「製缶工場IoT」実現したネットワーク変革の道筋 「高速生産」のデータ化をかなえた方法とは
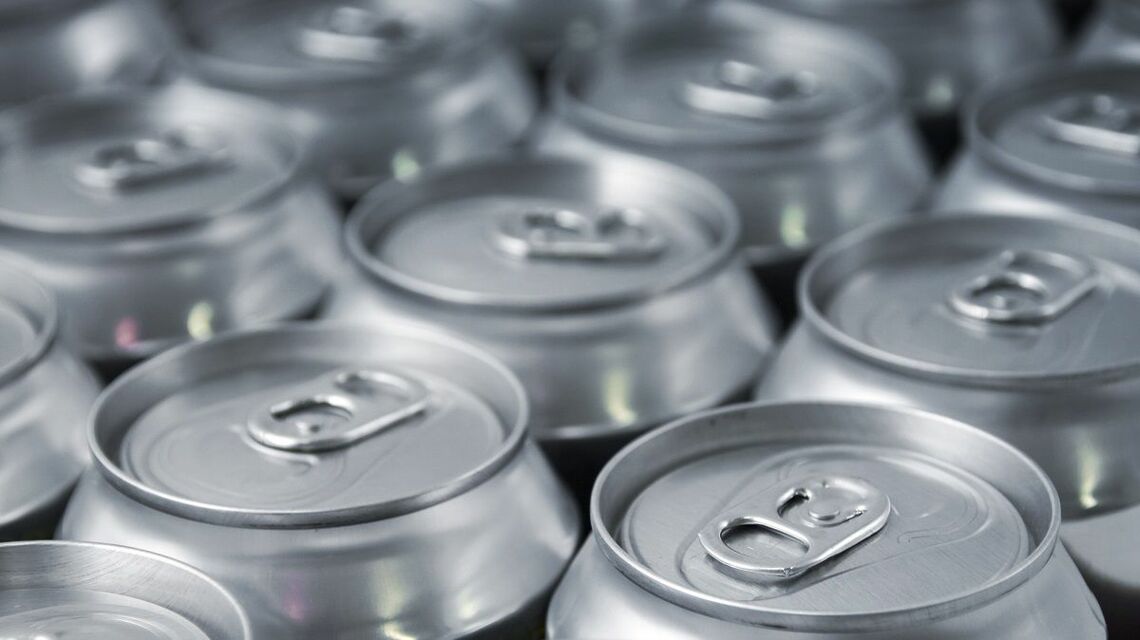
「近い将来、新しいことに取り組めなくなる」
1917年の設立以来、100年以上にわたり缶やペットボトル、プラスチック、パウチなどさまざまな包装容器を手がける東洋製罐グループ。2025年度を最終年度とした中期経営計画では、「『くらしのプラットフォーム』へ向けた持続的な成長」を基本方針に掲げ、その成長を支える経営基盤を強化する手段の1つとしてDXを推進している。
中でも重視するのが、製造現場である工場のIoT導入とデータ活用だ。東洋製罐グループホールディングス IoT・ロボット推進室 ジェネラルマネージャーの菊地隆之氏は、次のように語る。
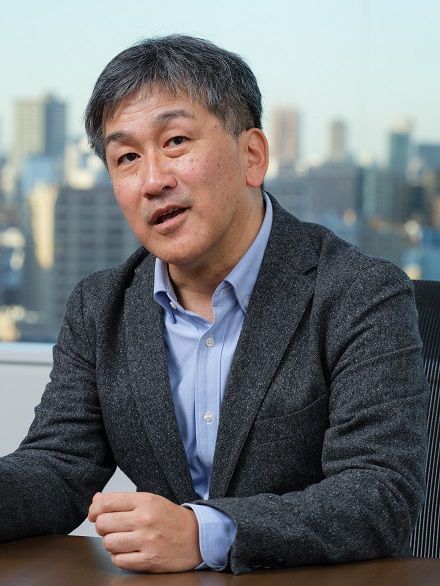
IoT・ロボット推進室
ジェネラルマネージャー
菊地 隆之氏
