クルマの「あたらしい動き」をつくる
エンジニアたちの挑戦
日本精工の次なる100年を生み出す原動力
ステアリングシステムの
「これまで」と「これから」
ステアリングシステムは、クルマの「曲がる」を実現するために、なくてはならない重要な部品だ。運転者のハンドル操作によって加えられた力を伝達し、その力でタイヤの向きを変え、車体が進む方向を変える。しかし車体の重量が増すほどハンドル操作が重くなるため、そのアシストのためにパワーステアリングシステムが開発された。
最初に普及したのは、油圧式のパワーステアリング(HPS)だ。エンジンの出力を利用して油圧ポンプを作動させ、その圧力でタイヤの向きを変える力をアシストする。しかし、ハンドルは軽くなるものの、常にポンプを動かすために燃費の面で難点があった。
モーターの力でタイヤの向きを変える電動パワーステアリング(EPS)は、このHPSの弱点を補う形で1988年に市場に投入された。ハンドル操作が必要なときだけモーターを駆動するため、エンジンのパワーロスが少ないのが特徴だ。しかし初期のEPSは油圧式と比べ、アシスト出力を大きくするのが難しく、まずは軽自動車や小型車から広まった。その後、高出力のEPSが登場、2000年代に入ると環境意識の高まりをきっかけとして、中型車や大型車にも搭載されるようになっていく。
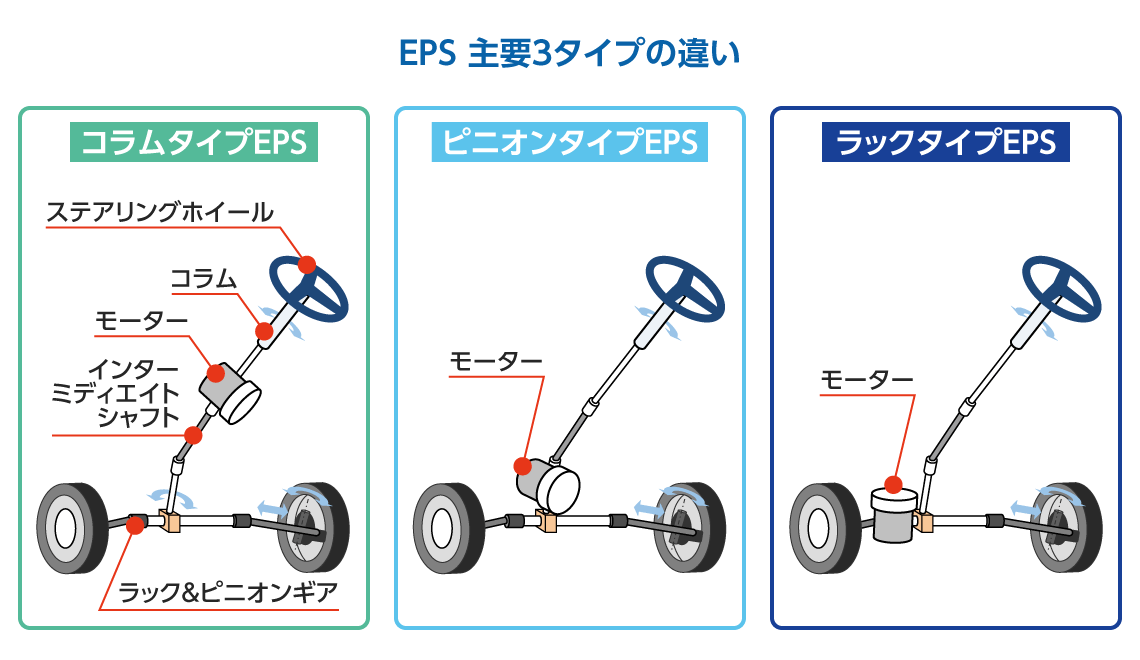
EPSとひとくちに言っても、ステアリングシステムのどの部分をアシストするかで大きく3つのタイプがある。
まず、軽自動車や小型車に搭載されたのが、コラムタイプEPSである。その後、モーターの高出力化によってコラムタイプの適用範囲が広がっていくのと並行して、ピニオンタイプやラックタイプも開発され、中~大型車にもEPSが搭載されるようになってきた。
コラムタイプは、2015年の出荷台数ベースでEPS市場の過半数を占め、今後も新興国や欧州を中心に市場規模の拡大が見込まれている。加えて、これから大きな伸びが期待されているのがラックタイプEPSだ。前述のとおり環境意識の高まりや操舵感の改善を背景に、中~大型車向けの搭載が増加してきている。
ステアリング開発の
「あたらしい動き」
NSKは、ステアリングメーカーのなかで先駆けてEPSに取り組んだ企業のひとつだ。1986年にフォークリフト向けに世界で初めてEPSを開発し、1988年には軽自動車向けのEPSを市場に投入した。その後も、先行者の強みとノウハウを活かしてEPS市場を開拓してきた実績がある。
