JSRに見る、「半導体材料」で日本が躍進する訳 「フォトレジスト」でトップクラス維持の"鍵"
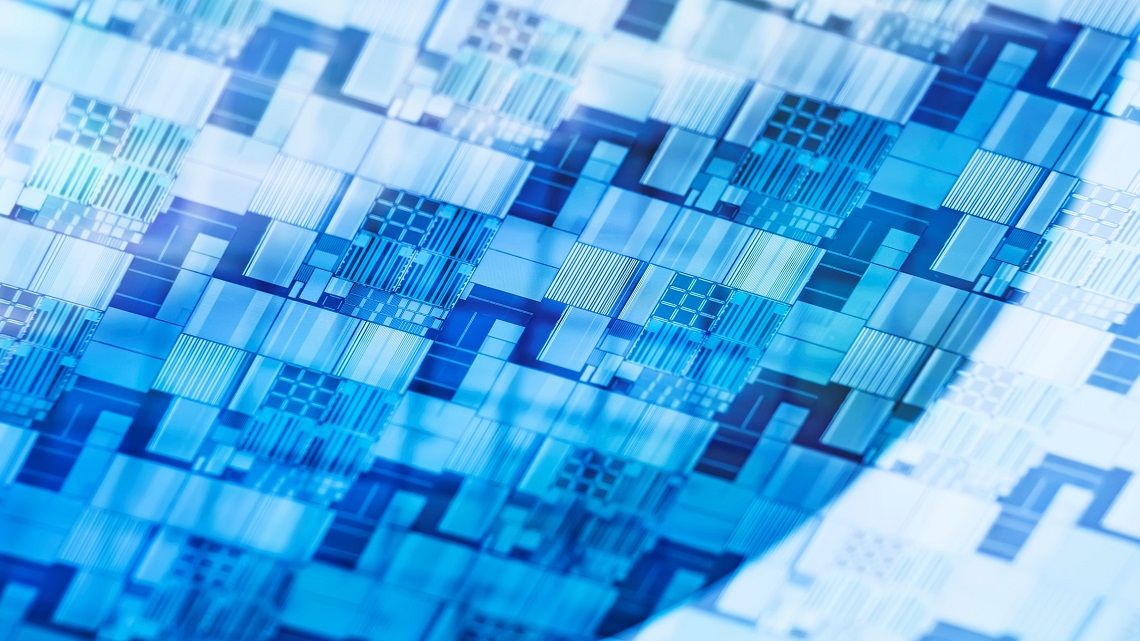
半導体の製造に欠かせない「フォトレジスト」
情報技術の発展は、人々の暮らしや社会をより便利に、豊かにしてきた。スマホを使いインターネット上で手軽に情報を収集・発信するのは今や「当たり前」に。最近は、情報処理技術のさらなる高度化・高速化によって、機械学習やディープラーニングといったAI技術が普及し、自動運転の実用化に向けた研究開発も進んでいる。これらが実現できるのは、半導体の存在とその進化があってこそだ。
半導体の進化は、つねに「微細化」によってもたらされてきた。半導体のチップ上に描かれる電子回路が微細化するほど、動作速度や電力効率が上がり高性能になる。JSRでフォトレジストなど半導体材料の研究開発を行う四日市研究センターのセンター長である島基之氏は、半導体の微細化には「フォトレジスト」の貢献が大きいと話す。
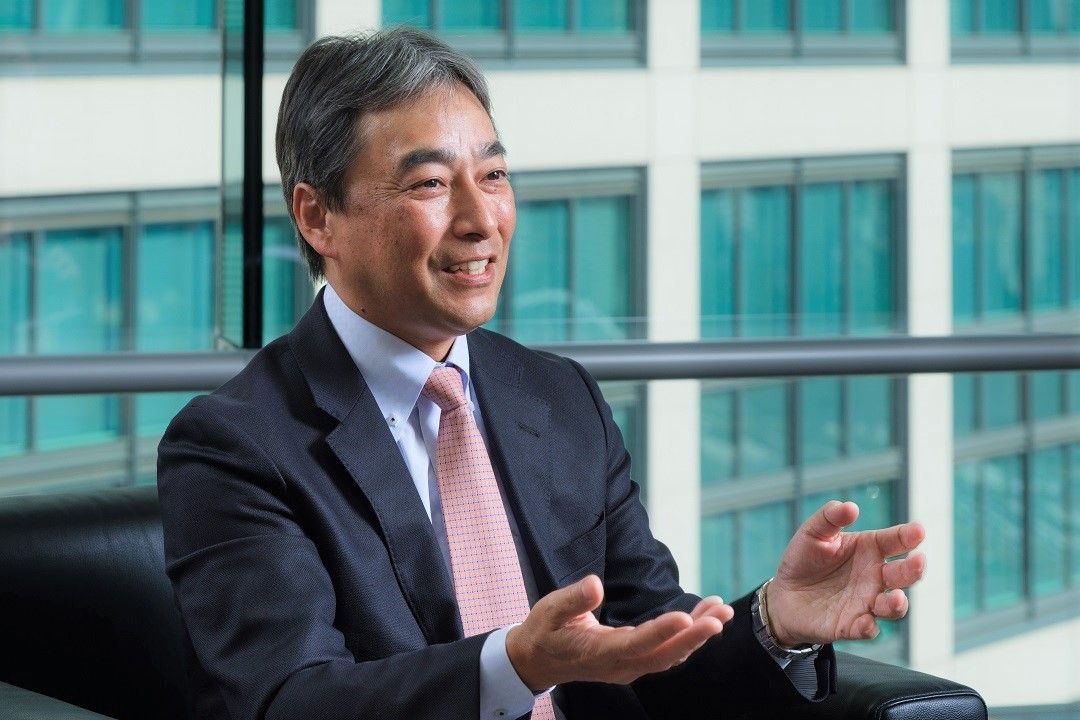
四日市研究センター長 精密電子研究所長 島 基之氏
「半導体の回路パターンは露光技術によって基板となるシリコンウェハーに転写されます。
このとき、シリコンウェハー上で光を受け止めるのが 『フォトレジスト』と呼ばれる感光性材料です。フォトレジストに微細な回路パターンが転写されて、この微細パターンをもとにシリコンウェハーが加工されていきます。つまり、露光技術とフォトレジストが両翼で進化することによって、初めて高集積な回路を形成することができるのです」