「容器は、中身の使用が終わると資源に変わるという特性があり、バリューチェーン全体をデジタルで管理することが求められます。製造現場のデジタル化による生産効率の最適化と、そのデータを在庫や営業などの社内データと統合することによる改善サイクルの構築が、情報システムに求められる姿だと考えています」
その第一歩として同社が取り組んだのが、製造関連のデータ活用の高度化を見据えたIT基盤の構築だ。
「製造現場のデータ活用自体はこれまでも進めてきましたが、各所で部分最適を積み上げてきたために、データがバラバラに管理され必要なときに見つからなかったり、ノウハウが個人にひも付いて引き継ぎが難しい状態になっていました。このままでは近い将来、作業に追われて新しいことにも取り組めなくなるという危機感がありました。
そこで、製造現場のあらゆるデータやノウハウを集中的に一元管理して活用可能にすることで生産効率を高め、担当者が変わっても安定した製造を維持できるようにしようと考えました。そうして開発したのが『SaTeras』です」(菊地氏)
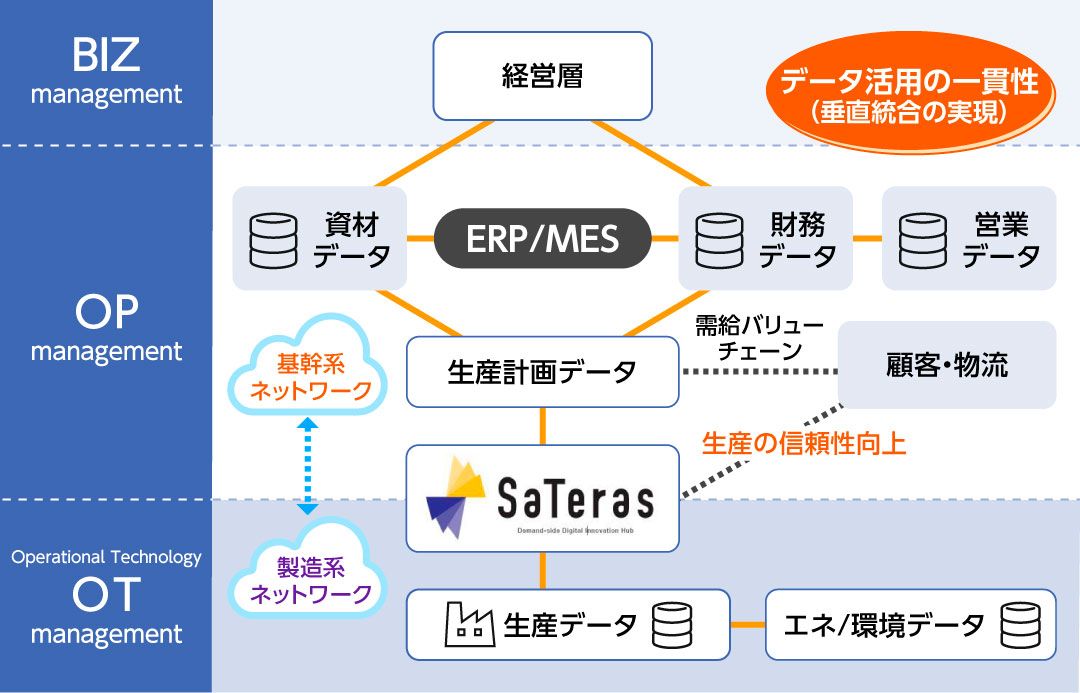
「1分間に2000缶」に対応するネットワークをどう実現?
