工場側が上げてきた課題は大きく2つ。ひとつは、工場にツートンカラーを塗装する工程を組み込むことが困難なこと。もうひとつはツートンカラー用の塗料の開発だ。
工場はそもそも単色用に作られているため、もう1色塗るには新たに工程を足さねばならない。だが、それをどこに組み込むかが難しい。
齋藤ら開発メンバーは、実際に鈴鹿製作所に何度も出向き、工場現場の担当者と議論を重ねた。ヘルメットをかぶって生産ラインも見学した。そのうえで、ライン塗装や手作業による塗装、また新たな工程を置く場所など、さまざまな可能性を工場に提案したという。開発者、とりわけカラーデザインのような1担当者が、実際の量産工程にかかわることは通常なく、異例の取り組みだ。
デザイナー自ら、塗装のテストを繰り返す
最終的には、ベースとなる色の塗装を終えた後、いったんラインから車体を降ろし、マスキングをしたうえで、手塗りをすることになった。自動工程を作れば塗装のスピードは上がるが、もし売れなかったら設備投資がムダになる。工場としては、さすがにそこまでリスクは取れない。
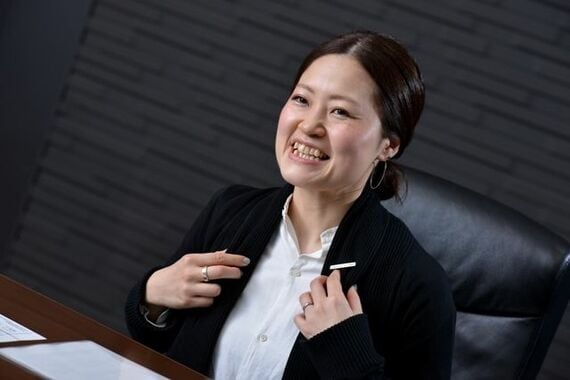
塗料開発では、「塗料は自分の直接の領分なので、自ら提案やテストを繰り返した」(齋藤)。通常の塗料開発であれば、カラーデザイナーが色を提案すればそれに沿った形で、塗料が開発され、量産に回る。
だが、ツートンカラーの場合は、ベースカラーの上に2色目を塗るため、色や塗料の組み合わせによっては、ベースの色が透けてしまい、想定どおりの色にならない。齋藤にはちゃんと塗装できることを証明する必要があった。
齋藤は、塗料・色の組み合わせや、塗装の厚さなど、自らテストを何度も繰り返し、ツートンカラー実現に向け、検証を行った。「A4サイズの車体と同じ鋼板に色を塗って、実際の組み合わせを作り、これなら大丈夫と、工場を説得した」と齋藤は語る。
結局、工場を説得するまでには1年以上の時間がかかり、量産工程の完成まで含めると約2年もの取り組みになった。
無料会員登録はこちら
ログインはこちら