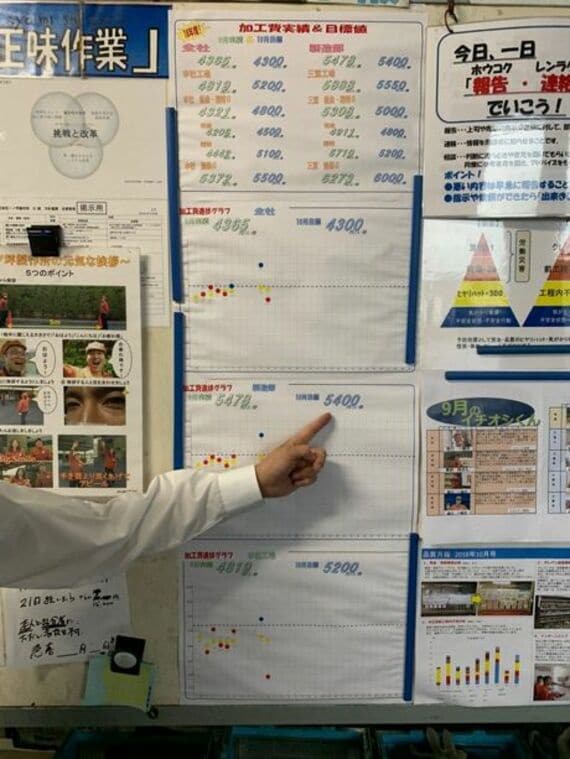
工場建屋の真ん中に大きな看板が設置されています。そこには、各グループの加工実績と目標値が表示されています。1人が1時間にどの位の加工費を生み出したかを、毎日、グループごとに模造紙にドットしているのです。
たとえば、製造部では9月実績は5478円/人・時間でした。一方で、目標は5400円/人・時間となっています。目標を上回った日は青のマーク、下回った場合は赤のマークで、その累計値は黄色で示されます。日々の実績が全員の見える場所に掲示され、まさに究極の「見える化」です。
それも他部署との優劣が一目でわかる、結構キツイ「見える化」だと思いました。
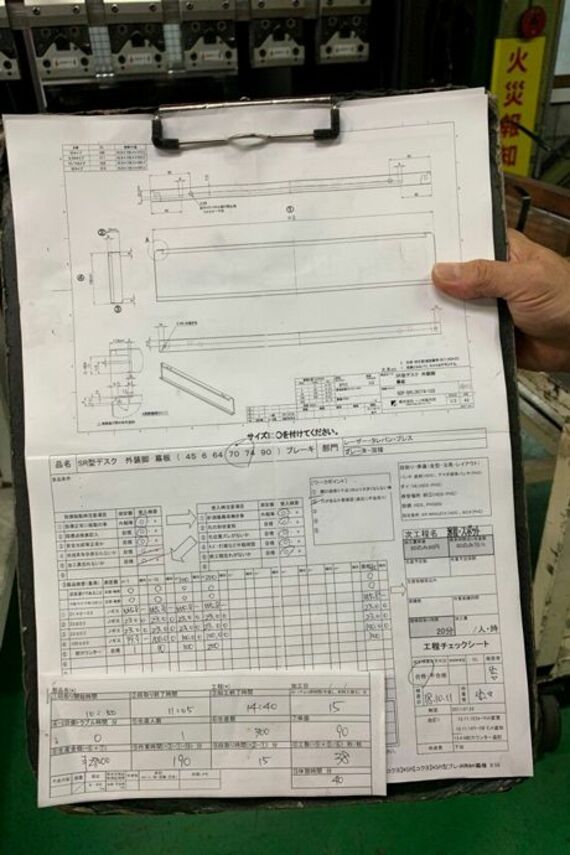
社長に工場を案内してもらって、もう1つ驚いたのは、現場の従業員一人ひとりがクリップボードの上に自らの担当作業が一覧できるペーパーを持っていることでした。そこには、品名、設備稼働時の注意項目、ワークポイント、製品検査基準などが事細かに記され、さらに各工程毎の開始時間、終了時間も記入するようになっています。
この個人毎の集計が、先程の看板のグループ毎の加工費実績に集約されるわけで、初めて目にすると、気の遠くなるような作業に見えます。ただカーキ色の制服を着た従業員の皆さんは、特に大変なことをやっているという感じはなく、日常業務の一環として普通にこなしているようでした。社長が言った「アナログもアナログです」が実感できた瞬間でした。
柔軟なアナログ手法の効果
ただ、この「アナログ」、実は先端のロボット技術、高価な製造機械といった最新デジタル技術の導入が前提にあってのものです。大手取引先の担当者も、その最新機器を見学したうえで、筆者が先程挙げたようなアナログ手法に感心し、取引を継続しているのだと思います。
それでもその膨大な負荷を考えると、「できるところはなるべくパソコンに落とし込んだらいかがですか?」と聞かずにいられませんでした。それに対し一ノ坪社長は「一般の成形品などの加工はコンピュータ処理が可能です。ただわれわれの仕事は、注文相手の要望に即時に対応せねばなりません。つねに変化する得意先の注文に応えるには、『人間の持つ生産性』というべきものが必要なのです」と言います。画一的なデジタル技術を補うには、柔軟なアナログ手法が効果的だ、ということです。長い試行錯誤の末の結論なのだと思いました。
無料会員登録はこちら
ログインはこちら