大企業が教えを請う“ダイセル式”カイゼン活動
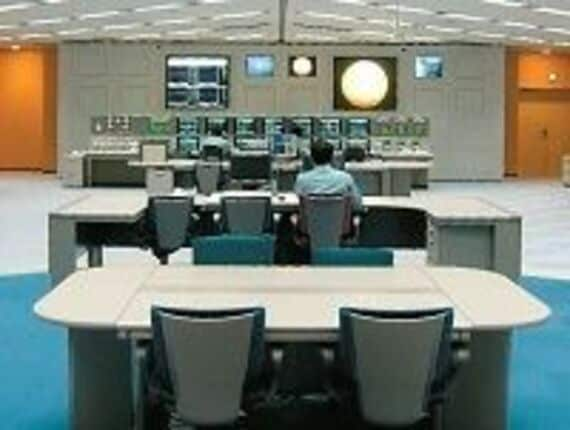
兵庫県南西部に位置する姫路市網干地区。揖保川が瀬戸内海へと注ぎ込むこの工業地帯で、次世代のものづくりが胎動し始めている。
それは「ダイセル方式」と呼ばれる、プロセス産業版のカイゼン活動。ダイセル化学工業のここ網干工場から始まった、新しい生産革新の取り組みだ。プロセス産業とは、化学、医薬品、鉄鋼、非鉄金属、窒業、ガラス、紙・パルプなど、主に素材から中間財を製造する装置産業を指す。自動車のような組立・加工産業とは違って、プロセス産業では製造工程が見えにくく、生産革新が難しいと言われてきた。
さまざまな業界から、この網干工場を見学に訪れた企業は延べ500社、約4000人に上る。まさに“ダイセル詣で”とも呼ぶべき光景だ。コンサルティングの要請も多く、ダイセル化学は2005年から、横河電機と協業で「知的生産支援コンサルティング」として、同方式を外部の顧客へ販売してきた。今では順番待ちの引く手あまただ。
「格上」企業が続々導入 技術承継への一つの解
ダイセル方式を導入済みの企業には、三井化学、住友化学、ダイキン工業など、ダイセル自身の倍以上の売上高を誇る“格上”大企業が名を連ねる。ほかに、東洋紡、日本ゼオンなども顧客だ。導入に踏み切った企業の担当者が最初に受けた印象は鮮烈だった。
「初めて網干工場を見学したときは、頭を殴られたような気がした。今までわれわれが行ってきた改善運動は、いったい何だったのだろうか、と」(宮本正文・日本ゼオン常務)
「網干工場は決して最新の製造設備ではないにもかかわらず、工場内に人が少なく、あいさつなどの対応もいい。整理、整頓、清掃の3Sが隅々まで行き届いていることに衝撃を受けた」(野田知久・ダイキン工業生産革新プロジェクト担当部長)
日本ゼオンの場合、同方式を導入したことで、2年間でオペレーター(現場作業員)の作業負荷が66%、ダイキンは67%削減された。作業負荷とは設備点検など日々の業務のこと。これを減らすことが、工場の安定化と生産効率のアップに直結する。
しかし、「ダイセル方式の効果は定量的なものにとどまらない」と前出の宮本常務は言う。激化する国際競争で勝ち残るためには、当然、コスト削減のための少人化が必要である。ただ、団塊世代の大量引退という問題は、産業そのものの担い手がいなくなるという意味で、より深刻だ。
昨年3月には信越化学工業が新潟・直江津工場で、同12月には三菱化学が茨城・鹿島事業所で共に大規模な火災事故を起こした。少なくとも三菱化学の事故については、同社の元技術者からも技術の承継について不十分だったとの指摘がある。現場での技術をどう伝えるか。製造工程を目で確認しにくい素材産業では、経験豊富なベテランのオペレーターに役割が集中しがちだ。属人的要素の強い産業で、ダイセル方式はベテランの技術をITシステムに組み込むことで、広く解決策を提供した。大手がこぞって導入した理由がここにある。
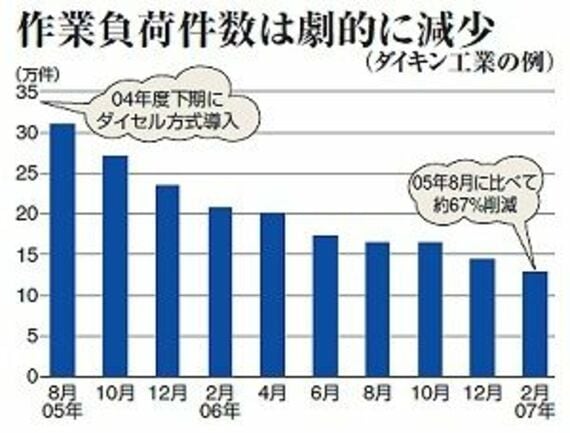