半導体の製造工程は、「前工程」と「後工程」の大きく2つに分けられる。シリコンウェハーの上に電子回路を加工形成し、半導体チップを作っていくのが前工程。ウェハー上に出来た数百のチップを一つひとつ切り出し、最終製品へと仕上げていくのが後工程だ。フォトレジストが使われるのは主に前工程である。
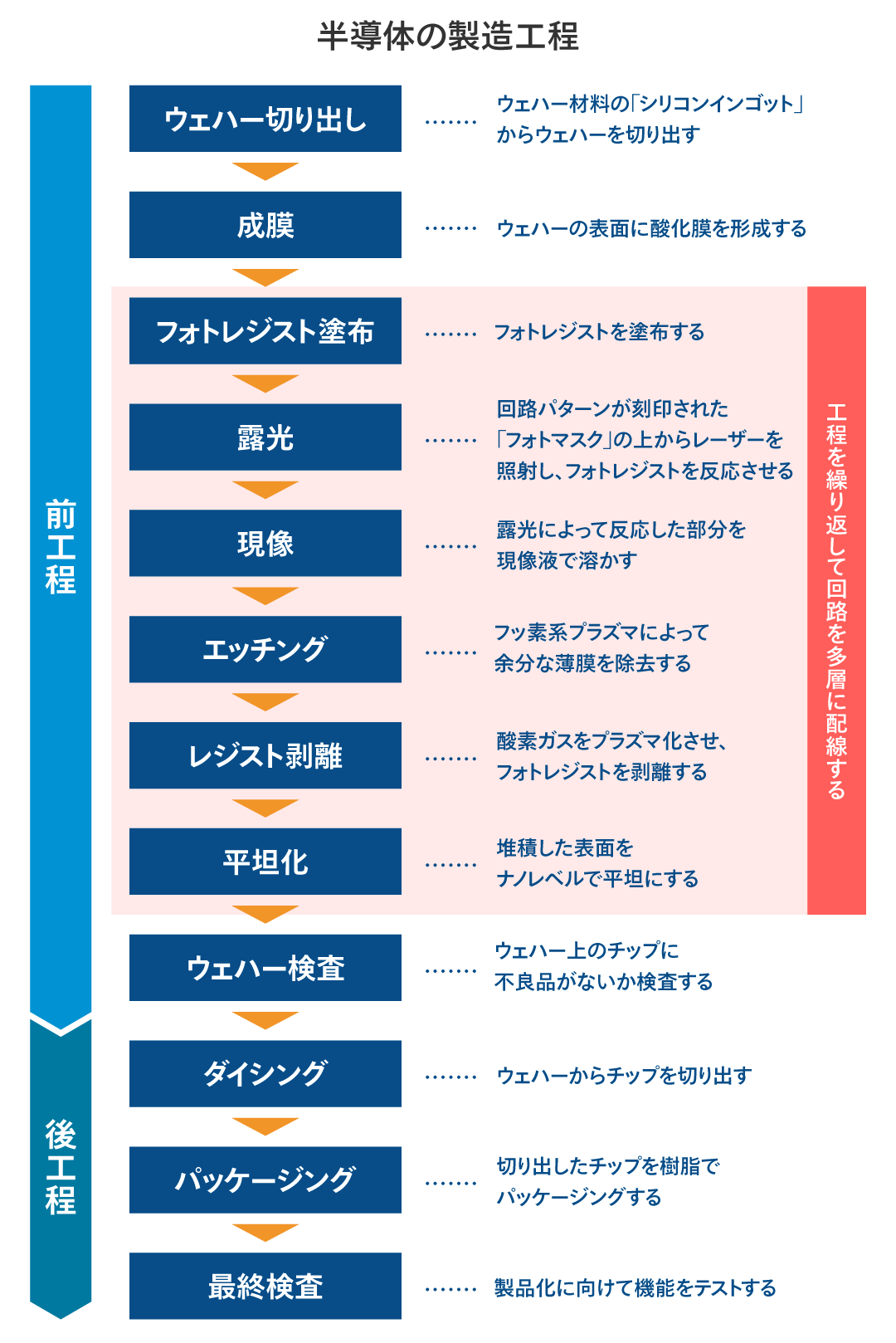
露光技術とフォトレジストの進化により微細化が進んだことで、半導体の性能はかつてとは比べものにならないほど向上してきた。
そして、進化はこの先も続く。「半導体には長期的な技術ロードマップが存在しており、これは詰まるところ微細化の計画です。当社は、このロードマップを見据えながらフォトレジストの開発を進めています」(島氏)。
トップクラスの実力の裏に「最先端」を追求する姿勢
半導体の製造工程に必須のフォトレジストは、日本企業5社で世界シェアの9割を占めるといわれている。
その中でもトップクラスにいるのがJSRだ。もともとは1957年に合成ゴム事業でスタートした同社だが、事業構造の変革に取り組み、優れた高分子技術を武器にフォトレジストを事業化し、40年超にわたり事業を発展させてきた。
なぜJSRはフォトレジストの分野において世界トップクラスでいられるのか。その理由として島氏が挙げるのが、継続的な技術開発で培ってきた「性能」と「品質」の高さだ。