NSKが得意とするのは、コラムタイプEPSである。市場拡大を見越して開発資源を集中し、市場の波に乗って事業を拡大させた。1916年に軸受メーカーとしてスタートしたNSKにとって、今や自動車関連事業は堂々たる中核事業であり、なかでもステアリング事業は大きな柱となっている。NSKのEPSは、小型・高出力が強みであり、「世界最小・最軽量」のコラムEPSをこれまで幾度も市場に投入してきた。前述のとおり、コラムEPSは今後も成長が見込まれる有望市場であり、NSKの収益を支えていくことだろう。
2016年11月8日に、NSKは創業100周年の節目を迎えた。次の100年を力強く歩み出すべく、2026年までの10年で「あたらしい動きをつくる。」ことをビジョンとして掲げ、ステアリング事業でも、「あたらしい動き」が生まれている。コラムEPSに並ぶ事業の柱をつくるべく、大きな成長が見込まれるラックEPS市場への参入を目指し、開発プロジェクトが始動しているのだ。
自動車技術総合開発センターの萬雄介氏と川井康寛氏は、このラックEPSの開発に取り組むエンジニアだ。両氏はそれぞれ、機械(メカ)とECU(電子制御ユニット)の設計・開発を担当する。
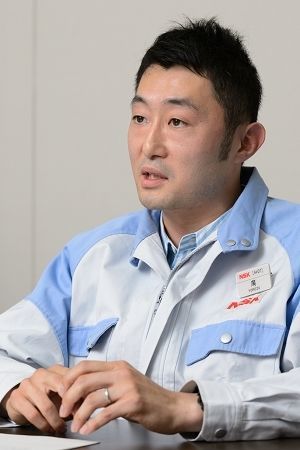
自動車技術総合開発センター
ビークルダイナミクス技術開発部
副主務
萬雄介
萬氏は、NSKがラックEPSの開発に乗り出した背景を次のように語る。
「ラックタイプの市場拡大が見込まれることに加え、主要部品の開発に、当社の強みを生かせることが理由として挙げられます。当社はもともと軸受メーカーとして始まった企業で、今も機械要素部品である軸受やボールねじを生産しています。このボールねじが、ラックアシストを実現する主要部品として使われています。ラックEPSを先行して開発している他社は、このボールねじをサプライヤーから購入しているようですが、当社は自社で開発することができます。同じことが、ボールねじを支持する軸受にも当てはまります。これらの専用に開発したボールねじや軸受に加え、当社の部品メーカーとしての総合的な技術力を集結させることにより、スムーズなアシストや小型化・軽量化を実現し、あるいはコスト面での優位を出せると考えています」
ボールねじの役割は、ねじ軸とナットの間にボールを入れ、回転運動と直線運動を相互に変換することにある。ラックEPSにおいては、ラックに取り付けたナットを、水平方向の位置を固定したままモーターで回転させる。それによってラックが水平方向に移動し、タイヤの向きを変えるアシスト力になる。萬氏によれば、ラックEPSの開発のポイントは、ボールねじの作動性をいかに出せるかにあるという。
