環境先進企業の挑戦<2> リコー−−取引先を巻き込め! 全包囲でCO2を削減
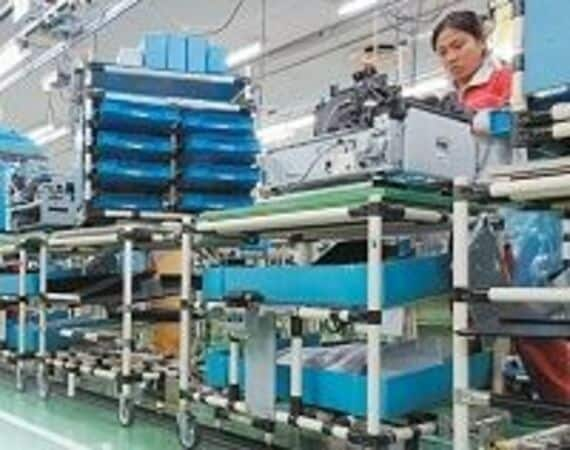
埼玉県八潮市にあるリコーグループ子会社、リコーユニテクノ。一見すると先端技術からは程遠い、昭和の雰囲気漂うファクシミリの製造工場だ。だが、社員数400人弱とさして大きくないこの工場に大型バスが乗り付け、連日国内外から多くの見学者が訪れる。
工場内に入るとまず気づかされるのはその静かさ。工員たちが粛々と組立作業をこなしているものの、ベルトコンベヤーやロボットのモーターから聞こえてくる工場特有の音がほとんどない。肩透かしな印象を受けるが、まさにこれこそがこの工場の先進性の表れだ。
工員たちの前に並ぶのは、ファクシミリ本体や部品が置かれた台。台には車輪が付いており、モーターの動力により、ゆっくりと動いている。一人目が担当の作業を終えるころには製品は次の工員の作業場所近くまで移動。製品は組立工程から検査工程へと流れ、ファクシミリなら2時間ほどで完成する。その後、社内で手作りの搬送ロボットが階下へと運んでいく。
かつてはこの工場でもベルトコンベヤーを採用しており、1996年には1ライン100メートルのコンベヤーが10本並んでいた。1本のベルトコンベヤーには大小54のモーターが付いており、ライン1本だけで1日114・6キロワットの電力(CO245・8キログラム相当)を消費していた。それが現在の台車方式に変えたのは、98年夏のこと。台車方式では1ラインに二つのモーターが付いているのみで、1日の消費電力はわずか2・75キロワット。CO2排出量も1日たったの2・07キログラムだ。
また、工場の屋根や側壁には合計136枚の太陽電池パネルが張り付けられており、ここで作られる電力だけでライン3~4本分の電力は十分賄えるという。工場全体で、限りなくエネルギーを使わない生産体制が築き上げられている。音の静かさや台車の速度の遅さは、まさに省エネの証しなのだ。
やむを得ぬコンベヤー廃止が環境にも好影響
68年に設立されたユニテクノは、グループのファクシミリ生産拠点として、月5万台のファクシミリを製造していた。だが95年、中国・上海にグループの新たなファクシミリ拠点がつくられると、ユニテクノでの生産量は急激に減り、図面の印刷に使う業務用の大型複写機に生産をシフトすることとなった。
大量生産するファクスから生産量の変動が大きい業務用複写機に事業を切り替える中、生産方式の見直しが迫られた。100メートルコンベヤーの場合、月の生産量が半分になったときに半分だけ動かすという融通はきかない。そのため、フル稼働の場合を除き、つねに無駄な電気がかかることになる。そこで98年に、ラインの長さを自在に伸び縮みさせることができる台車方式を導入した。いわばベルトコンベヤー廃止はやむを得ぬ決断で、台車ライン導入の目的はあくまで生産効率向上だった。
が、電気利用を抑えたことで、結果としてCO2削減にも大きく貢献。今では国内リコーグループ全社が台車方式を採用している。