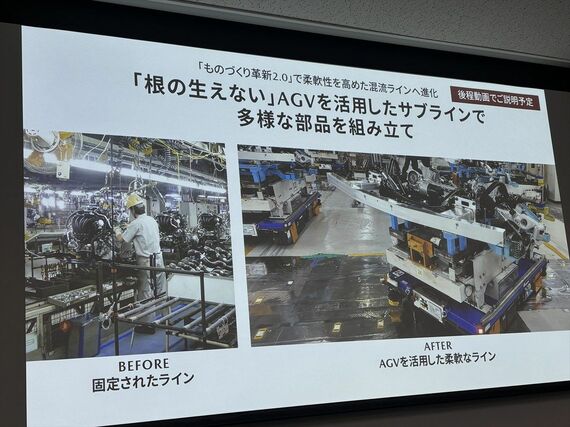
このメインラインは2018年ごろから準備が進められ、2021年にラージ商品群の量産開始とともに稼働しているが、需要拡大にともなって、ライン長は当初の約2倍に伸びている。
また、この方式では「行き」と「帰り」の台車に対して、車両の左右違う作業を行う工程も組み込める。
こうした可変する製造ラインシステムも、マツダが主張する「根の生えない設備」の一環だ。
多様な車種を生産するための柔軟性
ポイント・その2は、「工場内品質保証」と「(バッテリー)モジュール機能保証」。
例として、プラグインハイブリッド車用の組み立て工程を見た。現在、ラージ商品群の生産台数の約4分の1に相当する。
課題は、電池パックの締め付けボルトの本数が多いこと。これをひとつの機器で一気に行うことも可能であるが、マツダはさまざまなモデルやグレードに対応する汎用性を優先し、1本ずつ締め付ける。
作業はAGV(自動搬送車)の上で行い、作業場所の上部にあるカメラが締め付け作業をリアルタイムで記録して、作業の正確さをチェックしている。
仮に、締め付ける順番が違うと、作業が終わってもAGVは移動しない。その後、作業者が電装系のチェックなどを行ってから充電する。
こうしたAGV上の作業工程を、2027年に量産開始予定のEVに応用する予定とのことだ。
その先の工程で注目すべきポイント・その3は、大型AGV2台を使った「根の生えない設備」。
この工程では、車体がハンガーに抱えられた状態でメインライン上を移動しており、そこにパワートレインを下から入れ込む。
無料会員登録はこちら
ログインはこちら