ホンダの最新鋭工場は一体、何がスゴいのか 寄居工場の生産ラインはこんなにも効率的だ
寄居工場は、車種、ボディカラー、取り付け部品が違うグレードを同じラインで生産する混流ラインであり、工程をまたいでの情報共有も重要視されている。塗装では、ボディカラーに違いが出ないようにドアやハッチバックを一緒に塗る。それをいったん外して、ロボットと人間の手で効率よく部品を取り付けていく。シートの取り付けや、フロント/リアのガラスといった重量部品の取り付けは、ロボットで自動化されている。燃料タンクのような10kgを越える重量級パーツはすべて自動で組み付けられる。
自動化によって得たこと
マルチサスマウントの工程も、自動化が進められた部分だ。シャシー中央部を抑えるロボットがせり出してきて、そこをしっかりと止めることで、前後のサスペンションを整列させて、前後のロボットが一斉に動いて取り付ける。前後の足回りの取り付けに要する時間は、ひとつの工程でわずか50秒以下だ。コストを下げるだけではなく、走行安定性の確保にもつながる。また、取り付けが原因の不良を40%も減らせた。
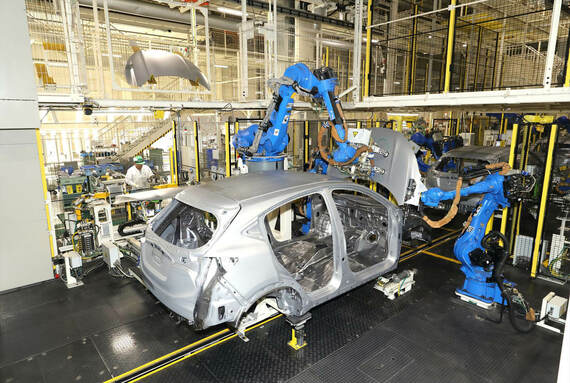
インストゥルメントパネルの組み付け工程では、狭山工場では2人の作業者を必要としたが、寄居工場ではロボットと一人の人間が連携して組み立てている。80Wの出力しか持たない低出力マニュピレーターと呼ばれる組み立て支援ロボットを使って、安全柵なしに人間と機械が連携してボディを組み立てられる。これにより、設備の専有面積が60%も減った。
タイヤも、自動で組み付けられている。4つのロボットが、ネジの設定、センサーでのタイヤの位置決め、締め付けといった役割分担をして、上手に組み上げていく。個々の役割を担ったロボットが連携する様子は、なんとも可愛らしくて、ユーモラスだ。従来のラインでは前後に2組、合計で8機のロボットが設置されていたが、新設されたラインでは車台を半分動かしてやることで、4機一組のロボットで前後のタイヤを取り付けることができる。見学した際は4穴のホイールを組み付けていたが、治具の交換で5穴にも、前後異型ホイール/タイヤにも対応できる。
最後に、ピカピカの新車が工場のラインから出てきて終わり、というわけではない。塗装面の品質や動作などの検査を受けた後、併設されるテストコースでの完成車走行テストを受けて、トラックに搭載されて顧客のもとに届けられていくのだ。
無料会員登録はこちら
ログインはこちら