軸受メーカーのステアリングシステムが、 なぜ世界で受け入れられるのか? クルマの未来を切り拓く、部品メーカーの底力
クルマの「曲がる」を実現する、
"ステアリングシステム"解剖!
電動パワーステアリング(EPS)とは、電気モーターを使ってドライバーのハンドル操作をアシストし、快適かつ安全な運転をサポートするシステムのことだ。旧来型の油圧式パワーステアリング(HPS)と比べて燃費性能や細かな制御、環境負荷の低減に優れ、1980年代終わりにEPSが登場して以来、急速に普及してきた。
ひとくちに「EPS」と言っても、ステアリングシステムのどこにモーターを取り付け、何をアシストするかで大きく3つのタイプに分かれる。まずは本題に入る前に、ステアリングシステムとEPSの概略を押さえておきたい。
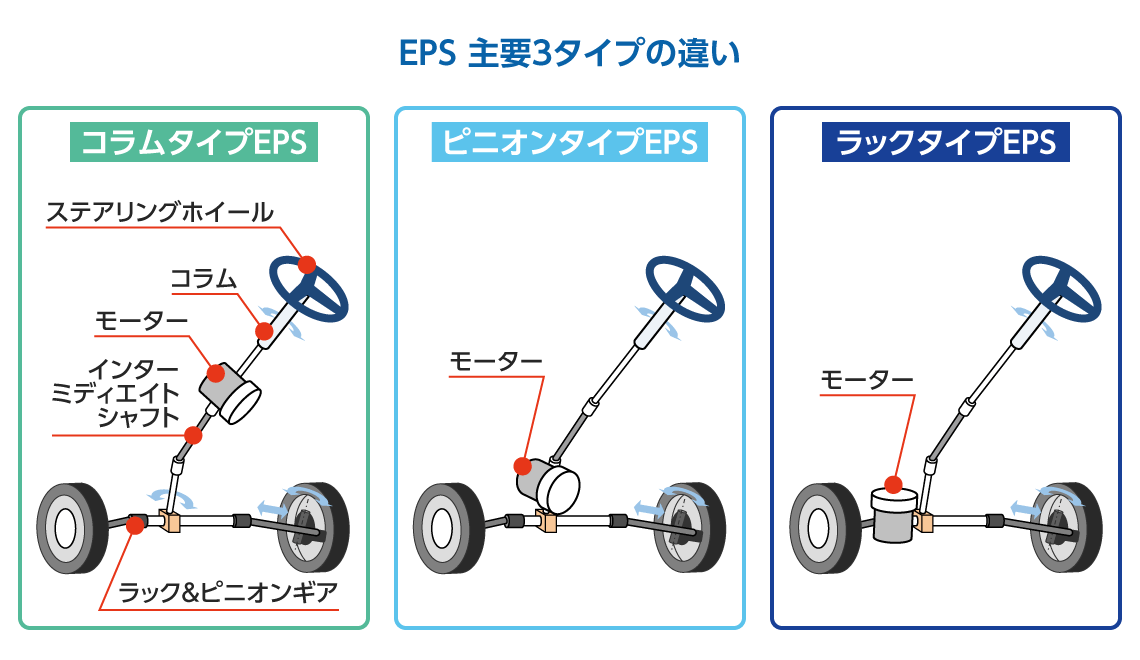
ステアリングシステムは、図で示すような構造をしている。要素部品の主要なものを車室側から見ていくと、ドライバーがステアリング操作を行うための「ステアリングホイール」、いわゆる「ハンドル」があり、その下に、ハンドルを固定する「ステアリングコラム」がある。最もタイヤに近い箇所には、左右のタイヤをつなぎ、タイヤの向きを変える役割を担う「ラック&ピニオン」というギアがある。そして、ラック&ピニオンとコラムをつなぐ中間にあるのが「インターミディエイトシャフト」だ。
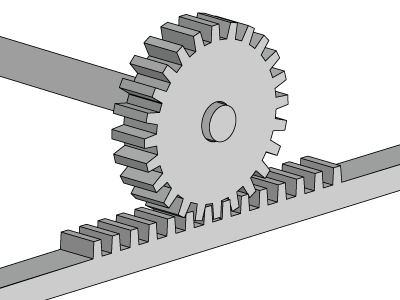
なお、ラック&ピニオンは、円盤状の歯車であるピニオンギアと棒状の歯車であるラックから成る機構だ。シャフトの回転運動がピニオンギアに伝わり、ピニオンギアが回転するとラックの棒状の歯車が直線に動く。すなわち、回転運動が直線運動に変換される。この場所で、ハンドル操作の回転がラックの直線運動に変換され、タイヤに力が伝わって向きが変わる仕組みだ。
EPSの場合は、ここに3つの要素部品が付け加わる。ハンドルに加えられた力(トルク)を検出する「トルクセンサー」と、センサーが検出したトルクや車速などの車両情報をもとにアシスト力を計算する「ECU(電子制御ユニット)」、そして、ECUの演算結果を物理的な力に変換する「モーター」の3つだ。すなわち、「ハンドル」と「トルクセンサー」は入力装置として働き、「ECU」は演算装置として、「モーター」は出力装置として機能する。これが、EPSのおおまかな全体像だ。
世界に広まる
「コラムタイプEPS」とは?
