実はこの2000年前後に半導体製造工場は大きな変革期を迎えていたのである。
カギはシリコンウェーハ口径の30mm化
大きな変革とは半導体製造に使用するシリコンウェーハの口径が200mm(8インチ)から300mm(12インチ)に大口径化するタイミングだったことを指す。ウェーハ口径は1970年代に4インチ、1984年前後に6インチ、1991年前後に8インチと大口径化が進んできた。
ウェーハを大口径化させていった目的は生産性向上である。つまりチップ当たりのコストを削減するためである。ちなみにシリコンウェーハの口径表記は慣習的にインチを使用することが多いが、業界標準(SEMI)として4インチ以降は「mm」表記が正式である。
それまでのウェーハ口径拡大と異なり300mm化が特殊だったのは、工程間のウェーハ搬送などを業界として世界標準化することになったことである。標準化が目指された背景のひとつには工場の建設コストの高騰がある。
図2に月産2万枚の半導体工場建設費用の推移を示す。200mmまでは数百億円から1000億円程度の建設費用だったものが300mm工場では2000億円(当時)が必要となり、それまで各社が独自の仕様でウェーハを収納する容器や自動搬送システムを共通化することになったのである。
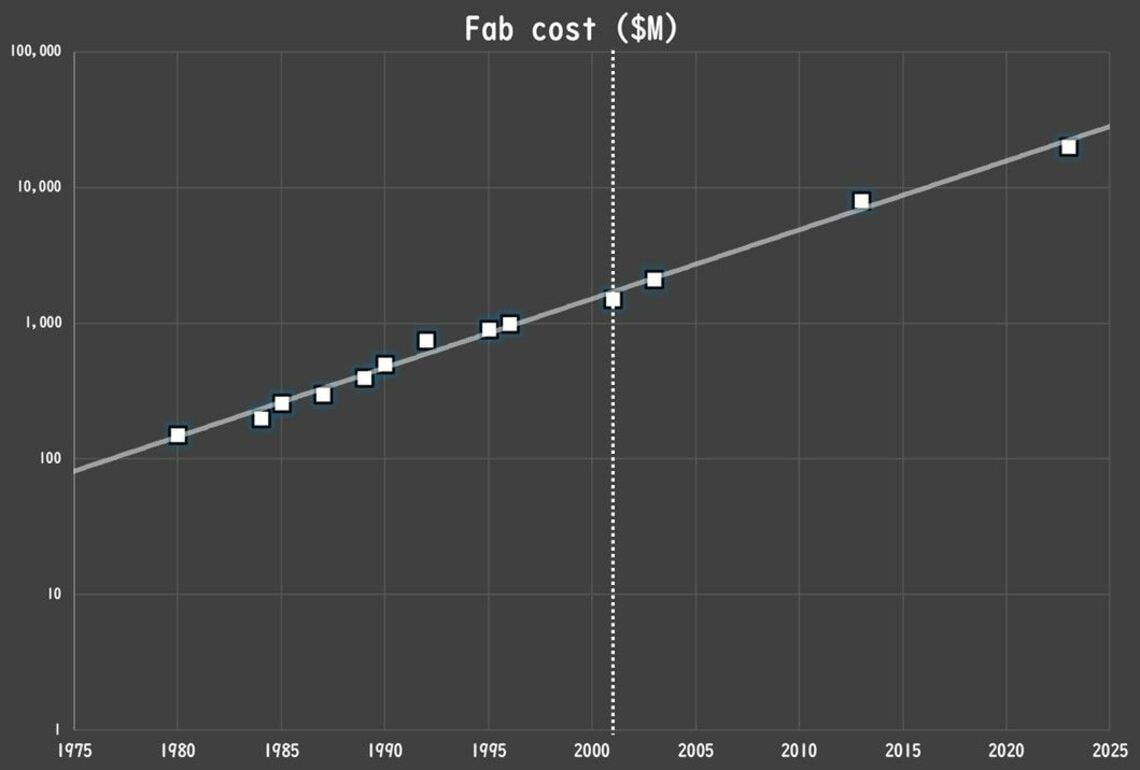
とはいえ、標準化によりコスト削減できる範囲も限られており、300mm工場を建設できる会社は限られた。ファウンドリが大きく市場を伸ばすことになったのはまさにその300mm化のタイミングであった。自社単独で工場投資ができない日本を含めた半導体会社がプロセス開発能力も高めていたTSMCへの製造委託を増やすことになったのである。
かつて日立製作所とUMCとの合弁でできたトレセンティテクノロジーズ(TTI)は、現在ラピダスの社長を務める小池淳義氏が中心となって製造時間を短縮できる短TATをコンセプトとし、工場投資は抑えたが「生産性向上」にはつながらなかった。これに関して興味がある方は「ラピダスが直面する20年の反省と3つの技術課題」を読んでほしい。
無料会員登録はこちら
ログインはこちら