半導体製造を支える「見る・測る・分析する」技術 日立ハイテクの半導体製造ソリューション
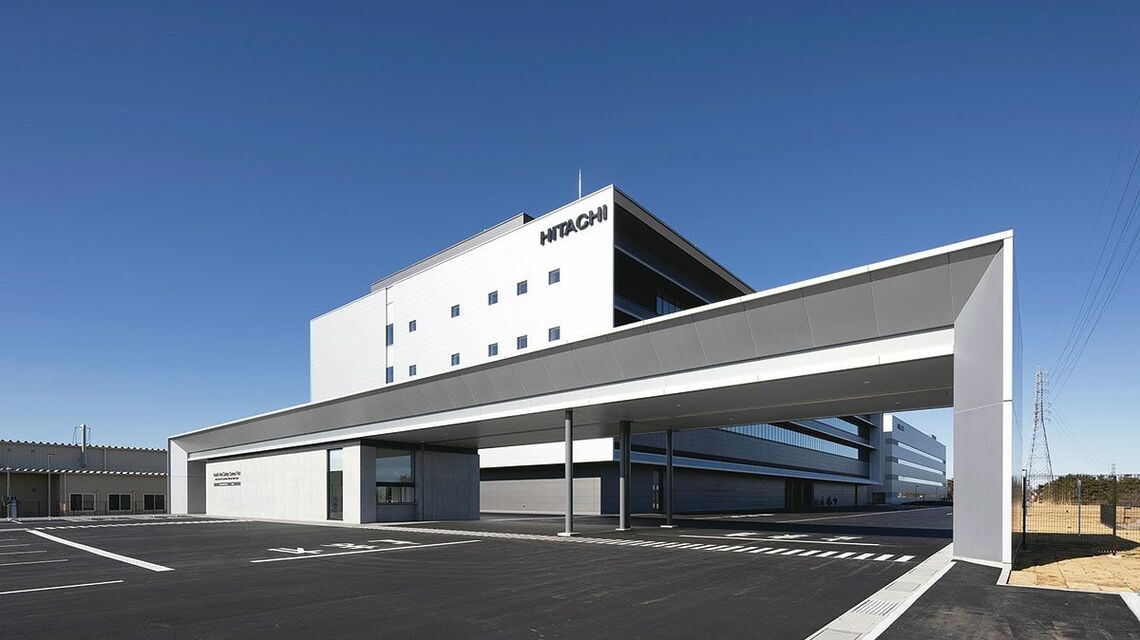
高性能な半導体の開発・量産を実現する
「見る・測る・分析する」力とは?
半導体は「産業の米」といわれる。そのゆえんは、スマートフォンやパソコンのみならず、エアコンや洗濯機など暮らしを支えるあらゆる製品やサービス、インフラに組み込まれ、直接的にも間接的にもわれわれの生活を支えていることにある。
それだけではない。AIの進化、自動運転、ビッグデータを用いた高度な分析、電気自動車の実用化など、従来なら不可能にも思えた高度なデジタル技術の活用により、持続可能な社会の実現が進んでいる。それには高性能な半導体が不可欠となる。
「生活に溶け込む半導体は、地政学上の戦略物資として位置づけられるほど重要性が増しています。実際、2023年は調整期となりますが、年平均成長率(20~27年)は9%程度で拡大し続けると予測されています※。今後も需要が増大するだけでなく、半導体の用途は多様化・高度化し、高性能化や開発期間の短縮が求められています」とナノテクノロジーソリューション事業戦略本部事業戦略部の堀田尚二氏は語る。
最先端の半導体へのニーズは量的にも質的にも高まり続けているが、その供給には3つの課題がある。開発期間の短縮、量産立ち上げ段階における良品率の早期向上、量産段階における装置の高稼働率の維持だ。
日立ハイテクはこの3つの課題を解決すべく、同社の「見る・測る・分析する」技術を活用した半導体製造ソリューションの開発を推進している。具体的には、製造過程で生じる不具合を発見する検査装置、設計どおりの微細加工ができているかを計測する測長装置、欠陥や不具合を分析して原因を究明する解析装置、微細加工を実現するエッチング装置をラインナップし、さらにこれら装置が生成するデータを統合し活用することで高度化する半導体製造の要求に応えていく。
とくにプラスマイナス0.1ナノメートルレベルの寸法誤差も計測できる「測長SEM(CD-SEM)」は、世界市場でシェア約7割を維持し続けている※。
「半導体業界において製造装置から検査装置、計測装置、解析装置まで幅広い領域にわたりラインナップを持っているメーカーは珍しいと思います」と評価システム営業本部評価企画部の水野貴之氏は語る。これらの技術を一貫したソリューションとして提供することで、最先端の半導体開発から量産に至るまでを支えている。
「10億分の1メートル」精度の製造装置もラインナップ