EPSのタイプは、これらの要素部品が、ステアリングシステムのなかのどの部分に配置されるかで決まる。コラムの近くに置かれるのが「コラムEPS」、ラック&ピニオンギアのラック部分に取り付けられるのが「ラックEPS」、ピニオンギアに設置されるのが「ピニオンEPS」だ。
NSKは、このうちコラムEPSを得意としてきた。1991年に業界のなかでいち早くコラムEPSを軽自動車に投入し、今ではコラムEPS市場で世界トップクラスのシェアを占める。
コラムEPSは、トルクセンサーとECU、モーターが車室内のコラムのすぐ近くに設置され、モーターがインターミディエイトシャフトの回転をアシストする。ラックEPSやピニオンEPSがボンネット内に配置され、タイヤに近い下流でアシスト力を加えるのとは対照的だ。
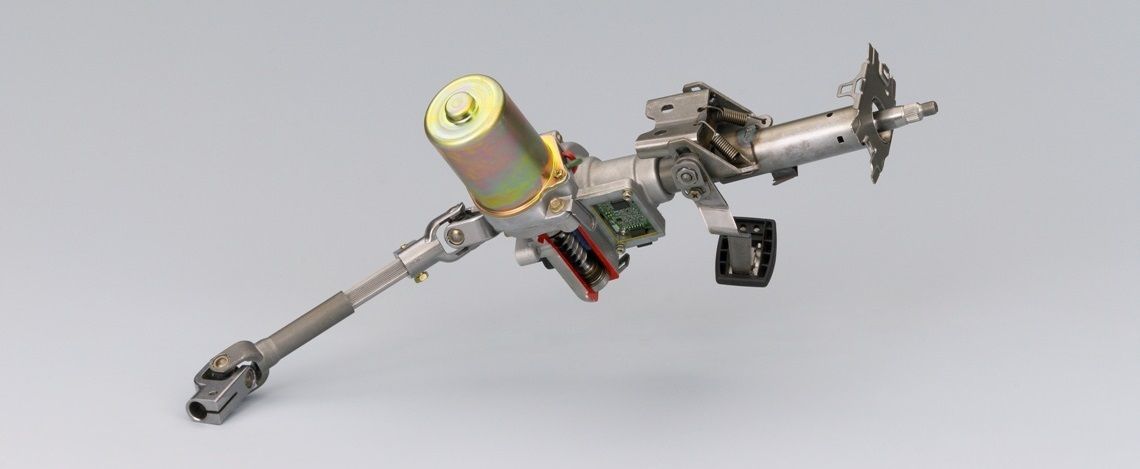
コラムタイプの構造面での特徴が、そのままコラムタイプの利点につながる。室内に設置するため防水設計が不要で、安価に製造可能であることに加え、エンジンやミッションまわりのレイアウトをコンパクトに納めることができる。そのため軽自動車や小型車に多く搭載され、新興国や先進国での小型車ニーズの高まりもあって、2015年の市場規模で、コラムタイプがEPS搭載車の過半数を占める。今後も継続的な成長が見込まれる有望市場だ。NSKは、こうしたコラムEPSの市場拡大の波をうまくとらえ、成長の弾みをつけた。
EPS全般の話として、車体が大きくなるほど高いアシスト力が必要になり、それにはアシスト機構を下流のタイヤ近くに設置するのが望ましい。アシスト機構を車室内(運転者に近い上流側)に配置するコラムタイプでは、高出力を得るのは難しいとされるが、NSKのコラムEPSはその「常識」に果敢に挑み、小型乗用車以上の中型乗用車カテゴリーまでをカバーする高出力化を実現している。それと同時にシステムの小型化にも力を入れ、「世界最小・最軽量」のEPSをこれまで幾度も市場に投入してきた。システムがコンパクトになれば、車体のレイアウト設計の自由度も向上する。高いアシスト力とコンパクトさを併せ持つシステム――。それが、NSKのコラムEPSが世界で受け入れられているひとつの要因といえるだろう。
さらなる成長の切り札、
新市場への参入
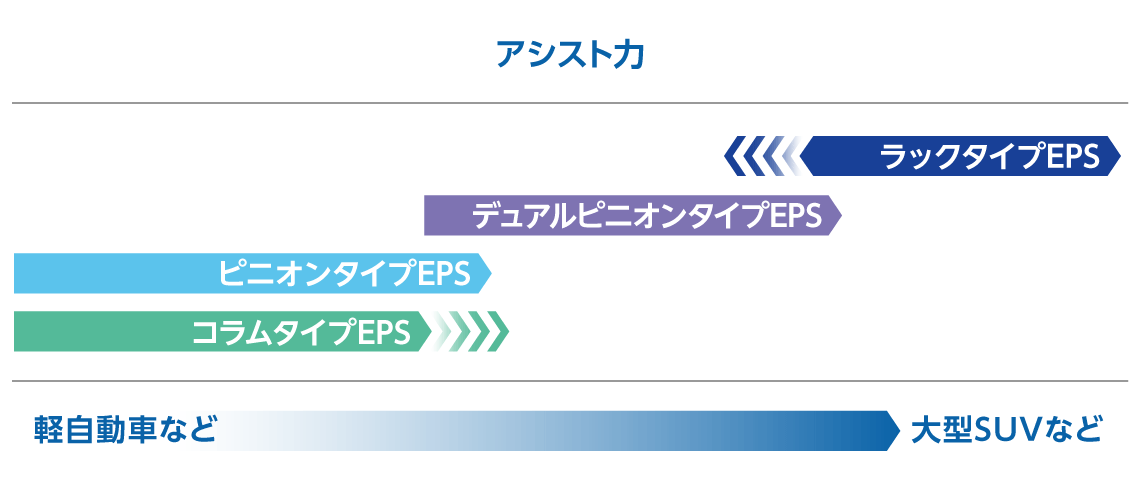
コラムEPSという確たる柱を持つNSKだが、市場の変化の波をとらえ、今後はラックEPSへの参入を視野に入れている。
ラックEPSとピニオンEPSは、どちらもラック&ピニオンの動きをアシストするものだが、よりタイヤに近い下流のラックタイプの方が、高い出力を得やすく、中~大型車向けのEPSとして、市場の拡大が見込まれている。これまで中~大型車には、高出力と操舵性能を得やすい油圧式パワーステアリング(HPS)が使われることが多かったが、環境性能へのニーズの高まりと、EPSの技術の進展により、ラックタイプ搭載車が増えているためだ。
