混乱する製造サプライチェーン、変革が進まぬ訳 日本の処方箋は「共通言語」と「図面データ」
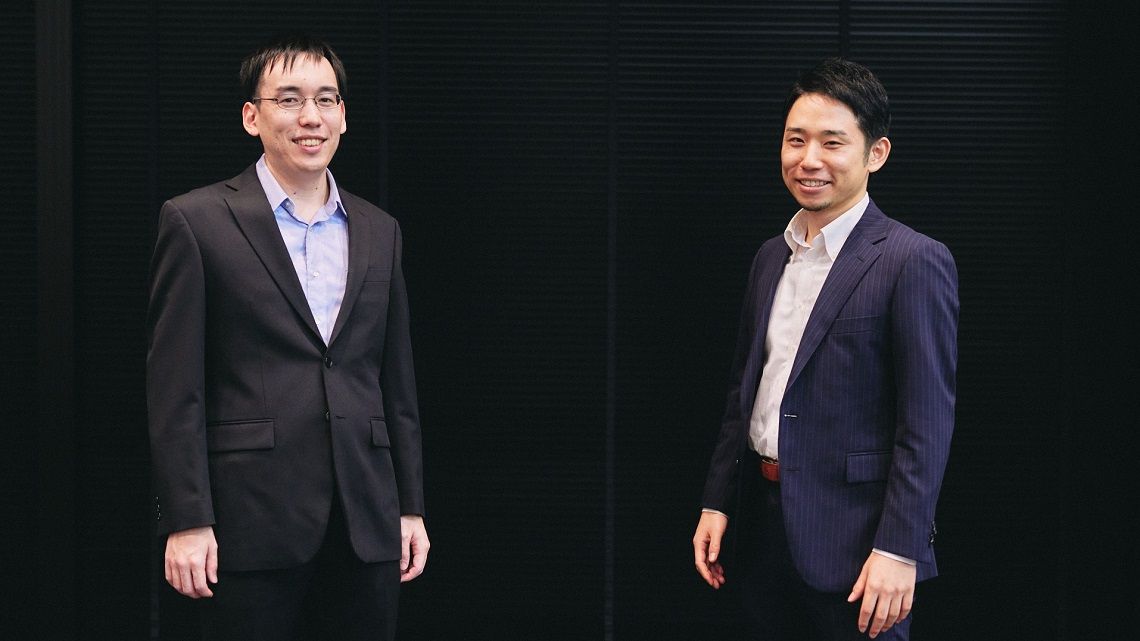
※出所:キャディ「地政学リスクによる製造業(食品・繊維・化学は除く)サプライチェーン・調達への影響調査」(2022年8月19日~23日、インターネット調査)
QCDは暗黙知ではなく「共通言語化」すべき時代
――コロナ禍や地政学的リスクの高まりで、サプライチェーンの分断が問題となっています。キャディの調査では、製造業の9割が計画どおりに調達先の見直しができていないとの結果が出たとのことですが、なぜサプライチェーン改革は進まないのでしょうか。
加藤 大きな理由は、製造業のほとんどが「大量生産・マーケット拡大」を前提とした下請け構造だということです。大量生産、かつGDPが拡大している高度経済成長期のようなタイミングにおいては、発注側(メーカー)とサプライヤー(加工工場)が固定的な関係でも、共に成長していける理にかなった構造でした。
しかし、それでは有事の対応はできません。加えて今は、複雑多様化したニーズに合わせる多品種少量生産の時代です。従来のように「いつもと同じで“よしなに”やってください」だと、QCD(品質・コスト・納期)を確保できません。かといって、メーカーが新しいサプライヤーにいきなり発注しても、「この図面ではよくわからない」と言われてしまいます。また、サプライヤー側も、顧客であるメーカー側が成長していないので、下請け構造に依存していると、いずれ破綻してしまいます。
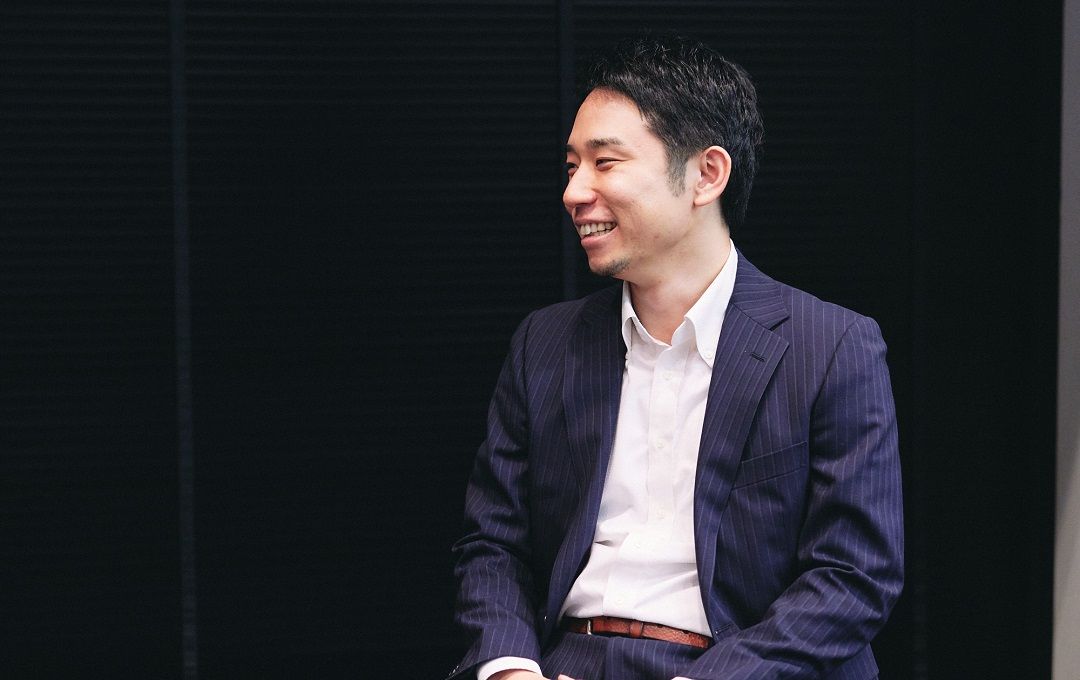
