クルマが進化するほど求められる技術とは AT多段化、脱エンジンでむしろ増える軸受
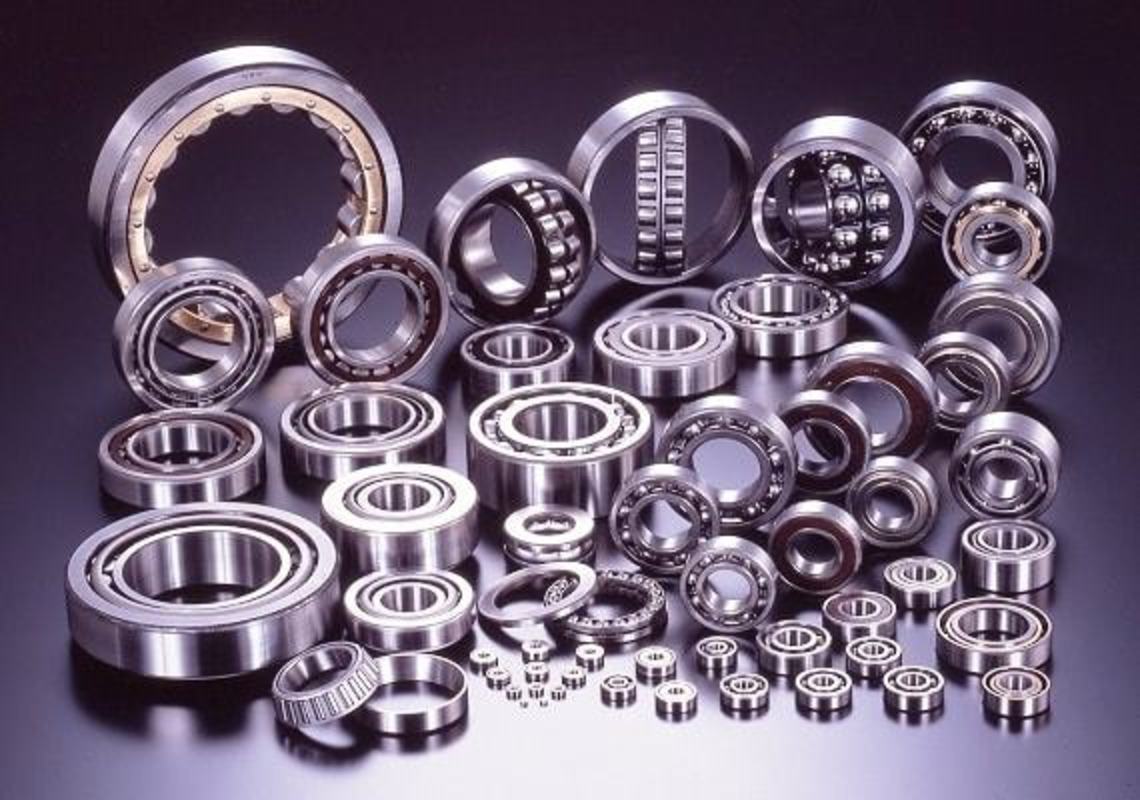
「オートマ車」の変化が、軸受市場に及ぼす影響
――いわゆる「オートマ車」で使用される自動変速機(Automatic Transmission)の多段化が急速に進行し、それによりNSKのAT向け軸受事業が大きく伸びていると報じられています。
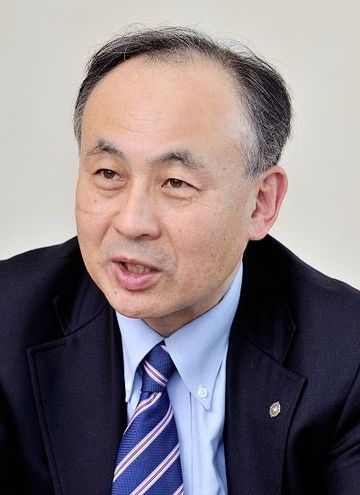
執行役常務
自動車技術総合開発センター 副所長
パワートレイン軸受技術センター 所長
宮崎裕也
5年ほど前まで、ATは6速が標準でしたが、ここ数年で8速も登場し、9速・10速のATを搭載した車種も販売され、今後もATの多段化は進む見込みです。
この多段化するATの中に、当社の軸受が使われています。トランスミッションも「回転」によってタイヤに動力を伝える装置ですから、「回転」を支える軸受が必要になります。多段化によって、AT全体に使われる軸受の個数も増えるだけでなく、1つの軸受に求められる要求が厳しくなります。高付加価値軸受は当社が強みを発揮できる分野で、それが自動車軸受事業の好調につながっています。
――いまなぜAT多段化の波が来ているのでしょうか。
AT多段化には大きく2つの目的があります。環境性能と運転操作性を向上させることです。すなわち、燃費を向上させ、より滑らかな走り、あるいは快適な乗り心地を実現することが求められています。多段化は、はじめは高級車で広まりましたが、いまではクルマへの環境性能要求の高まりを受け、幅広い車種で採用されるようになっています。
――AT多段化によって、軸受に求められる条件はどのように変化しているのでしょうか。
多段化は、AT全体の部品点数増加につながります。それらの部品を従来どおりの寸法や重量のままATをつくると、全体としての寸法や重量も当然増えてしまいます。それは、多段化の大きな目的の1つが環境性能向上であることを考えると、好ましいことではありません。さらに車内の部品設置スペースも限られているため、ATの中で使われている部品を、性能を落とさず小型・軽量化するしか道はありません。
軸受は、回転軸を支える円筒状の部品です。通常の軸受は軸と一体になって回転する内輪、ハウジングに嵌合する外輪、内輪と外輪の間に入って転がる転動体で構成されています。軸が回転すると内輪あるいは外輪と転動体の間で、摩擦が発生します。燃費向上のためには、エンジンで発生させた動力を無駄なくタイヤに伝えられるよう、軸受の摩擦・摩耗を制御することが重要です。つまり、小型・軽量化とあわせ、高性能化も求められているのです。こうした厳しい条件に応えられる軸受メーカーは、世界でも限られています。
100年以上、軸受を見てきたからこその技術の強み
――NSKの軸受が、それほどまでに強みを発揮できる理由はどこにあるのでしょうか。
