30年以上、世界の半導体の現場に身を置いて今も現役で活動する半導体エンジニアが日本や世界の半導体政策や業界動向を解説する。
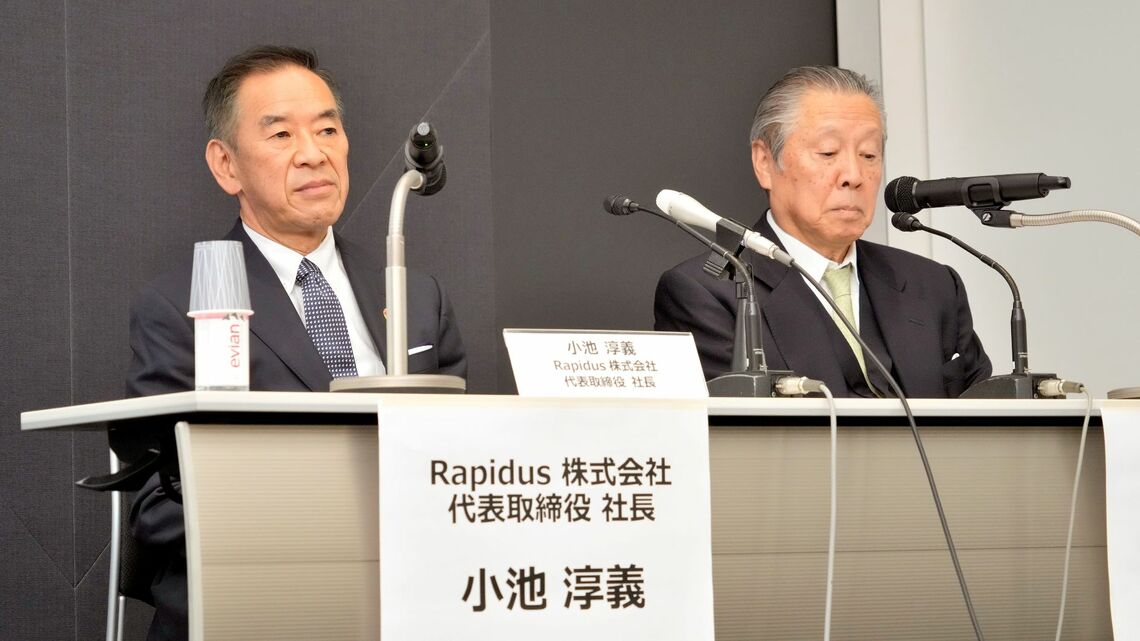
先端半導体製造に向けた国策企業Rapidus(ラピダス)が抱える課題に関して、多くの識者が報道やSNS上で非常に厳しい意見を出している。ただ、具体的に何が障壁なのか説明されているケースがほとんどないようだ。今回はラピダスが抱える課題についてビジネス面と技術面から見解を示したい。
2000年代に失敗したファウンドリー経験
ラピダスについては日立製作所と台湾の半導体受託製造(ファウンドリー)大手である聯華電子(UMC)との合弁、トレセンティテクノロジーズ(TTI)を抜きに語ることはできない。TTIは2000年に設立された。
半導体製造は生産性向上のために製造に使用するウェーハ口径を4インチ、5インチ、6インチ、8インチ(200mm)と拡大させてきた。しかしながら12インチ(300mm)のファブ(工場)建設が具体的に検討され始めた1998年時点では、月産2万枚で少なくとも2000億円の投資が必要とされ、メモリ半導体のひとつDRAMの製造を諦めた多くの日本のデバイスメーカーでは300mm半導体ファブ投資に二の足を踏むところが多かった。
その中で現ラピダス社長である小池淳義氏はウェーハを1枚ずつ処理する枚葉生産を前提とした「短TAT(Turn-Around-Time)」生産を武器に月産7000枚で投資可能なコンセプトを提案。日立単独ではなくファウンドリー経験豊富なUMCを迎え入れて事業を開始した。
この事業は最終的にUMCが手を引くことになり、最終的に日立出資100%となって、今のルネサス主力工場であるN3に繋がる。ただ、TTIが成功しなかった理由が公にされることはなかった。それが今年5月22日に千歳市民文化センターで開催されたラピダスの地元説明会で小池氏が「驕り」のたった一言で統括したことに筆者は驚き、違和感を覚えた。
20年以上前のTTIの話を出したのは、なぜファウンドリーとして設立されたTTIが成功しなかったのか、その反省がどのようにラピダスに生かされているかが重要なポイントだからである。
筆者は当時のTTIが抱えた課題がさまざまに説明されているのは認識しているが、ここでは以下の3点にまとめる。
無料会員登録はこちら
ログインはこちら