では日立ハイテクが高度な技術を幅広い領域で連携させ、ソリューションとして提供できるのはなぜか。背景にはその成り立ちがある。同社は日立製作所グループの中で脈々と受け継がれてきた電子線技術を持つ計測器グループや、エッチング装置を持つ半導体製造装置グループが事業統合して成長してきた。「半導体製造の課題が高度化する中で、それに対応するために、検査計測装置事業と製造装置事業の連携が強まっていった」(堀田氏)という。
半導体の製造工程は、大きく3つに分けられる。回路の設計、設計した回路をシリコンウェハの表面に作る前工程、そして半導体チップを切り出して製品に使用できる状態に組み立てる後工程だ。
さらに前工程は成膜、パターン転写、そしてエッチングなどの工程に分かれている。
中でも「エッチング」はウェハ上の薄膜に転写された回路パターンに沿って膜を削り、実際の配線形状に加工する、半導体製造の肝ともなる工程だ。とくにハイエンドの半導体を作るときは、ナノ単位の精度が要求され、わずかな不具合や誤差も許されない。
日立ハイテクでは、このエッチング工程においてナノメートル、すなわち10億分の1メートル以下の精度が要求される半導体製造工程の微細化にも貢献している。
同社がラインナップする製造装置の中でも「電子サイクロトロン共鳴(ECR)」を使ったエッチング装置は日立独自のものだ※。プラズマ化したガスを用いて「膜」を削る技術により、膜を傷つけるリスクを最小限に抑え、品質や歩留まりの向上を実現しながら最先端の微細な半導体の製造に貢献している。
半導体製造工程の「脱炭素化」で
持続可能な社会の実現に貢献
今後は引き続き「見る・測る・分析する」技術に磨きをかけるとともに、サステナビリティの観点を重視していくという同社。
「半導体市場はどんどん大きくなっているので、いろいろな事業機会が生まれています。われわれは自社の強みを生かし、お客様の困り事にお応えして事業の幅を広げ、事業を成長させていきたい。同時にSDGsを踏まえ、社会課題の解決を意識して事業を展開しています。例えば、省エネに貢献するパワー半導体をはじめ、われわれが供給する装置やソリューションで作られた半導体は、電気自動車、再生可能エネルギー供給、DXの中核となるデータセンターなどに使われています」(堀田氏)
また、日立ハイテクでは装置の設計、開発、製造から利用に至るすべての段階でのCO2削減を図ることでサプライチェーン全体の脱炭素化に貢献していく。すでに、21年3月には半導体製造装置の新たな開発・製造拠点として「マリンサイト」(茨城県ひたちなか市)が竣工。太陽光発電をはじめとする再生可能エネルギーの活用などにより、操業当時からカーボンニュートラルを実現。27年までに全事業所のカーボンニュートラルを目指す。
利便性とサステナビリティの両軸で重要性が増す半導体は、半導体事業の進化そのものが、環境負荷低減につながっていく。
その製造工程を進化させる日立ハイテクの「半導体製造ソリューション」も大きな役割を担っているといえよう。