軸受は、回転軸を支えるとともに、内輪や外輪と転動体との間で起こる摩擦や摩耗を制御して、機械の効率や寿命、信頼性を高める要素部品です。エンジンにしろ、モーターにしろ、タイヤにしろ、機械が回転するところに軸受は不可欠で、日本人の主食になぞらえて「産業のコメ」とも言われます。この軸受は、地道な技術の蓄積がものを言う部品です。新規参入して一朝一夕に、顧客要求を満たせる製品をつくれる世界ではありません。
当社は日本国内で初めて、軸受の中で最も標準的といえる「玉軸受」を開発しました。それが1916年のこと。以来100年を超え、軸受の開発・製造を中核事業として展開しています。創業当初から自動車用の軸受の開発・製造に携わっているほか、鉄道車両用、ジェットエンジン用、火力発電用といった大型の軸受から、カメラや歯科治療器具の内部で使うミニチュアの軸受まで、サイズや用途もさまざまな軸受を開発し、国内の軸受市場を切り拓いてきました。1963年に開発した東海道新幹線用の軸受、2010年の人工衛星姿勢制御用の軸受も、国内初の成果です。こうした技術の蓄積が、今日さまざまな要求に応えられる力につながっています。
――NSKが培ってきた技術の蓄積は、具体的にどの辺りにあるのでしょうか。
当社が掲げる「4つのコアテクノロジー」が、100年を超す歴史で培ってきた強みです。
1つ目が「トライボロジー」。運動しながら接している物体どうしの表面で起こる摩擦や摩耗を制御する技術です。古代メソポタミアの「巨石の下に丸太を敷いて軽い労力で運ぶ方法」に由来しています。2つ目が製品の耐久性を大きく左右する「材料技術」。3つ目が、コンピュータ・シミュレーションによって製品の性能を仮想的に試験・評価する「解析技術」。4つ目が、機械技術と電子制御を最適な形で組み合わせる「メカトロ技術」です。
このうち「メカトロ技術」は、同じ自動車部品でも電動パワーステアリングシステム(EPS)のような複合製品の開発で重要な技術であり、軸受の開発・製造にとって重要なのは、「トライボロジー」「材料技術」「解析技術」の3つです。当社は、生産こそしていませんが軸受の材料となる特殊鋼や油などを、独自で開発・解析する環境を整えています。つまり軸受メーカーでありながら、材料や素材へのニーズ・シーズを社内に有しているため、高品質な製品を、早い開発サイクルで提供できるという強みがあるのです。
「脱エンジン」を見据え、クルマと軸受はどう変わるか
――近年は、EVやFCVのように「エンジンを持たないクルマ」も市場に出回り始めています。環境性能への要求が高まると、いずれはEVやFCVが主流になるのではないでしょうか。
たしかに、長期的には「脱エンジン」の動きが広まっていくでしょう。温暖化対策で環境規制が強まると、その動きは加速すると予測されます。ただし、それはあくまで長期的な動きです。さまざまな市場予測によれば、少なくとも今後10年ほどは、エンジン搭載車がクルマのメインストリームであり続け、その販売台数も増えていくと見込まれています。その後は、環境規制の方向性によって、エンジン搭載車の比率がどう変化するかの見方は割れますが、新興国を中心にクルマの販売台数は増え続けるという点は、どの予測も共通しています。
