続くフェーズ2(2025~2027年)が、「電動化へのトランジッション(過渡期)」。そしてフェーズ3(2028~2030年)を「バッテリーEV(BEV)本格導入」と位置づけた。2030年時点でのマツダ総生産台数のうち、BEV率を「25~40%」と幅を持たせている。
こうした表現をマツダが使わざるをえない背景には、国や地域によって電動化に対する社会状況が今後、どのように変化していくのかを正確に推測することが難しいことがある。
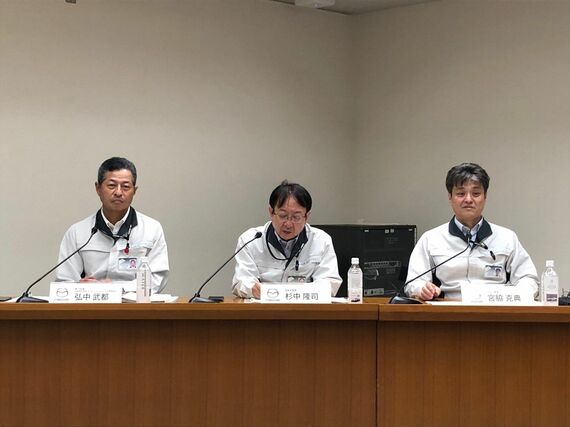
カーボンニュートラルに向けた電動車普及比率を規定する欧米や中国での規制もさることながら、アメリカのIRA(インフレ削減法)に代表される国家間の投資戦略に対する政治的な駆け引きが、予測不能であることが大きい。
そうした「先読みできない電動化シフト期」において、マツダの方針は自社が持つ技術、またはトヨタなどパートナー企業と連携し得る技術を、国や地域によって使いわける。
多様な電動化ユニット(マルチソルーション)を、状況に応じてフレキシブルに生産するのだ。そのために、マツダ生産体制の真骨頂である混流生産を、さらに極める。
工場で見た「マツダらしい」クルマづくり
現在、マツダの国内工場は、広島の本社工場(宇品東地区)のU1 No5(ロードスター、ロードスターRF、MX-30、CX-30)、U1 No6(CX-9、CX-8、CX-5、CX-30)、そしてU2(CX-5)の3ラインがある。
また、本社工場からクルマで2時間ほどの距離にある山口県防府工場では、H1(マツダ3 セダン、マツダ3 ファストバック、CX-30)と、H2(マツダ6 セダン、マツダ6 ワゴン、CX-60、CX-90)の2ラインという構成だ。
今回、U1 No5で特にMX-30 Rotary-EV向けのサブ組立ラインで電池+ガソリンタンクユニットの組み付けや、メイン組立ラインでそのユニットを車体に装着する様子を詳しく見た。
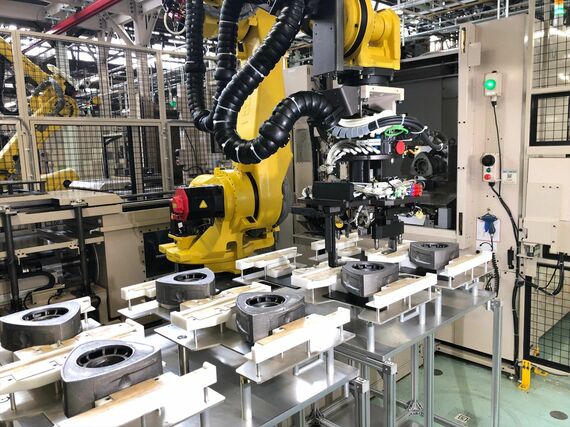
サブラインで行われる電池+ガソリンタンクユニットの電池モジュールは、BEVの場合は16個、PHEVであるRotary-EVはその半分の8個(電池容量:17.8kWh)。そこに容量50リットルのガソリンタンクが、パッケージ化されていた。
ラインの工程としては、メイン組立ラインで流れるクルマの順序と構造を「固定」と見なし、サブ組立ラインでの「変動」とを連携される形をとる。その様子を1モデルで多様な電動仕様を持つMX-30を軸として見ると、マツダらしいクルマづくりの狙いがよく理解できた。
無料会員登録はこちら
ログインはこちら