タカタ破綻で注目、「エアバッグ」生産の裏側 躍進する業界2位、日本プラストの工場へ潜入
運転席用のバッグを機械で折り畳んでいるところは、「企業秘密」を理由に撮影を断られた。バッグの折り畳み方がエアバッグ展開時の性能を左右するからだという。自動車メーカーの品質基準をクリアするのは当然だ。そのうえでエアバッグが膨らみ切った時に乗員に与える衝撃を軽くし、しぼんだときに乗員を受け止める性能をどれだけ高められるかでモジュールメーカー各社は競い合っている。
一方、助手席用バッグは社員が指示書を見ながら、丁寧に手で折り畳んでいた。展開時の性能を出すためには複雑な折り畳み方が必要で機械化では対応できないという。社員が折り畳みの工程を担当するためには社内の試験を合格する必要もある。
この20年超でエアバッグサイズは3分の1に
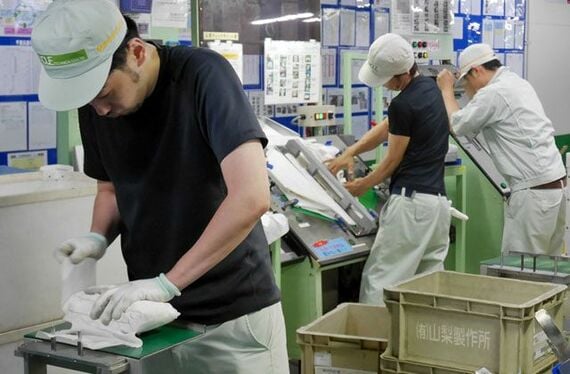
さらに競争が激しいのはモジュールの小型化だ。より小さくできれば、ステアリングのデザインの自由度も高められる。実際、日本プラストが製造するモジュールの容積は1990年の量産開始時に比べ、今では3分の1になったという。インフレーターの小型・高性能化に加えて、バッグがかさばらずに折り畳めるようになったことが大きい。
エアバッグを製造する富士工場の遠藤正人工場長は「自動車メーカーからはモジュールの容積をさらに20%減らしてほしいと求められている。容積を減らしてもエアバッグの性能は維持、向上させないといけないので開発のハードルは高くなっている」と悩ましげだ。
タカタ製エアバッグの品質問題を受け、エアバッグモジュールの調達をタカタから他社に切り替える自動車メーカーが相次いでいる。日本プラストも今年度下期から新規大型受注を獲得。増産対応に伴い、2017年度の設備投資は前期比5割増の83億円を計画している。
エアバッグ事業拡大のチャンスをつかんだわけだが、タカタのようにインフレーターを内製する可能性もあるのか。前出の長田・先行開発部次長は、「インフレーターへの新規参入はまったく考えていない。技術の肝がわからない人間が、作り方を教わって手順どおり作ればいいというものではない」と強調した。
まずは自社が得意とする技術領域を確実に深めていく。人命にかかわる安全部品を手掛けるメーカーだからこそ、慎重な姿勢が求められる。
日本プラストの株価・業績 は「四季報オンライン」で
記事をマイページに保存
できます。
無料会員登録はこちら
ログインはこちら
印刷ページの表示はログインが必要です。
無料会員登録はこちら
ログインはこちら
無料会員登録はこちら
ログインはこちら