一方のピニオンタイプは、コラムタイプとラックタイプの中間に位置づけられるが、コスト面ではコラムタイプに、出力面ではラックタイプに見劣りする。現在のEPS市場において最も採用数が少ないうえに、今後も搭載車の販売は減少していくと見られている。
NSKがラックEPSへの参入を決めた背景には、市場の伸びが見込まれることに加え、核となる要素部品を自社で内製・調達できることが理由として挙げられる。
ラックをアシストする機構には、「ボールねじ」という機械部品が使われるのが一般的だ。2016年現在、NSKはラックEPSのシステムの納入実績こそまだないが、「ボールねじ」は軸受メーカーとしてNSKが長年手掛け続け、世界一のシェアを誇る製品だ(NSK調べ)。この核となる要素技術を活かし、自社でラックEPSを製造するための準備も進めている。コラムタイプとラックタイプの二本柱で、完成車メーカーの要望にフルレンジで応えていく戦略だ。
なぜ、軸受メーカーのステアリングシステムが
世界で受け入れられるのか
ここであらためて、NSKのEPSがなぜ世界で受け入れられているかを考えてみたい。
NSKは、1916年に軸受メーカーとしてスタートした企業である。コラムEPSの市場拡大の波をうまくとらえたのは確かとはいえ、それだけが理由で、世界のEPS市場でトップクラスのシェアを占められるものだろうか。
その謎に迫るカギは、まさにNSKが軸受メーカーとしてスタートしたことにありそうだ。同社のステアリング開発部門で、ユニット部品の開発を担当する黒川祥史氏は次のように語る。
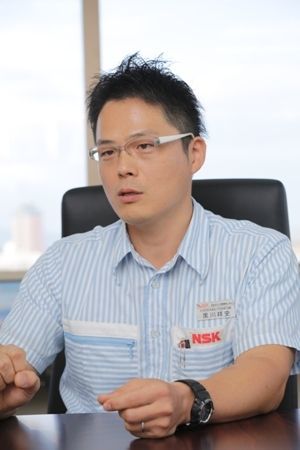
ステアリング技術センター
ステアリングR&Dセンター
ユニット開発部 副主務
黒川祥史
「ステアリングは、運転者が直接手で触り、フィーリングを確かめながら操作する、自動車のなかでも特殊なシステムです。運転者の意図通りにクルマを動かすには、ソフトウェアの制御だけでは難しく、機械部品の性能が物を言います。というのも、ステアリングはトルクや回転を伝える部品を統合したシステムです。部品どうしの接合部には当然ながら荷重がかかり摩擦が発生する。それを適切に制御することが、ステアリングをシステムとして成立させる重要なポイントです。荷重や摩擦の制御は、当社が軸受メーカーとして長年培ってきた技術のひとつです。その技術をステアリングに応用できることが、当社の最大の強みと考えています」
軸受は、機械部品どうしを接合し、回転や往復運動を支える基幹部品だ。軸受に求められるのは、摩擦によるエネルギーロスや発熱を減少させ、部品の焼き付きを防ぐこと。NSKは創業以来、機械の摩擦や摩耗を制御する「トライボロジー」と呼ばれる技術を磨き続けてきた。
