新幹線の「亀裂」はなぜ発見できなかったのか 専門家がわかりやすく解説する技術的背景
京浜急行の電車を例に取ると、全般検査または重要部検査(走行距離60万kmまたは4年ごと)で工場に入ると、床下は台車だけピカピカに塗装されて出てくるが、これは塗装を剝がして磁粉探傷をしているからである。台車の構造や過去の亀裂発生の有無から、台車枠に十分な疲労強度があれば磁粉探傷は必ずしも実施する必要はない。
新幹線の台車は、全般検査または台車検査(走行距離60万kmまたは1年半毎)で異常の有無を確認しているが、磁粉探傷は実施しているのだろうか? もし実施しているのに亀裂を見逃したとすれば、検査が形骸化していた可能性もある。
東海道新幹線開通2年後の1966年、高速走行中に車軸が折れ、車掌が異常振動に気づき緊急ブレーキをかけて事なきを得た。車軸は1回転ごとに(300km/hでは1秒間に約30回転)繰り返し大きな力を受け、台車枠よりはるかに厳しい条件で使われている。車軸の傷は即重大事故につながるため、全般検査または台車検査で超音波探傷(発信した超音波の反射で判断)を徹底し、疑わしい車軸は惜しげもなく廃棄処分にしている。車軸と比較すれば台車枠は探傷の優先度が低いことは筆者も機械屋であり理解できるが、今回の事故に鑑みて検査体制を見直すことが必要である。
台車枠溶接後の熱処理は適正だったか
ユーチューブ上で、N700系の台車製作の工程(今回の台車とは別のメーカー)が約15分間にまとめて紹介されている。前項で説明した磁粉探傷作業も登場する。機械加工の工程を完全に省略しているなど、全ての工程を網羅しているわけではないが、気になるのは台車枠溶接後の応力除去焼なまし(材料の組織に残った力を和らげる熱処理)の工程が出てこないことである。
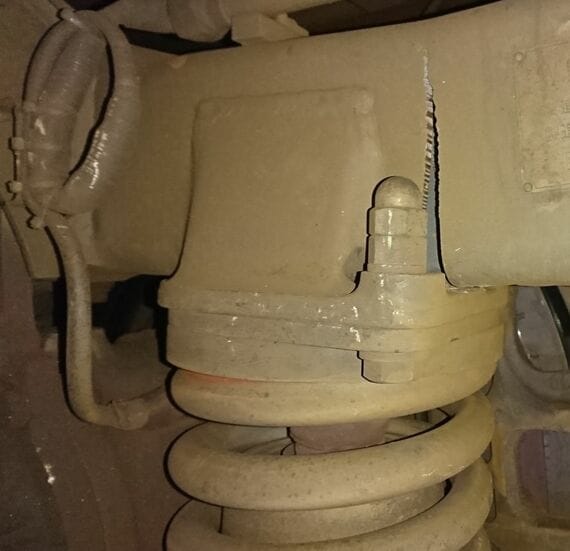
筆者は以前に電車モーターの機構設計をしていたが、外装部品の溶接部分(正確に言うと溶接の肉盛りから少し離れた“二番”と呼ぶ部分)に入る亀裂で苦労した。溶接すると周囲の母材が熱影響を受け、表面に引張(ひっぱり)応力(材料の組織を引き離そうとする力)が残留することがある。モーターのフレームは鋼材を溶接して作るが、残留応力を除去するため炉に入れて比較的低い温度(600~650℃くらい)で焼なましをする。船や橋など巨大な構造物はできないが、台車枠なら可能である。
無料会員登録はこちら
ログインはこちら