「フォトレジストの技術開発ポイントは、新しい特性を求めて原料である感光剤や機能性ポリマーを設計、合成することと、その原料を組み合わせてお客様の要求に合致したフォトレジストを開発することの、2つの側面があります。これらはどちらも、一朝一夕にできるものではありません」
新しい原料の探索には、経験豊富な有機合成の技術者と最新の理論を駆使する計算科学エンジニアがタッグを組んで進めているという。無限に広がる新規化合物の海から効率的に最適な物質を探し当てていく。
もう一方の、工業製品としてのフォトレジストの品質は、JSRが誇る生産技術、管理技術の結晶だ。ナノメートルレベル(※ナノメートルは10億分の1メートル)の微細な回路パターンを描く材料ゆえに、フォトレジストの製造には不純物の混入を徹底的に防ぐクリーン化技術が必要となる。
そのクリーン度のイメージは、直径300ミリメートルのシリコンウェハーを野球場のサイズに拡大したときに「グラウンドの上に砂粒が10粒あってはいけない」(島氏)というレベルで、途方もないクリーンさが要求される。
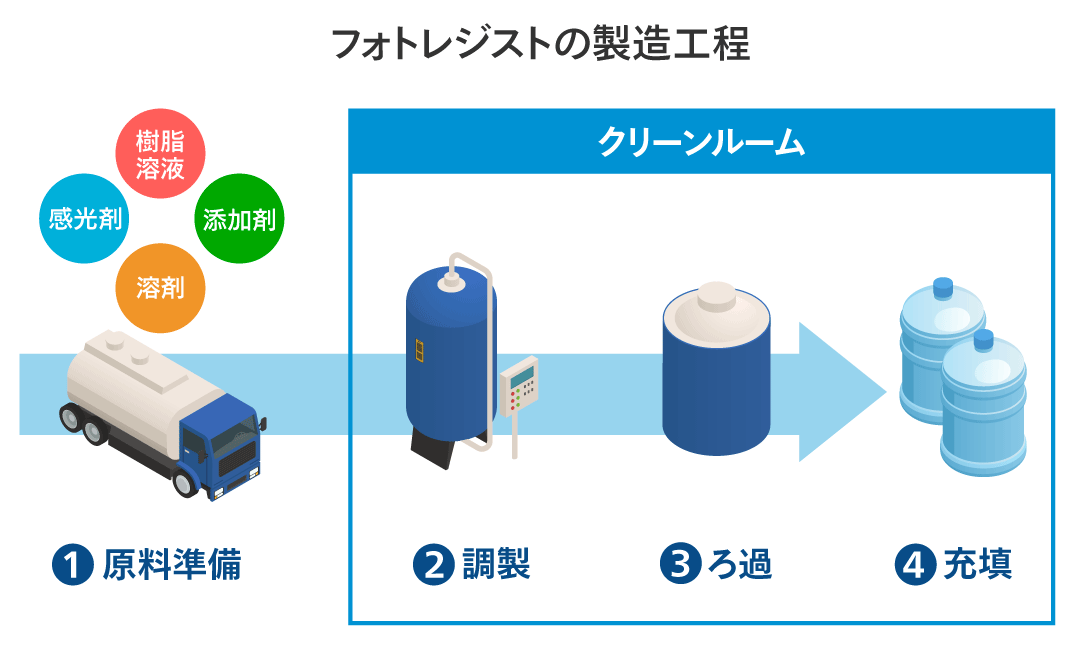
「現在、半導体製造の中心は海外に移っており、それぞれの国や地域でフォトレジストを作る新興メーカーも出てきていますが、この品質レベルを実現するのは容易ではないはず。私たちはこれからもクリーン化技術に磨きをかけていきます。追いつくのはかなり難しいでしょう」(島氏)
クリーン化技術のノウハウも、JSRが長年にわたって世界トップクラスであり続けられる理由のひとつだとうかがえる。それだけでなく、最先端を追求し技術開発を続けるには投資も必要になる。
