テスラ、最先端ロボット工場に行ってみた ガソリン車メーカー工場との違いは歴然
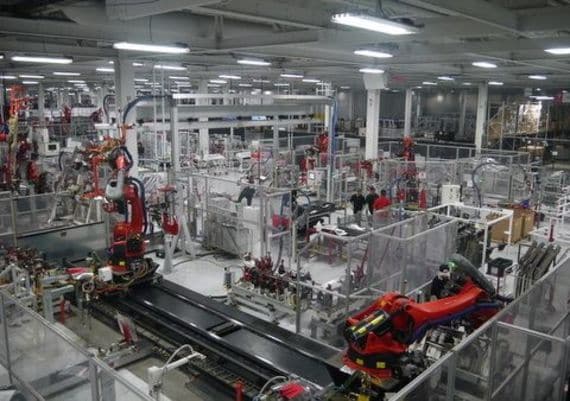
米カリフォルニア州のサンフランシスコ国際空港から車で約30分。フリーモントに着くと、広大な工場と「TESLA」の大きな看板が目に飛び込んできた。ここは米国の電気自動車(EV)ベンチャー大手、テスラモーターズの工場。かつてはトヨタ自動車と米ゼネラル・モーターズ(GM)が設立した合弁工場「NUMMI」だったが、2010年にテスラが買収し、ロボットが動き回る最先端のEV工場に変貌を遂げた。
中に入ると、まず目に入ったのは広大な建屋を自転車で駆け回る従業員の姿。約50万平方メートルに及ぶ巨大工場内では、製造ロボットの動きが目立つが、その脇を人間が自転車ですいすいと駆けてゆく。
素材から一貫生産が特徴
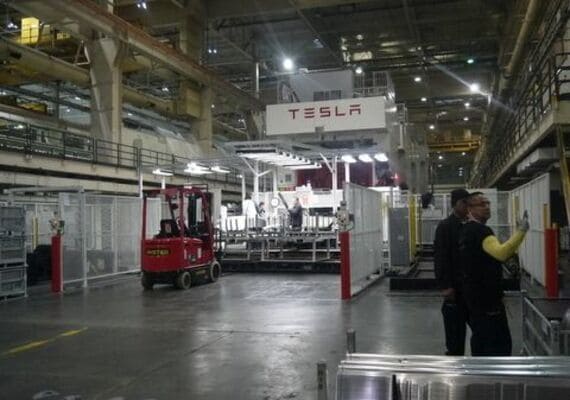
最先端工場というと、無人のイメージがあるが、工場内には部品を投入する人、機械のメンテナンスをする人などの姿も多く見られ、カフェでくつろぐ人々の姿も。「買収した工場を、従業員ができるだけ働きやいように作り替えた」と案内スタッフが教えてくれた。同工場の従業員は約4000人。かつてNUMMIに所属していた人も多いという。
テスラ工場の特徴の一つは、素材からの生産を重視していることだ。既存のガソリン自動車工場の場合、下請け企業から購入して集めた部品を、組み立てる場としての意味合いが大きいが、「われわれの工場はスタンスが違う」(テスラ担当者)。工場内にはアルミニウムを溶融してつくるダイキャストの設備があるほか、プラスチック製品もダッシュボード付近以外は自社で素材から作り上げるなど、内製を重視している。
生産工程の順にカートで進むと、ボディ部品が溶接ロボットで接合され、その他の部品もロボットのアームの先から、次々と取り付けられていく。ボディのカラーリング(塗装)の機械は、NUMMI時代のものを活用。先端の製造ロボットを自社で取りそろえるだけでなく、既存設備を活かすことで生産コストを抑えている。
無料会員登録はこちら
ログインはこちら