ギガキャストとは、超高圧かつ超高速で行う鋳造を指す。テスラや中国の自動車メーカーなどがBEV(電気自動車)向けの製造方法としてすでに採用しており、日系メーカーを含めてグローバルで注目が集まっている技術だ。
テクニカルワークショップ2023では、ギガキャストで一体成型した車体後部と既存のプレス加工による部品を溶接して作った車体後部を比較して展示していた。
ギガキャストによって、86部品・33工程で作っていたものを、1部品・1工程で作るという。
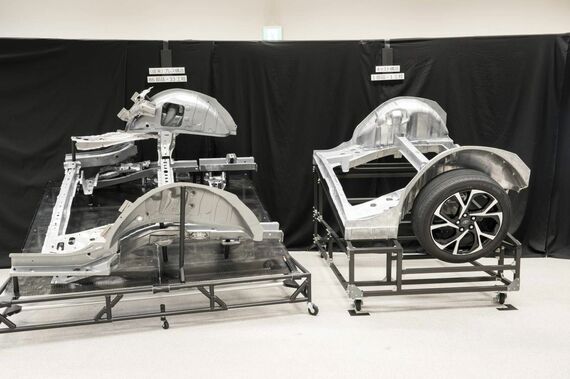
鋳造について改めて説明すると、いわゆる鋳物(いもの)だ。自動車産業で現在、使われている鋳造は、主に低圧鋳造と高圧・高速で行う鋳造であるダイキャストの大きく2種類。
そのダイキャストでの圧力と速度を上げ、大きな部品を一体成型する鋳造方法を一般的にギガキャストと呼ぶ。対応する圧力について、トヨタは「6000トン以上」としているが、「ギガキャストの対応圧力など技術面での定義はまだない」というのがトヨタの見解だ。
今回、明知工場で視察した試作機の圧力は4000トンで、テクニカルワークショップ2023に展示された次世代BEVの車体後部を一体成型する工程を見た。
改良の成果は明らか
工程の内訳は、まず10秒程度でアルミを金型に注湯し、4000トンの圧力をかけてコンマ数秒で一気にアルミを固める。そのあと、数秒でアルミの温度を約700度から約250度まで一気に冷やして、金型から離形(取り外し)。最後に、金型に特殊なスプレーをかけて次の工程で離形しやすくしている。
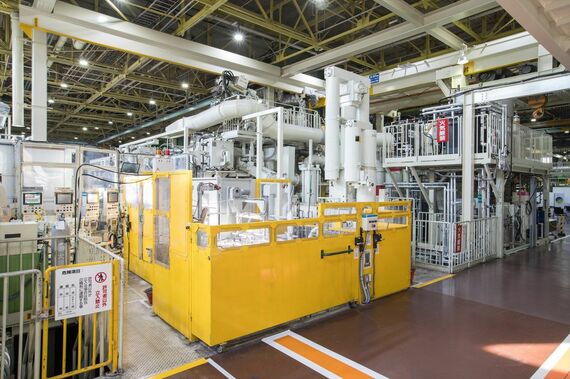
トヨタによると、これまでも高圧のダイキャスト技術は使ってきたが、今回のような大きな成形に採用したのは、2022年9月が最初だそうだ。その1回目で作った鋳物の実物を見たが、一部の肉厚が薄かったり、仕切りであるスリーブの形状がしっかり成形できていなかったりと、粗さが目立った。
その隣には、初回から数カ月後に成形した改良型が展示されていたが、初回で目立っていた粗さが一気になくなり、量産に向けた方向性がしっかり見えた印象がある。
無料会員登録はこちら
ログインはこちら