「ボールとねじ軸・ナットの間には摩擦が発生し、それをうまく制御することが、スムーズなハンドル操作を実現するカギを握ります。先行他社は、まさにその点で苦労しているようですが、当社には、1916年の創業以来、軸受の開発で築き上げてきた摩擦制御のトライボロジー技術の蓄積があります」
この技術の厚みを最大の武器に、EPSの次なる有望市場の開拓に乗り出しているのだ。
クルマの「頭脳」が背負う課題
一方の川井氏が取り組むのは、EPSの電子制御を行う「ECU(電子制御ユニット)」の開発だ。ボールねじがラックEPSにおけるメカの心臓部なら、ECUはそれを動かす頭脳と言える。トルクセンサーが検出したハンドルに加えられた回転力と、車速などの車両情報を入力として、違和感のないスムーズな曲がりを実現するため、最適なアシスト力を演算してモーターの回転を制御する。
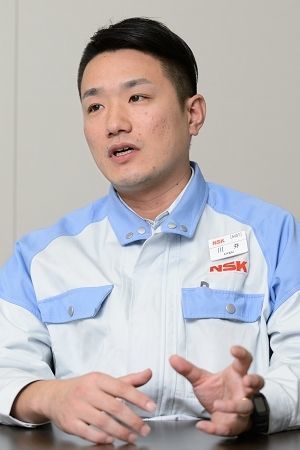
自動車技術総合開発センター
ビークルダイナミクス技術開発部
川井康寛
コラムEPSとラックEPSで、ECUが担う機能にそれほど大きな差はないと川井氏は言う。だが、ECUの設置場所の違いが、ECUの動作環境要件の違いになってあらわれる。
「アシスト機構一式が車室内に設置されるコラムタイプに対し、ラックタイプではエンジンルームに設置されます。車室内のECUは、雨水やエンジンの放熱にさらされることもなく、路面の振動もタイヤのサスペンションのおかげで大きく軽減されます。それがエンジンルームに変わるだけで、耐水・耐熱・耐振動のすべてにおいて、ECUに求められる要件が厳しくなります」
さらには、クルマの電子化の進展に伴い、ECUに求められる要件が増大している。EPSがそうであるように、クルマの諸機能は、いまや電子部品抜きには成り立たない。クルマの電子化は、メカ部品の細やかな制御を可能にし、クルマの高機能化という恩恵をもたらした一方で、電子部品の故障や誤作動によってクルマの機能が停止し、重大な事故を引き起こすリスクをクルマに内在させることになった。
そうしたリスクを回避するため、クルマの安全性に関する国際標準規格が定められた。電子システムが機能不全に陥った場合でも、ドライバーや乗員、交通に支障を来さずにクルマが走行できることを求めた「機能安全」の国際標準規格「ISO26262」である(2011年11月制定)。ECUの機能安全対応も、開発の大きなポイントだと川井氏は述べる。
