期待される全固体電池は、どうだろうか。全固体電池とは、これまで正極/セパレーター/負極の間にあった電解液に代わって、固体の部分でリチウムイオンを伝える仕組みだ。
トヨタは、充電時間の短さと航続距離の長さを「全固体電池のうれしさ」として示した。
充電時間を現行電池と比較すると、これまで30分かかっていたところが次世代電池パフォーマンス版で20分、さらに全固体電池では10分と現行電池と比べて1/3まで一気に短縮できるという。
航続距離は、次世代電池パフォーマンス版で200%、全固体電池ではそこから20%増となると説明した。
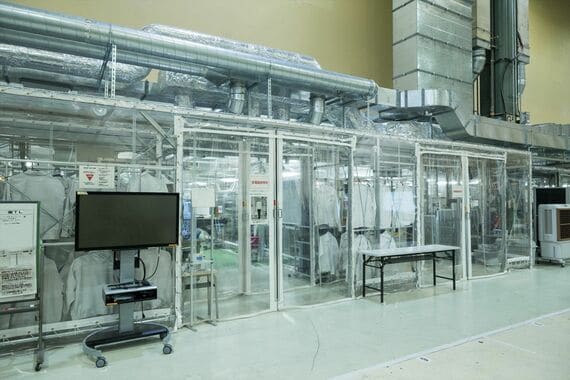
全固体電池の製造は、材料加工、つぶして固める電池加工、そしてできた板上の部品を「速く積む・ぴったり包む」という電池組立工程という流れで行われる。トヨタは、これを知恵と工夫、デジタル、新機構、高速制御などを駆使して、低コストで量産化することを目指す。
今回は、「速く積む」技術を詳しく見た。ポイントは、「速く」「ダメージなく」「精度良く積むこと」だ。
トヨタが独自に開発した装置では、同期制御して流れる小型コンベアの相対速度をゼロにして、上下のパレットが爪を離す/つかむタイミングを同調する「からくり」との合わせ技を使う。こうした量産工法をさらに研究し、2027~2028年の量産化を目指すとした。
無人運転でなくなるコンベアという概念
最後に、元町工場での次世代BEVラインを紹介する。ポイントは、3つの「1/2」だ。
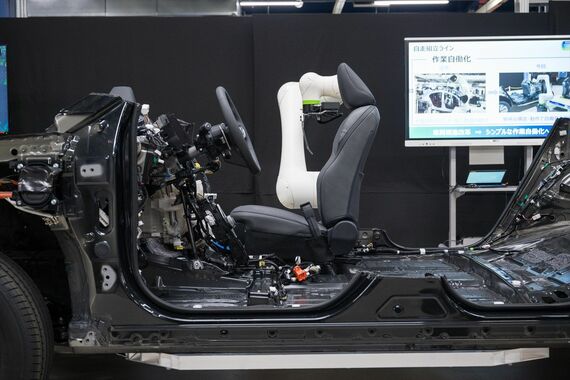
1つ目は、ギガキャストでの大型成型部品を含めた新モジュール工法による、「工程1/2」。2つ目が、車両が自走することでの「工場投資1/2」。そして3つ目が、デジタルツインで検証することでの「生準(生産準備)LT(リードタイム)1/2」だ。
今回、BEVが製造ラインを自動走行する様子を見た。従来の「コンベア」の概念をなくしたほか、シートなどを取り付ける作業も小型ロボットで自動化している。また、部品をトラックから降ろすフォークリフトや部品搬送も、無人運転で行う。
無料会員登録はこちら
ログインはこちら