SaTerasは、製造関連データをシンプルに統合し、現場や管理部門、さらに経営層が活用していくためのシステムだ。工場にIoTを導入し製造関連のデータを一元化することで、リアルタイムに生産状況を可視化し、遠隔監視によって管理負担を低減。AIによる分析で、工程の不具合発生の予測も行えるようになる。
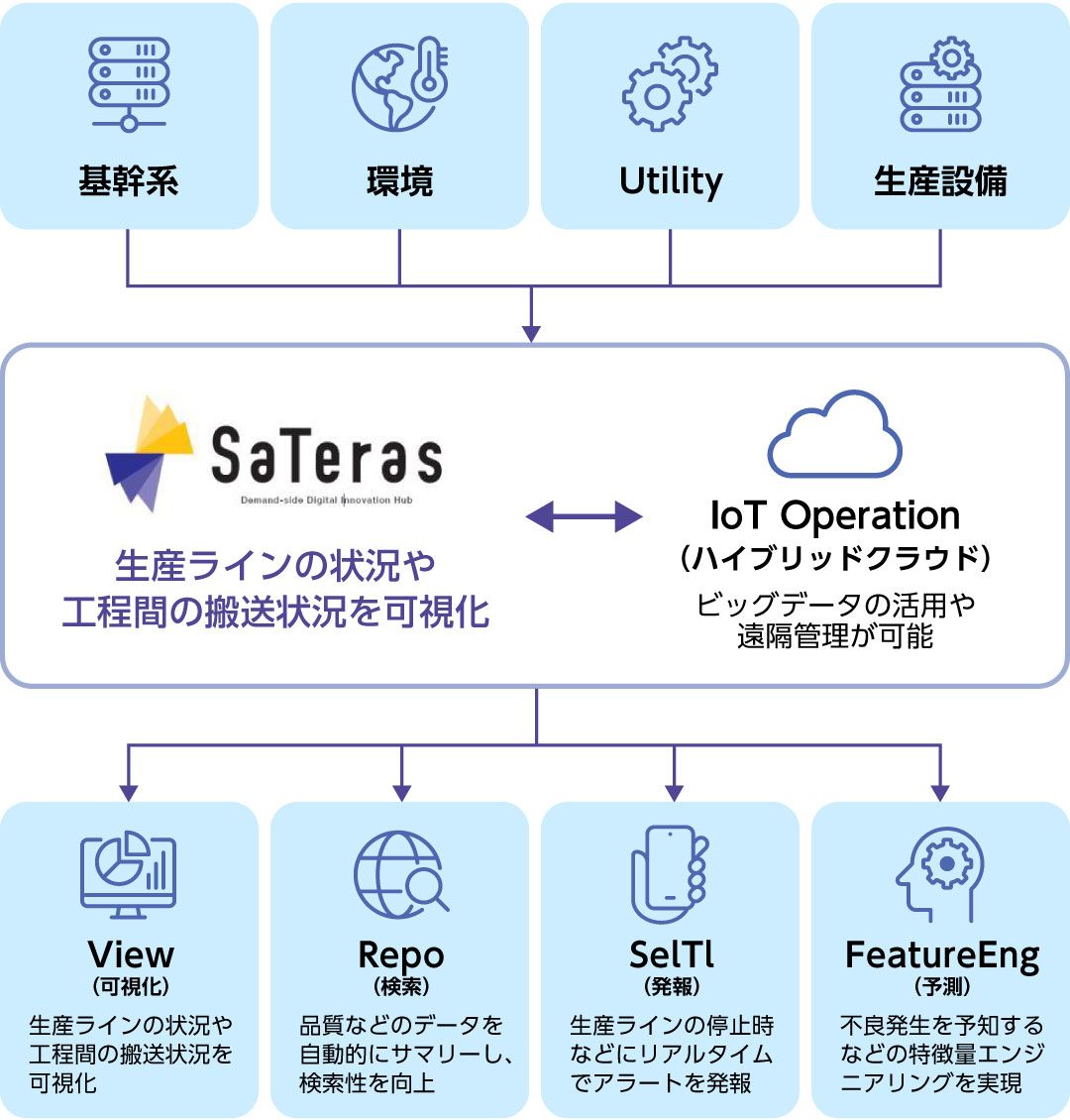
しかし、製造現場のデータをIP(インターネットプロトコル)として統合するシステムは、簡単には導入できなかった。東洋製罐グループの要求に応えるシステムは、製造現場向けのソリューションを提供するベンダーの製品の中には見当たらなかったのだ。
その理由は、製造ラインの特徴にある。「製缶に用いる製造ラインの全長直線距離は約800メートルあり、速度は最も速いところで、1分間に約2000個の缶が流れます。この高速・大量な製造ラインのデータ化にリアルタイムに対応できるものが見つからず、内製化が必要でした」(菊地氏)。
工場のラインには、高度な制御を施した生産設備と生産技術者が配置されているが、省人・省力化の傾向に伴い、兼務作業が増えつつあるという。また、工場内の各工程情報のトラブルなどの伝達事項の共有は、人による紙ベースまたは実製品ベースによって日々行われている。今後、生産技術者の育成、人材確保がさらに難しくなる現場では、労働環境をよりよくすることも重要だった。
こうした現場の課題を解決するためにSaTerasの開発に着手する。それに当たって菊地氏は、SaTerasの心臓部である製造現場から情報を集めるセンサーネットワークに、無線LANの技術を使うことに決めていた。