「クルマの『曲がる』を担うステアリングシステムは、重要保安部品です。緊急時でも、運転者の意図する通りに車体の向きを変える機能を維持しなければなりません。機能安全の要件を満たすため、ECUの回路を二重化する対応を進めています。難しいのは、エンジンルームの中で、EPSに与えられるスペースが限られていることです。限られた空間で回路の二重化を実現するため、半導体モジュールを導入し、回路そのものの小型化に取り組んでいます。ところが今度は、回路の小型化が別の問題を引き起こします。回路の配線や素子間の距離が近くなり、熱の影響を受けやすくなります。いかに熱を逃がすか、あるいは熱に耐えられるようにするかを、小型化とあわせて検討しています」
自動運転時代を見据えた
ステアリングの「あたらしい形」
ラックEPSの開発が、新たな100年の始まりの5年10年先を見据えた「あたらしい動き」であるならば、自動車技術総合開発センターは、より長いスパンで未来を見据えた先行開発にも取り組んでいる。その役割を担うのが、同社の松田靖之氏と郡司大輔氏の二人だ。両氏はステアリングシステムに留まらず、自動運転が引き起こす変化も見据え、クルマの「あたらしい動き」をつくる種まきに余念がない。
自動運転には、いくつかの段階がある。国やメーカー、人によっても捉え方がまちまちだが、内閣府は自動化のレベルを4段階に分けて定義している。
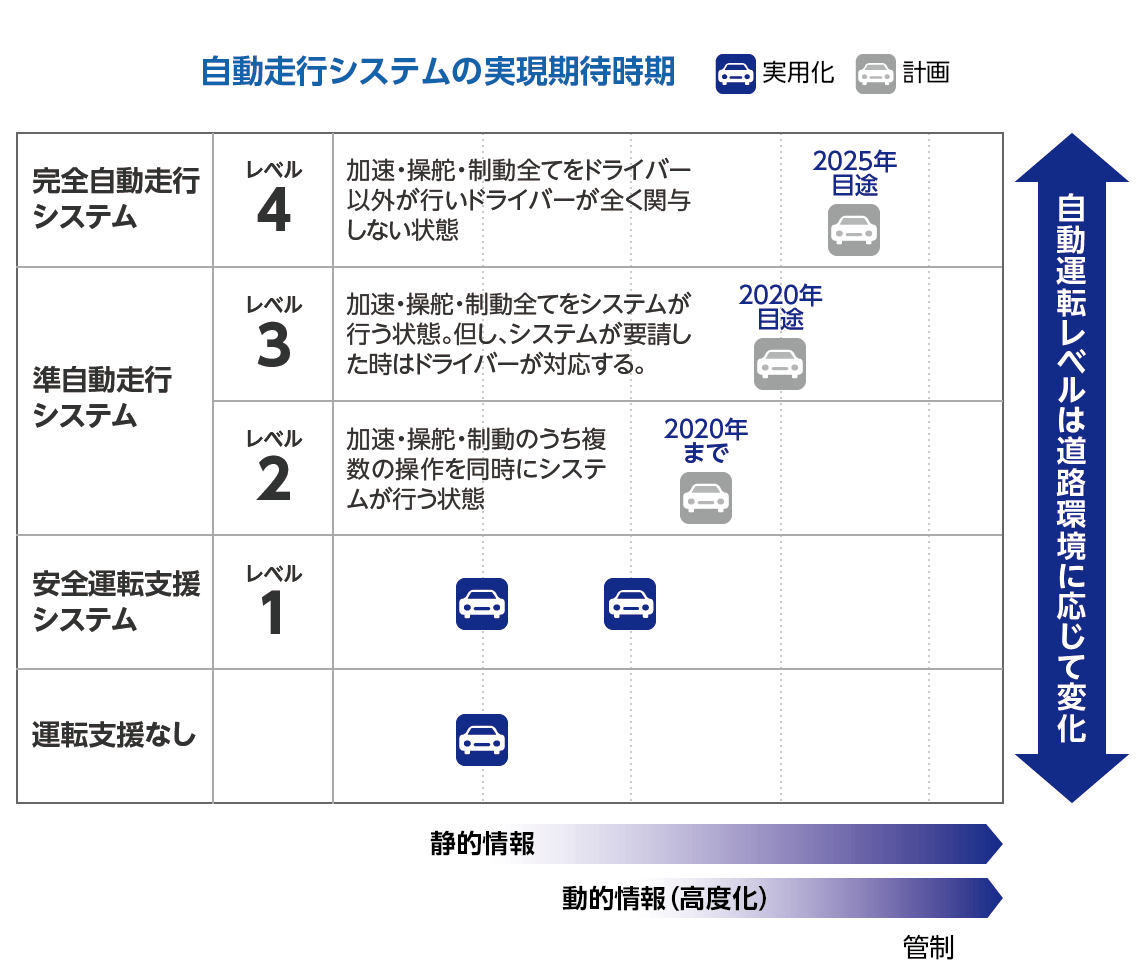
出典:内閣府 戦略イノベーションプログラム 自動走行システム 研究開発計画(平成28年6月23日)
レベル1と2は、「自動運転」というよりも、「運転支援」と捉えた方がしっくり来るかもしれない。衝突回避のための自動ブレーキはレベル1に、渋滞時、ブレーキやステアリングの制御をシステムが行い、車間や車線を維持する「クルーズ・コントロール」はレベル2に該当するとされる。いかにも「自動運転」らしく、人が運転操作をしなくとも、クルマが自律的に走るのはレベル3以降である。「加速・操舵・制動」、すなわち「走る・曲がる・止まる」のすべてをクルマが行うが、システムの要請により人間が運転を引き継ぐのがレベル3、人間の操作をまったく必要とせず、クルマが完全自律走行するのがレベル4と定義される。
なお、2016年末時点では、レベル3以上のクルマはまだ販売されていない。「自動運転」を連想させるクルマが販売されてはいるが、それらはいずれもレベル2に該当する。技術面での課題に加え、自動運転車で事故が起きたときに誰が法的責任を負うか、法律の整備もこれからだ。市販の自動運転車が公道を走るようになるには、もう少し時間がかかる見込みだ。
