日本に自動車生産は残るのか?--トヨタ、日産の賭け “最後”の国内工場(上)
だが準備が本格化したところにリーマンショックが襲う。直前の08年3月期に1512億円だったセントラルの売上高は、10年3月期には728億円とわずか2年で半分以下まで急降下。この期には57億円もの営業赤字を出した。「何の準備もなしに現状を迎えていたら、相模原工場閉鎖だけで終わりかねなかった」と新美副社長は振り返る。
最悪期には稼働率が3割まで下がった苦境にあっても、セントラルでは手が空いた社員による地道なカイゼンが続いていた。たとえば、外部から買っていた自動走行台車を自分たちで試作してみることで、大幅なコスト削減が可能になった。こうして積み重ねたノウハウが、宮城工場にはぎっしり詰めこまれている。
宮城工場では、車体を吊るすコンベヤーを廃止したことで、天井の高さは4メートルと一般的な完成車工場の3分の2程度に収めた。車体に足回りの部品やエンジン回りの部品を取り付ける工程では、縦を向いて流れるのが通常のラインを横向きに変更。作業性が上がりラインの長さを35%圧縮できた(下図参照)。
こうした工夫の積み重ねで、宮城工場の設備投資は、当初の計画に比べて6割ほどに抑えられた。1台当たりの生産コストでいえば、5%前後の削減効果がある。
実はラインのコンパクト化、低コスト化への取り組みは、トヨタだけではない。数年前までトヨタの拡張路線についていくのに必死だったサプライヤー(部品会社)は、減産で生まれた余裕をカイゼンに振り向け、ラインの競争力を磨いてきた。
中央発條や愛三工業など愛知県の中堅サプライヤーでは、「既存ラインと同等の生産能力を持ちながら、設備投資が半分」というラインが続々と出来上がっている。「彼らがやっていることこそ本当の革新。これが広がっていけば、まだまだ日本で車は作れる」(新美副社長)。国内生産320万台を死守するというトヨタの方針は、「生産革新」を生み出すネットワークへの期待に根差しているのだ。
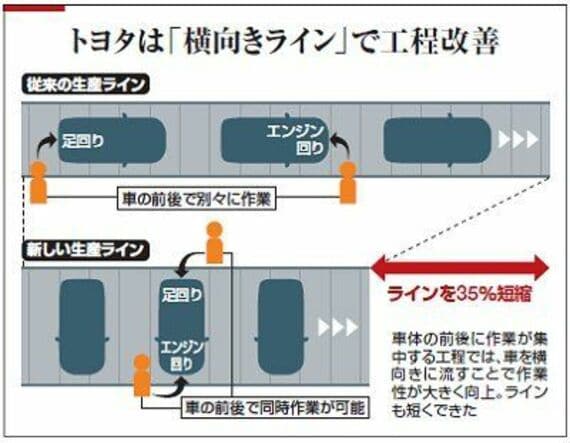