工場内に無線LAN環境を整備できれば、作業員が工場内で持ち歩くウェアラブルデバイスに直接通知やメッセージを送ることができるため、異常が起きてアラートが発報された際も素早い対応が可能になる。それによって作業員の負担は大きく減るとともに、対応が早くなることで結果的にラインへの影響も抑えられるからだ。
しかし一般的に、工場のラインではノイズの影響や機械が動くことによる電波の安定性などを考慮すると、無線LANのシステムは対応させるのが難しいというのが定説だった。しかし菊地氏は、それを乗り越えられると考えたという。
「これまで無線技術に携わってきた経験から、工場内に影響を与えるノイズと無線LANの帯域は、そもそも周波数が異なるため、それを考慮して設計すれば影響は少ないと考えていました。ただその検証ができていなかっただけで、実際にトライしてみれば十分に無線LANでいけるだろうという確信があったのです」(菊地氏)
「国内専業メーカー」の技術力やサポートを評価
これまで困難と思われてきた工場の無線LAN化に際して、東洋製罐グループがネットワーク構築のパートナーに選んだのが、日本発のネットワーク機器専業メーカーであるアライドテレシスだった。同社とはかねてオフィス内のネットワークで取引があったが、改めて相談する中で「製造現場を丁寧に視察して、業務への深い理解の下に実現可能なプランを提案してもらえたことが、採用の決め手になりました」と菊地氏は言う。
同社の工場IoTは、無線LAN化を前提に設計が進められた。今回の開発は、アライドテレシスにとっても新たな挑戦が多かったという。同社でプロジェクトを指揮した、アライドテレシス執行役員の小泉卓也氏は次のように語る。
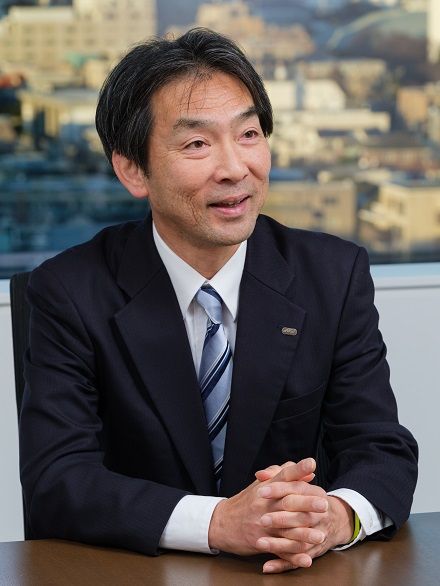
執行役員
東京営業本部長
小泉 卓也氏