レベル3以上の自動運転車がいつ市場に投入され、社会にインパクトを与えるレベルにまで普及するか――。クルマの未来予測は、メーカーや人によってさまざまだ。技術の発展や法整備、自動運転のベネフィットとリスクを、社会がどのように評価するかによって、市場投入のタイミングや普及速度は大きく変わってくる。
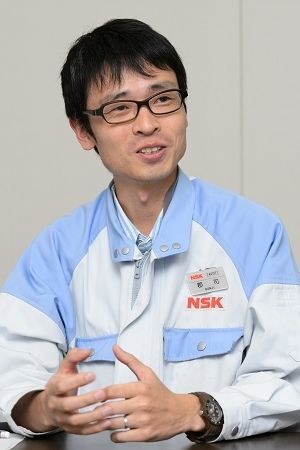
自動車技術総合開発センター
ビークルダイナミクス技術開発部
副主務
郡司大輔
「いつ」とは断定できないにせよ、自動運転車が市場に投入される日がいずれやって来るのは間違いないだろう。そのときクルマの「曲がる」はどのように変わっていくか、郡司氏はまずレベル3での見通しを次のように語る。
「個人的な感想として、システムがときどき自動運転を諦めるレベル3は、中途半端な印象が拭えません。レベル3対応車が広く受け入れられるかは疑問があります。そういう留保はあるにしても、自動運転が基本になれば、ステアリング周りも変わっていく可能性は十分あります。ときおり人が運転操作をしなければならないとはいえ、自動運転中に運転席の目の前にハンドルがあるのはいかにも邪魔です。ハンドルほど邪魔にならず、それでいて場所をとらず、なおかつ人がすぐに運転を引き継ぐことができる。そういう形の新しいインターフェイスが生まれてくる可能性があります」
ハンドルに代わる操舵のためのインターフェイスの候補として、松田氏は次のような見解を示してくれた。
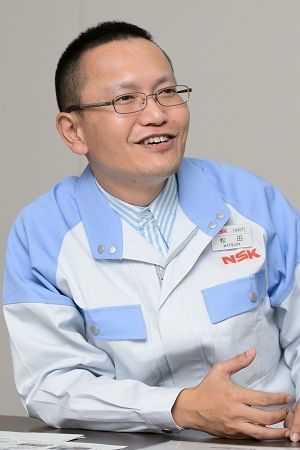
自動車技術総合開発センター
ビークルダイナミクス技術開発部
グループマネジャー
松田靖之
「形としては、ジョイスティックや、飛行機の操縦桿に使われるバーハンドルのようなものが考えられます。そのとき、クルマをどれだけ曲げるかを決めるのは、スティックやバーを傾けた角度ではなく、それらに加えた力の大きさを力覚センサーで判断する可能性もありえます。この方法ですとインターフェイス周りのメカの構造もシンプルになりますし、見た目の形状が変わったとしても、動作原理は今の技術をそのまま生かすことができます。さらに言えば、レベル4の世界では、そもそもの操作のあり方自体が変わり、極端な話、軽く手で押したり、声で指示を出したりといった、より直感的な操作方法さえありえます。現状の延長線上にあるものだけでなく、こういった新たな可能性について考えていくのも、われわれの仕事です」
部品メーカーのNSKが、
なぜ試作車をつくるのか
レベル4が実現すると、クルマの「曲がる」は、よりドラスティックに変わりうる。