軸受の性能や信頼性は、機械全体の性能や信頼性にも大きな影響を与える。そのため、軸受を構成する「材料技術」やコンピュータ・シミュレーションによる性能の「解析技術」においても、NSKは極めて高い水準を追求してきた。さらには、機械(メカ)の高い機能と性能をエレクトロニクスの力で引き出す「メカトロ技術」の研究開発にも力を注ぐ。NSKが誇るこれら「4つのコアテクノロジー」が、EPSの開発を根底で支えているのだ。
もうひとつのポイントは、ステアリングやEPSの開発に取り組んできた歴史の長さだ。ステアリングシステムのコスト設計を担当する小磯貴之氏は、その間の技術の蓄積の重要性を指摘する。
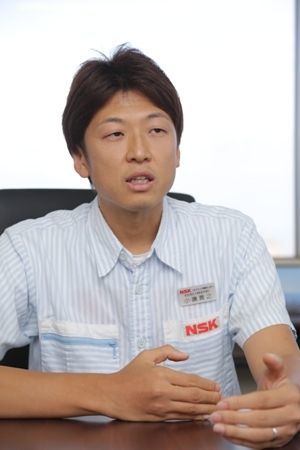
ステアリング技術センター
ステアリングR&Dセンター
設計原価企画室 副主務
小磯貴之
「当社がステアリング事業を手掛けるようになったのは1950年代、半世紀以上も前のことです。EPSの分野では、1986年にフォークリフトで電動モーターによるアシスト技術を業界に先駆けて実現し、自動車への採用という意味ではタッチの差で2番手になったものの、すでに30年近くEPSの開発に取り組んでいます。機械部品メーカーとしての土台に、ステアリングとEPS開発の歴史が積み重なり、それが世界で認められる強みになっていると感じます」
「4つのコアテクノロジー」の土台の上に、ステアリングやEPS固有のさまざまな技術が蓄積され、フィーリングのいいステアリングシステムに結実していると言えるだろう。
ステアリングシステムの制御ソフトウェアを開発する大場正也氏は、こうも指摘する。
「当社は、完成車メーカーの系列に属さない独立系メーカーです。系列企業の意向に縛られることなく、顧客の要望に柔軟に対応し、あるいは自社から積極的にアイデアを顧客に提案することができます。そうした柔軟性や提案力が、世界に認めていただけるひとつの要因になっていると思います」
揺るぎない技術と自由で柔軟な発想、そして独立独歩の精神が、軸受メーカーを世界有数のステアリングメーカーへと昇華させたというわけだ。
クルマの未来を切り拓く、
部品メーカーの底力
今、自動車業界は激変期を迎えている。自動運転や電気自動車が広まることで、クルマの形や動作メカニズムだけでなく、業界構造までもが大きく変わる可能性さえある。そうした状況で、ステアリングメーカーの現場のエンジニアが、未来の「曲がる」や未来のクルマをどう捉えているか、率直な意見を尋ねてみた。
大場氏は、ソフトウェア開発の観点から、「ソフトウェアにできることと同時に責任も増えていく」と展望する。
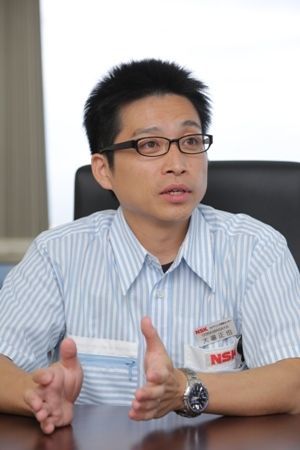
ステアリング技術センター
ステアリングR&Dセンター
次世代コラムEPS開発部 副主務
大場正也