フォトレジストの開発には半導体を製造するのと同じ装置が必要だが、先端半導体に用いられる露光装置の価格は1台数十から数百億円にも上る。「それでもお客様である半導体メーカーに安心して採用いただくためには、実機での検証は必要な投資だと考え、R&D(研究開発)にリソースをつぎ込んでいます」と島氏は語る。
外部の「新しい技術」も取り入れ進化を目指す
さらにJSRは、自前主義に偏ることなく、装置メーカーや半導体関連のコンソーシアムなど、外部との連携にも力を入れている。
そのひとつが、ベルギーの半導体研究機関であるimecとの共同研究だ。これまで、ArFフォトレジスト、液浸ArFフォトレジスト、液浸トップコート、EUVフォトレジストなどさまざまな材料の開発で成果を上げてきた。研究活動以外でも、2015年にEUVフォトレジストの製造に向けた合弁会社を設立し、先進的なフォトレジスト製造ラインとEUV露光機による量産・品質保証体制を提供している。
さらに最近の象徴的な例が、次世代EUVフォトレジストを開発するベンチャー企業である米Inpriaとの連携だ。JSRは21年に同社の全株式を取得し完全子会社化した。InpriaとJSRの技術を融合し、半導体のさらなる微細化に対応する態勢を整えようとしている。
「Inpriaは『メタルレジスト』と呼ばれる金属材料を用いたフォトレジスト技術で注目されています。EUV(極端紫外線)光を吸収する物質として金属が非常に有効なことはわかっていましたが、従来の常識では、金属の混入が半導体不良の原因となることから、金属不純物を極限まで取り除くことに心血を注いできました。そうしたわれわれにとって、金属を積極的に使うというのは新鮮な発想でした。