「人がクルマを操作する必要がなくなれば、クルマに運転席もハンドルも必要ありません。クルマからハンドルを取り払い、そこに人や荷物を乗せるロボットタクシーや無人宅配車のような形態の乗り物、あるいはサービスが生まれてくることは十分に考えられます」と、郡司氏は語る。
このとき、無人自動走行車の駆動・操舵装置として有力視されているのが、タイヤのホイールハブのなかにモーターを組み込んだ「ホイールハブモーター」(一般的にはインホイールモーター)だ。モーターの回転でタイヤを駆動させられるのはもちろんのこと、左右のタイヤの回転数を変えることでクルマの向きを変えることもできる。
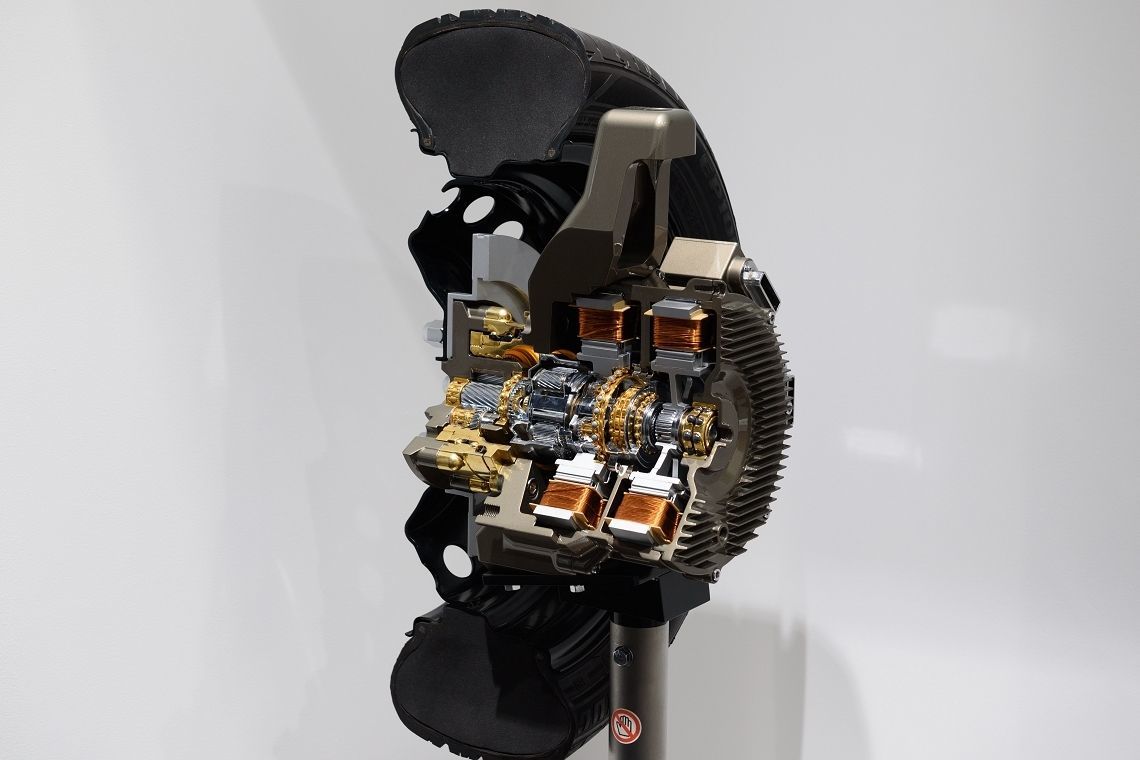
ただ、ホイールハブ周辺の限られたスペースに設置可能なモーターで、重いクルマを動かす駆動力を得るのが技術的な課題とされてきた。松田氏と郡司氏の二人は、この課題を克服する画期的なホイールハブモーターの開発に成功した。小型のモーター2つと変速機を組み合わせ、走行条件にあわせて低速・高速を切り替えられるようにしたのだ。さらには、ホイールハブモーターの性能検証のため、このモーターをクルマの前輪に搭載したコンパクトカーと同等サイズの試作車も独自開発した。
「ホイールハブモーターというと4輪すべてにつけるイメージがありますが、それだとクルマ全体のコストや重量を押し上げることになってしまいます。多くのエンジン車と同じように前輪2輪にだけモーターをつけ、それでクルマを走らせることを目指しました。試作車は最高時速135kmで走行可能です」と、郡司氏は試作車開発の狙いを明かす。
「さらに」と松田氏は言葉をつなぐ。「私たちは、ホイールハブモーターや、それを搭載した試作車までつくっていますが、それらを売り物にしようと考えているわけではありません。当社はあくまで要素部品メーカーだと考えています。自動運転が普及し、クルマの『曲がる』を実現する技術が変わっても、メカニカルな要素部品がなくなることはありえません。ただし、要素部品に求められるスペックは今と変わっていくはずです。その変化をいち早く予測するため、自分たちでモーターやクルマをつくっているのです」
松田氏と郡司氏の二人は、世界の完成車メーカーの研究開発部門と一緒に、クルマの「あたらしい動き」づくりに取り組んでいる。思いついたアイデアをもとに試作品をつくり、完成車メーカーを訪ね歩いて反応を見ながら、未来をこの手に手繰り寄せていく。それができるのは、NSKが、どの「系列」にも属さない独立系の部品メーカーであるからだ。どの完成車メーカーに対しても気兼ねなく、提案を持って行くことができる。