「ステアリングは重要保安部品で、緊急時でも“曲がる”機能を保ち続けなければなりません。自動運転システムに不具合が発生した場合や、人間の運転介入をどのように受け入れるかなど、ソフトウェアで処理しなければならないことが多くなります。もうひとつの大きな流れは、クルマそのものがインターネットにつながるデバイス、いわゆる“コネクテッドカー”になることです。スマートフォンと同じように、インターネット経由で、クルマを動かすソフトウェアのバージョンアップや機能追加がされるようになってきています。利便性と同時に、インターネットにつながっているがゆえのセキュリティ対策への対応も急務となっています。ソフトウェアの重要性が高まるだけに、ソフトウェアメーカーが業界を牛耳る構造に激変する可能性も十分にありえます。そういう状況で、クルマの“曲がる”を実現するメーカーとして何ができるか、何をすべきかを日々考えています」
続いて小磯氏が次のように語る。
「今の状況を見ると、ステアリング単体で“曲がる”を考えられなくなっています。そういう状況だからこそ、クルマの“常識”をいったん脇に置いて、あらゆる可能性を検討しています。ロボットカーのような無人運転(自動走行)が可能になると、そもそもハンドルが要らなくなるはずです。そのときにどうやって“曲がる”を実現するのか――。あるいは、運転席に人が座ることを前提にした自動運転でも、今あるステアリングシステムがそのまま使われるとは限りません。操舵のための入力デバイスが、ハンドルではなくスティックやスマホの画面になるかもしれません。既成概念を脱ぎ捨て、クルマの未来をどうつくっていくか――。そこに挑んでいけることに大きなやりがいを感じています」
黒川氏も、現状を好機と捉え、クルマの未来を力強く見据える。
「クルマは目的地まで移動する手段です。ひとりの運転者として、自動運転が広まることは、クルマの可能性を広げるものとして歓迎したい。そのときにクルマの“曲がる”がどうなるか――。さまざまな可能性がありえますが、“曲がる”ためにタイヤの角度を切るという方法はきっと残るはずです。当社にはそのための要素技術があり、独立系メーカーという立場からも、完成車メーカーに対して自由に提案を持ち掛けることができます。勝負どころは、市場に受け入れられる新しいクルマや“曲がる”仕組みを、他社に先んじて市場に投入できるかどうかです。今は、クルマの未来を自分の手で切り拓いていける、非常に面白い時期だと思っています」
クルマの「あたらしい動き」をつくる
エンジニア求む
NSKでは、クルマの未来をつくる技術と意欲を持ったエンジニアを募集中だ。実は、本記事に登場する3氏はみな転職組だ。働く場所としてのNSKの魅力や、求める人材像について尋ねてみた。
小磯氏は、NSKは幅広い仕事に取り組むチャンスが得やすいと、職場としての魅力を語る。
