新開発の低重心・低慣性プラットフォーム、薄型バッテリー、小型軽量・高効率のeアクスル(モーター・インバーター・ギア)の採用に加えて、歩行ロボット「アシモ」で培った3次元ジャイロ姿勢推定と安定化に対する制御を採用。結果的に「意のままにドライブ」できる感覚となっていた。
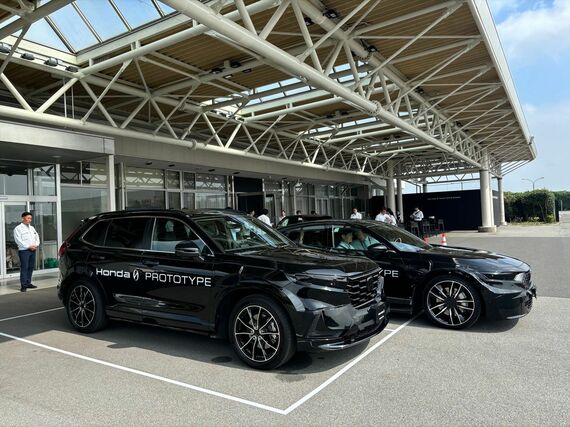
筆者はこの11日前、ホンダの北海道鷹栖町にある大規模テストコースで、量産型の燃料電池車「CR-V e:FCEV」を試乗していたが、ハンドリング・乗り味・走行感が、ゼロシリーズSUVプロトタイプも“同じ方向性”にあると感じた。
つまり、“ホンダらしい”走りが統一されているということだ。
そのほかにも先進ドライバー運転支援(ADAS) や自動運転技術、データやサービスを敏速に行うためのE&Eアーキテクチャー、AIを使った車内および車外でのドライバーの意図理解・行動予測、遠隔からの仮想同乗などの最新技術を体験し、量産レベルに達していることを肌で感じることができた。
変わる「バリューチェーン」
四輪生産本部では、6000トン級で行う鋳造技術、いわゆるメガキャストで生産するゼロシリーズ向けバッテリーパックの製造工程や、ホンダが独自に開発した直流を制御する溶接手法「CDC」などについて詳しい説明を受けた。
丸1日にわたり行われたゼロテックミーティングを通じて、ゼロシリーズの技術的な背景や、ホンダ技術のポテンシャルはよくわかったが、その一方で「コスパと実用性を考慮したクオリティ」と「他社との差別化」とのバランスの難しさを感じたことも事実だ。
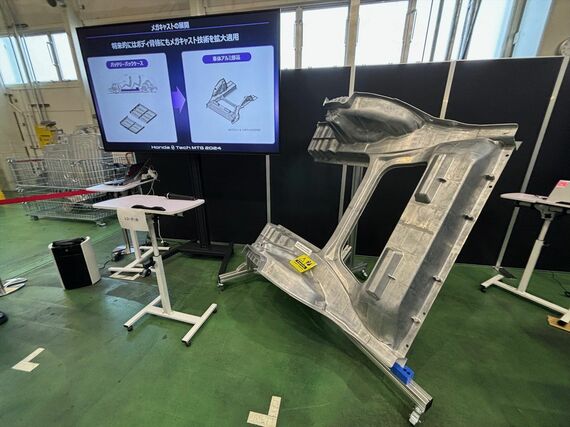
各種の技術とサービスがゼロシリーズの魅力を高めることはわかる。しかし、BEVがグローバルで急激に進化する中で、ユーザーが“ホンダらしさ”をどうとらえるのかは未知数である。
そこでキーになるのが、いわゆる「バリューチェーンの変革」だ。ここでいうバリューチェーンとは、ユーザーが新車を手にしたあとのサービス領域全般を指す。
一方で、自動車製造過程での材料や部品の調達、そして最終組み立ての領域をサプライチェーンと呼んでいる。現在の自動車産業は、実質的にサプライチェーンとバリューチェーンが分離している構造だ。
無料会員登録はこちら
ログインはこちら