そこには、先行開発ならではの苦労もある。
「あれこれアイデアを出して試作品をつくり、そこから売上につながる量産品に育っていくのはごくわずかです。それでも、何が起こるか分からない未来に備え、引き出しを増やしておく。それが先行開発のミッションです」と松田氏。
そんな彼らの合言葉は「DIY」。「Do It Yourself」と、「ダメでいいからやってみよう」を掛けている。数多くの挑戦のなかから、クルマの未来を切り拓く「あたらしい動き」が産まれてくるのだ。
クルマの「あたらしい動き」を
ともにつくる
NSKは、クルマの「あたらしい動き」をつくるエンジニアを募集中だ。記事の最後に、今回登場いただいた4氏から、未来の同僚に向けたメッセージを紹介したい。
「メカや電子回路の開発といった地道なエンジニアリングから、アイデアを思い描いて形にしていく先行開発のような仕事まで、ここにはさまざまな開発業務があります。これまでの経験を生かしつつ、あたらしいことにも挑んでみたい人にはぴったりの会社だと思います」(萬氏)
「当社は軸受メーカーとして、“摩擦”とうまく付き合ってきた企業です。摩擦を恐れず、既存の枠組みにもとらわれず、当社のビジョンにあるように、あたらしいことに果敢に挑戦していける人に、ぜひ来てほしいですね」(川井氏)
「クルマに関わる仕事をしていますが、クルマの運転は好きではありません。自動運転の普及に向けて、そういう視点も生きてくるはずだと今の仕事に取り組んでいます。私のように、人と違う意見や視点を持っている人と、ぜひ一緒に働きたいですね。そのあたらしい視点が、クルマの『あたらしい動き』をつくることになるはずですから」(郡司氏)
「これからクルマがどうなって行くか、結局のところは誰にも分かりません。今から10年、20年もすると大きな形が見えてくるでしょうが、今ならその流れを、自分たちの手でつくり出すこともできます。ぜひ私たちと一緒に、クルマの未来を切り拓いていきましょう」(松田氏)
軸受メーカーから始まったNSKが、今では自動車部品を主力製品として手掛けているのは、あたらしいことに挑んでいく気概が、企業風土として根付いているからだろう。
今まさに、クルマは激変期を迎えている。この時期に自動車部品の開発に携わるのは、未来のクルマのスタンダードをこの手でつくれるかもしれない千載一遇の好機だ。進取の気性に富んだNSKでなら、そのチャンスも数多く訪れることだろう。
未来のクルマのつくり手になれるかどうかは、あなたの選択にかかっている――。