「私は製品のコスト設計部門と次世代EPSの開発部門の2つの組織に所属し、異なる立場と視点から、EPSの開発に取り組んでいます。部署の枠を超えた業務でも、自分から手を挙げた社員には積極的に任せてくれるオープンなカルチャーのおかげです。兼務による苦労もありますが、複数の業務に取り組むことでキャリアの幅も広がり、自分でも成長を実感しています。また、前職ではマニュアルステアリングのメカ設計を担当していた私が、メカとエレクトロニクスが融合したEPSの開発に携わり、今では技術の幅も広がっています。さらにNSK が国内だけでなく、グローバル化を進めていることも大きな魅力の一つです。そのため海外の完成車メーカーとの取り引きがあり、生きたビジネス英語を実践を通じて学べる環境もあります。エンジニアとしての幅を広げたい人には間違いなくぴったりの環境です」
黒川氏も、社員に任される裁量の大きさを魅力として触れた。
「入社してまもなく、パワーアシスト機構のないステアリングシステムを、コラムタイプのEPSに置き換える業務を担当しました。そのなかで、要素部品のひとつであるインターミディエイトシャフトの設計を担当し、私が提案したアイデアが製品に採用されました。その過程で、完成車メーカーの設計統括者の信頼も得られ、大きなやり甲斐を感じました。このように、商品開発の方向性や開発プロセスにおいても、社員からの提案を受け入れてくれるオープンな土壌があります。自分の技術とアイデアを活かしたい、積極的な人にはもってこいの職場だと思います」
大場氏はソフトウェア開発の観点から、求める人材像を次のように語った。
「自動車技術は大きな変革期にあり、ソフトウェアに求められることがますます大きくなっています。プログラムの規模ももちろん大きくなり、従来の開発スタイルを変えていく必要性にも直面しています。つまり、ソフトウェア開発はこれまでにない新たな局面にあり、いま取り組んでいることが、これからのソフトウェア開発の標準を担う可能性が十分にあります。世の中の自動車を取り巻く流れにも好奇心を持ち、次の時代を自分の手で切り拓くという強い気概を持った人に、ぜひ来てほしいですね」
クルマの未来を見据え、NSKは既に、「曲がる」だけでなく「走る」と「止まる」の要素技術を手がけている。車輪に直接とりつける「ホイールハブモーター(一般にはインホイールモーター)」と、電気自動車の回生ブレーキに使われる「ボールねじ」だ。ボールねじを使ってNSK独自のブレーキシステムを開発する計画があることもすでに発表済みだ。
軸受メーカーとしてスタートしたNSKは、今やステアリングメーカーとして50年を超す歴史を歩み、自動車技術の総合メーカーへの脱皮を試みている。市場が激変する環境を好機と捉え、攻めの一手に出ているのは、系列に縛られない独立系メーカーであることと無縁ではないだろう。
クルマの未来をつくる――。NSKにはそのための要素技術があり、そのためのマインドと環境が、現場に息づいている。時代を動かすチャレンジングなものづくりの舞台が、ここにはある。