レジスト技術者としてフラットな気持ちでInpriaの技術を見ると、将来技術として大きな可能性を感じます。このようなイノベーティブな企業とJSRが組んで一緒にレジスト開発ができることはとても幸せなことです」(島氏)
過去の常識にとらわれず、新しい発想も受け入れて進化を模索する。そういうスタンスで技術と向き合うJSRの考えが表れたエピソードだ。
「イノベーションは『ゼロからイチを生み出すこと』といわれますが、私はそれだけではなく、『ある技術と何かほかの技術を組み合わせることで何十倍もすごい技術を生み出すこと』とも考えています。研究者は広い視野を持って、ユニークな組み合わせを探すことが大切です」と島氏は語る。
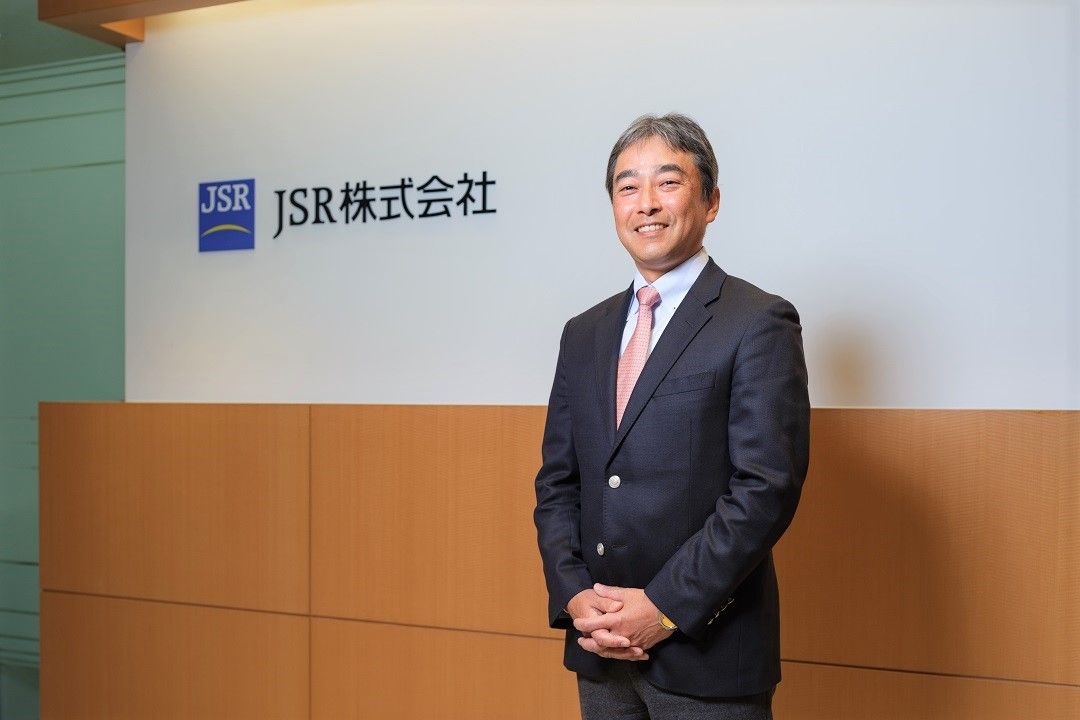
フォトレジストは、半導体の製造過程で使われた後、取り除かれて役割を終える。完成した半導体には残らないが、「半導体の進化を支えている自負を持って、研究活動を行っています」と島氏。
「半導体は今の社会に欠かせない存在です。当社は優れたフォトレジストを開発し、提供していくことで、これからも半導体の高性能化、ひいては社会の発展にも貢献していく考えです」と強調する。
年々性能が向上する情報端末や家電から、交通などの社会インフラまで、あらゆる場面で利便性を享受する私たちの生活の裏には、進化を続ける半導体と、それを支える日本企業の存在がある。