「三菱自動車に対してお客様は、会社として良くないイメージもあるかもしれませんが、クルマについては『こういうのが三菱だよね』というのがあると思う。それに逆らうのではなく、遺伝子、資産のひとつとして考えて伸ばしていったほうが得策ではないかと。そのほうが会社としても得だし、お客様にも喜んでもらえるんじゃないかなということですね」
そう語るのは加藤社長である。独自性がなければ、あえて三菱自動車のクルマを選んでもらえはしないということだ。
「先日、デリカミニを出しました。正直スーパーハイトの軽自動車は同じようなクルマが並んでいます。その中でどれを買いますかという時に、特徴を出さないとうちは選んでもらえませんから」
数多くの選択肢が揃う中で、ブランドとして三菱を選ぶのは実際、少数派となるだろう。一方、三菱のファンからしてみれば、「軽自動車は結局、日産製でしょ?」ということになり、やはり満足させることができない。あえて独自のデザイン、走りなどをまとわせたデリカミニが生まれた背景には、そういう事情もあった。
そうなってきたのは現行「アウトランダー」辺りから。プラットフォームは日産エクストレイルと共通だが、独自のPHEVシステム、制御技術などを入れて差を生み出していくうちに、三菱らしいクルマとなった。長岡副社長はこう言う。
「トライトンでは、フレームとエンジンとパワートレインは全部われわれ。“らしい”をしっかりやれたと思う。それにアライアンスの電子技術を融合しながら、“らしさ”を感じてもらうことが非常に重要だと思っています」
生産拠点を刷新し自動化率を向上
さて、開発も生産も自前でとなれば、当然そのための体制も整える必要がある。実はこの新型トライトンの立ち上がりに向けて、三菱は生産拠点の大幅な刷新を行った。
バンコクから南東に2時間ほど行った先にあるレムチャバン工場は1992年に生産を立ち上げた施設で、積み出し港であるレムチャバン港まで約3.5kmという優れた立地を誇る。実際、港湾当局との取り決めにより、完成車はラインを出た後、何と自走で港まで運ばれるという高効率ぶりなのだ。
生産能力は現時点では年間最大42万4000台。ここのうちトライトンを生産する第2工場が改修され、ロボットの大量導入、塗装の水性化、組み立てラインのIoT導入といった最新化などが行われた。
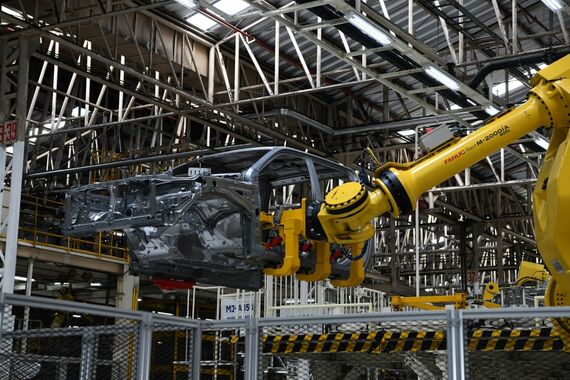
「月並みですが、ロボットで自動化率を上げています。今まではタイも溶接ラインでは人が室内に入って作業していました。人の力を活用していたのですが、こちらも賃金レベルが上がってきて、その意味では自動化のほうがメリットが出てきた。実際にロボットを入れると品質も安定しますしね」
無料会員登録はこちら
ログインはこちら