トヨタとホンダが「EV生産改革」でテスラを追撃 「ギガキャスト」や「モジュール構造」導入へ
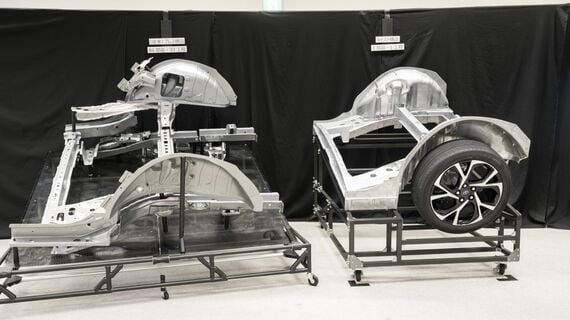
「日本の自動車メーカーはまさにテスラ化している」。ある大手自動車部品メーカーの幹部はそう驚きの声を上げた。
日本の自動車メーカーがEV(電気自動車)の競争で勝ち抜くために、生産工程の抜本的な見直しに取り組み始めた。ガソリン車と異なる構造であることを重視し、車両の設計や構造、生産手法を根本から見直す。見本とするのはEVで先行するアメリカのテスラだ。
トヨタ自動車は6月中旬に、次世代EVに使用する車体部品について「ギガキャスト」の導入を検討していることを明らかにした。ギガキャストは、車体部品を一体成形できる技術で、アルミダイキャストという鋳造法で溶かしたアルミ金属を流し込んだ金型を圧入して整形する。
アルミダイキャスト自体は既存技術だが、「ギガ=巨大な」という言葉どおり巨大な装置で大型部品を作り出す。別々に造った複数のパーツを溶接などでつなぎ合わせていたこれまでの工数、つまり製造コストを劇的に削減できる。
86個、33の工程が1つに集約
たとえば、トヨタが2022年に発売したEV「bZ4X」のリア部分は、86個の鉄製の部品を33の工程で一体化している。ギガキャストを導入することでアルミ合金製の1個の部品に置き換えて、工数は1に減らせるという。
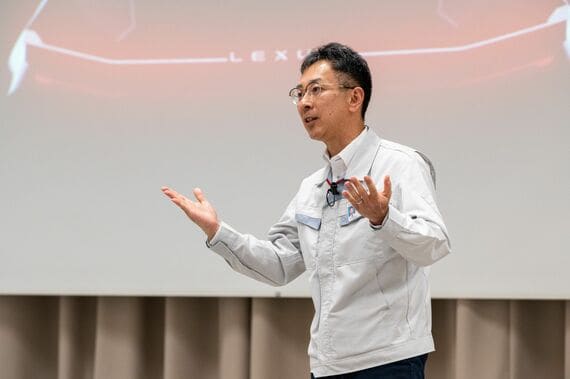
トヨタの生産改革は、ギガキャストの採用にとどまらない。次世代EVでは、現状のガソリン車やEVに比べて車体構造をスリム化・標準化する。具体的には、車体をフロント、センター、リアの3分割した大きなモジュール構造とすることで、車種の開発や生産を簡単にできるようにする。
このうち、フロントボディとリアボディを前述のギガキャストで生産する。さらにトヨタ生産方式の思想も盛り込むことで各工程の無駄を削減、効率化を徹底する。トヨタでEV事業を統括するBEVファクトリーの加藤武郎プレジデントは、3分割のモジュール構造とギガキャストの採用によって、「車両開発費と工場投資を削減できる」と自信を示す。
無料会員登録はこちら
ログインはこちら