凋落したと言われがちな日本の半導体産業だが、特定の分野では業界標準を主導するなど強みもある。その珍しい事例を紹介する。
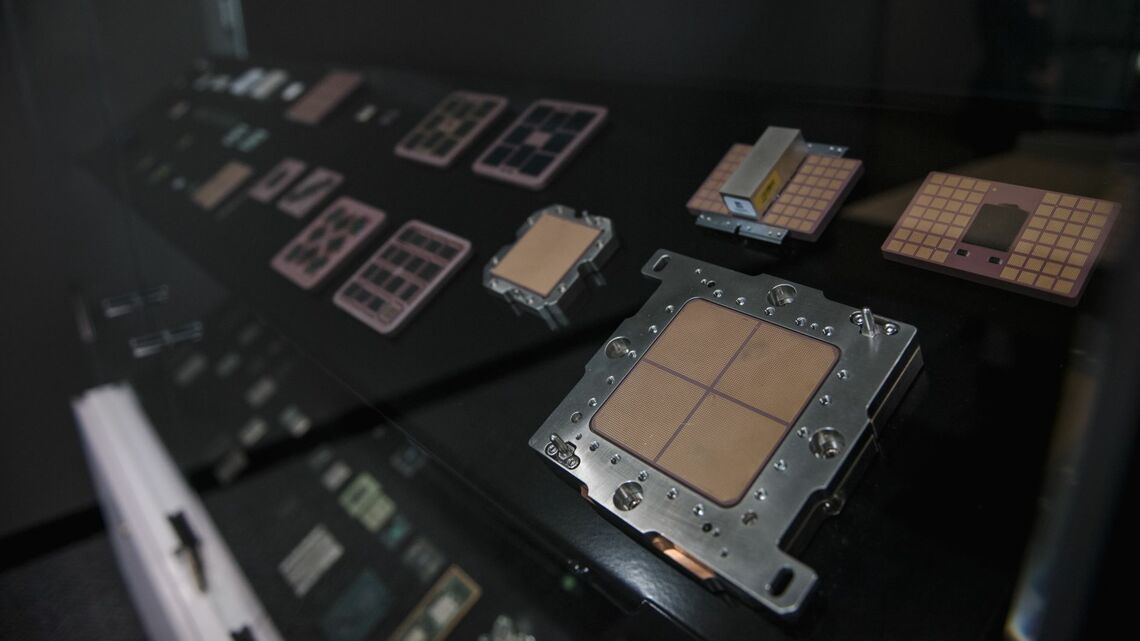
この数年、何かと話題が増えてきた半導体だが、最近は特にパッケージングと呼ばれる製造工程に関して注目が集まっている。
そもそも半導体チップの製造工程は前工程と後工程の2つの工程に分けられる。前工程はウェーハと呼ばれる円盤状のシリコン単結晶素材に、電気の流れをコントロールするトランジスタを作り込み、配線する工程だ。日本の熊本に進出したTSMCは主にこの前工程を手がけ、技術的な強みをもつ。
一方の後工程は、前工程で作られたウェーハから数十~1000個を超える半導体チップを小さく切り出して、配線を行い、樹脂封止した後に検査する工程を指す。この工程を経て、ようやく半導体という製品として出荷される。
近年、複数の機能をもつ半導体チップを積層して組み合わせるなど高度な接続を行うことが増えており、これを先端パッケージング工程と呼んでいる。このパッケージング分野で、実は日本のサプライヤーが健闘している。その状況を専門用語を解説したうえで、紹介したい。
チップレット、2.5D/3D実装とは?
最近何かと出てくる用語に「チップレット」がある。従来の半導体チップは、1つのチップ内に複数の機能を詰め込んでいた。これをMonolithic(モノリシック)と呼ぶ。一方で、機能ごとに個別のチップに分割したものそれぞれをChiplet(チップレット)と呼ぶ。このチップレット同士を接続する技術/製品も同じく「チップレット」と呼ぶことが多い。(図1参照)
記事全文を読むには有料会員登録が必要です。
(残り 2265文字 です)
【9/30(火)まで】 年額プラン2,000円OFFクーポン 配布中!
詳細はこちらから
無料会員登録はこちら
ログインはこちら