「当社が主に手がけるオフィスのネットワークとは異なり、工場現場では、さまざまなメーカーの機器が複雑に組み合わさり、個々の機器が独自のフォーマットでデータを吐き出しています。そのため、現場で実際に使われている機器を確認し、当社でも同じものを手に入れて、それらがどんなパケットを出すのかを調べることから始めました」
開発を進めるにつれ、次々と課題が出てきた。例えば工場には鉄製の機器が多数あるため、電波を乱反射する。安定して電波を送受信するには、アクセスポイントをどのように配置すればいいのか。また、高速で製品が流れているラインでは、1つの缶について約30ミリ秒という短い時間でセンサーデータを取得している。一見正しくデータが取れているように見えても、詳しくチェックすると取りこぼしがあったり、不要なトラフィックが混在したりしていた。
そうした問題を細かな調整によって、一つひとつ解消していった。現場にアライドテレシスのエンジニアや小泉氏もたびたび赴き、「ああでもないこうでもないと会話できたのがよかった」と菊地氏。小泉氏も「拠点に根付く国内メーカーとして、一緒に構築していくというのが当社のスタイルです」と応じる。
こうしたチューニングには長い時間を要したが、2年ほどで最初のパイロット工場で無事に無線LAN環境によるIoT化を実現した。工場が違えばラインで使われている機器も異なり、建屋の環境も異なる。都度チューニングの作業は必要だが、横展開を進めるにつれ時間の短縮が進み、現在では数カ月で導入できるようになった。
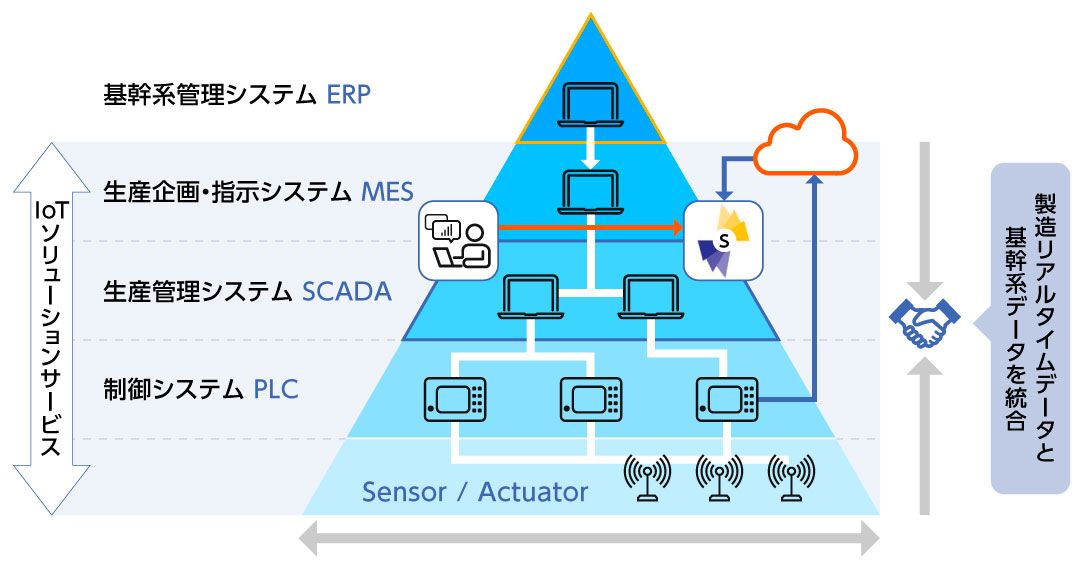
工場IoTの仕組みを国内外に横展開へ
現在、東洋製罐グループの国内製缶工場へのSaTerasの導入が決まり、段階を経て横展開を行っている。初期導入工場からは、「少ない人数でもライン全体の状況が把握できるようになった」「ベテランだけでなく若手でも適正な対処ができるようになった」といった声が聞かれるように。