――その動きを、NSKとしてはどのように評価されているのでしょうか。
現状、一台のクルマに100~150個ほどの軸受が使われています。エンジン周りで40~60個ほど、トランスミッションに代表される動力伝達系で30~60個ほど、タイヤ周りを含むシャシ系で10個ほど。それが、軸受が使われる主要な箇所です。今後10年ほどは、エンジン搭載車が主流で、その販売台数も増えていきますから、全体として軸受需要の伸びが期待できます。特にトランスミッション周りはAT多段化の流れを受け、一台あたりの軸受数も増えます。要求仕様が高度になれば、技術の蓄積のある当社がさらに強みを発揮できます。
注目すべきはその後の展開です。タイヤ周りの軸受需要は、クルマの販売台数増加によって増えるとしても、「脱エンジン」の動きが急速に進むとすると、エンジン周りと動力伝達系で使われていた軸受への需要が減少していくのは否めません。
ただし、動力源がモーターに置き換わることにより、軸受に対する新たな需要も生まれてきます。需要が減るものもあれば新たに生まれてくるものもある、ということです。
自動車軸受のこれからを支える人材像とは
――新たに生まれてくる需要で、減少した需要を補えるということでしょうか。
モーター駆動車が具体的にどのような形で世に広まっていくかにもよりますが、その可能性はありうると考えています。
たとえば、タイヤ(ホイール)にモーターを組み込んだ「ホイールハブモーター(一般にはインホイールモーター)」は、将来のモーター駆動車の大本命と言われます。この実装方式として、モーターに減速機を組み込む形が考えられます。その減速機構は、ATで使われているものと原理的に同じ仕組みで動作するものです。モーターにも減速機にも軸受は不可欠で、それがタイヤごとに増えるとなれば、むしろ需要が増加していく可能性は十分にあります。
――大きな変化の時代、NSKはどのように対応していかれますか。
近年は、軸受製造に求められることが変わってきました。かつては軸受を突き詰めていけばよかったのですが、今や軸受だけを見ていても「良い軸受」はつくれません。
背景にあるのは、環境性能への要求の高まりです。軸受に小型・軽量化が求められるのと同じく、軸受が支える回転軸や、軸受を格納するハウジングと呼ばれる部品も小型・軽量化が進んでいます。かつては、軸やハウジングには十分な強度があると想定しておけば事足りましたが、これらの部品の強度も変わってきます。使用条件によっては、部品が変形したり歪んだりすることも想定し、それでも壊れない軸受をつくることが求められるようになっています。
そういう「良い軸受」をつくるには、軸受がどのように使われているかを俯瞰でとらえる広い視野が必要です。クルマが全体としてどう動いているか。トランスミッションがどういう仕組みで力を伝達するか。物事をトータルに把握できる力を持った人材が、急速に必要になっています。
軸受は、クルマの「回る」を支える不可欠な部品です。そのさらなる進化に携わりたいという意欲を持った新たな仲間を求めています。