新日鉄住金、報告書に浮かぶ連続事故の真因 なぜ1年間で5度もトラブルが起きたのか
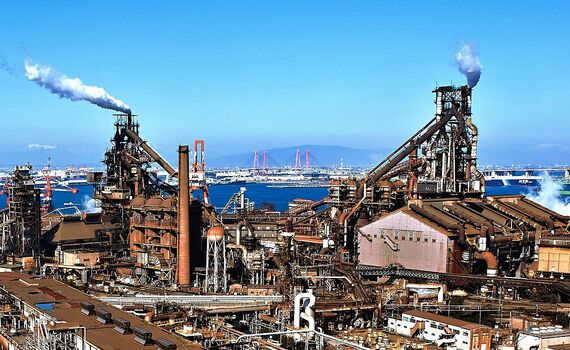
名古屋製鉄所は新日鉄住金にとって基幹製鉄所の1つ
1つは、コスト削減のために導入した新設備への理解の不十分さ、そして危機管理を徹底できなかった点だ。
新日鉄住金をはじめとした大手鉄鋼メーカーは、高炉に1200度を超える熱風を吹き込み、鉄鉱石を石炭によって還元させて鉄を造っている。特に日本メーカーが得意とする高級鋼を造るためには、高品質の石炭は欠かすことのできない存在だ。
ところが、中国の鉄鋼メーカーが急速に生産量を増やしたことで、この高品質な石炭の奪い合いが激化していた。2008年や2011年には1トン当たり300ドルを超えたこともある。足元の価格こそ120ドル程度まで下落しているが、それでも2000年代前半までは50ドル前後で推移していたことを考えれば、高値水準にあることは間違いない。
粉状の石炭を固めてコスト削減
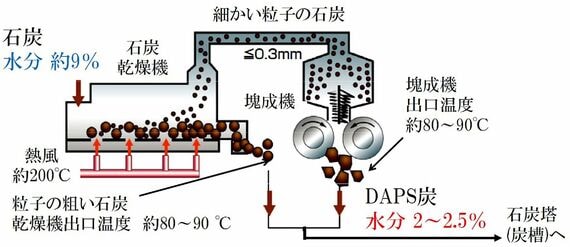
DAPS設備のフロー(新日鉄住金の資料から抜粋)
そこで、日本の鉄鋼メーカーは高品質な石炭である「強粘結炭」の使用量を減らし、「非微粘結炭」という粉状になりやすい石炭の使用量を増やしていた。
強粘結炭は、読んで字のごとく、粘結性が強く、堅い石炭のことを指す。一方、非微粘結炭は強度がなく、粉状になっていることが多い。強粘結炭は産地が限られるのに対し、非微粘結炭は世界各地で産出され、安定的な調達が可能だ。そのうえ、強粘結炭よりも価格が大幅に安い。
ただし、粉状の非微粘結炭は高炉内の空気の流れを阻害してしまうため、そのままでは投入できず、塊状に加工する必要があった。そこで、新日本製鉄は調湿・分級(DAPS、Dry-cleaned and Agglomerated Precompaction System)という加工手法を開発した。これは石炭を乾燥させ、大きな塊と小さな粉に分離し、小さな粉を塊に成形するというものだ。
こうした事前処理を施すことで、これまでであれば投入する石炭全量のうち10%しか使えなかった非微粘結炭を、40%まで引き上げることが可能になった。旧新日鉄のIR資料によれば、DAPSを導入することで15%の省エネ効果があるほか、生産性も2割程度引き上げることができたという。
無料会員登録はこちら
ログインはこちら