「SaTerasには製造ラインの情報をグラフィカルに表現する機能があります。現場の可視化によって工場全体の動きが見えることで社員のモチベーションが上がって、現場自ら作り上げていく思考に変わりつつあり、雰囲気も明るくなったと感じました」と菊地氏は手応えを語る。
同社では、SaTerasの導入で工場の「匠」のノウハウを可視化し、品質向上に役立てようとしている。それだけでなく、これまでの経験と勘に頼っていた作り方が、本当に成果を出しているかの検討も進めている。
「経験則に基づいた調整が本当に正しいのか、IoTのデータを見れば検証できます。社内には『都市伝説から探しにいけ』と伝えているところです」(菊地氏)
製造業のIoT化によって国内工場で培った現場の匠の技をデジタルで標準化し、それを海外工場に取り入れれば、生産の安定化と精度が飛躍的に高まるとみる。また、その先には、社内の実績をもって、SaTerasをソリューションとして展開することも視野に入れる。
「当社の工場は、おおむね高速生産が1つの特徴です。その流れを止めないことはIoT化の本当にシビアな課題でした。その解決には、アライドテレシスというネットワークの専門家の力が不可欠で、大きなサポートをいただきました。これからもともに、現場から学んでいきたいと思います」(菊地氏)
先端のデジタル技術やデータ活用を通して従来のものづくりを変革し、顧客や社会に新たな価値を届けようとする東洋製罐グループ。その中核といえるインフラ基盤をアライドテレシスのネットワーク技術が支えている。
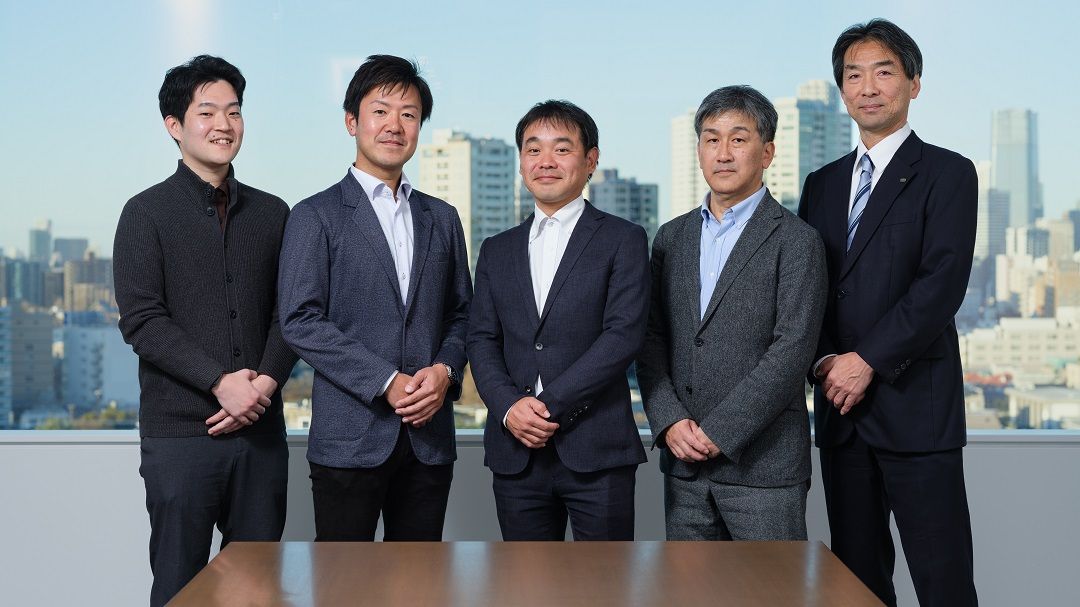