2014年に東京大学卒業後、外資大手コンサルティング会社に入社。16年にマネージャーとしてグローバルで製造業メーカーを多方面から支援するプロジェクトをリードする。とくに大手メーカーの購買・調達改革をサポートしたほか、IoT/Industry4.0領域を立ち上げ時から牽引。17年11月にキャディを創業
小橋 すり合わせや暗黙知に支えられたモノづくりだけで対処できる時代は終わったということですね。サプライヤーの選択肢を広げるうえで、海外からの調達も当然視野に入れる必要がありますが、「“よしなに”お願いします」というやり取りでは無理です。言語や文化、商習慣の違いといった部分とは別に、品質基準や設計仕様などを曖昧にせず、メーカー・サプライヤー間で通じる「共通言語」で表現し、信頼の根幹を築いていく必要があると感じています。
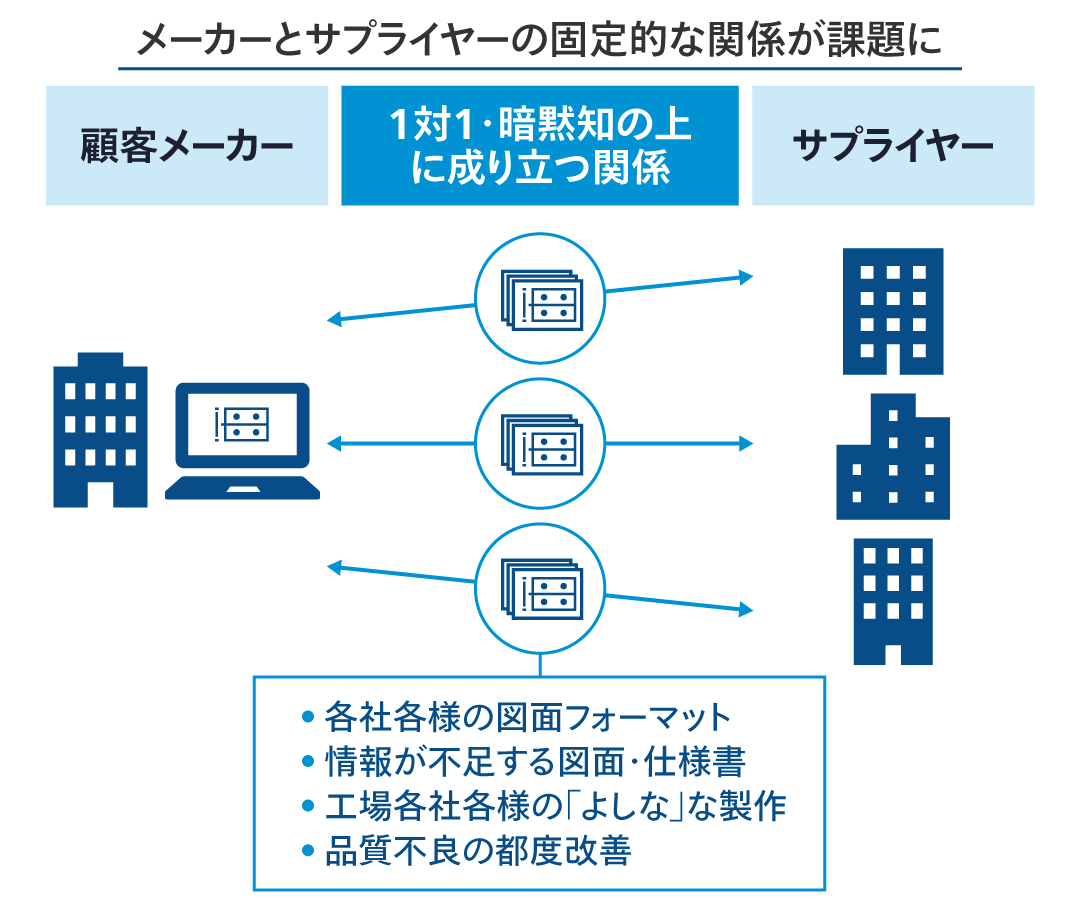
加藤 アメリカだとそれに近いやり取りがなされています。よくも悪くも、サプライヤー側の柔軟性が低いため、できないことはできないと明確に伝えるんですね。
日本だと「とにかく100%を目指してお互いに頑張りましょう」といった精神論に終始しがちですが、アメリカではサプライヤーから「品質を上げたければコストも上がるが、どうするのか」といった声が普通に上がります。
そういったやり取りだけでQCDを担保できるとは限りませんが、暗黙知ではなく「共通言語」を持ってやり取りできる下地があります。「共通言語」があれば、データドリブンな取り組みが可能となり、サプライチェーンの柔軟性につながります。
QCDを担保し納品責任まで負う「仮想工場」とは
――暗黙知から脱却して「共通言語」を持てるようにするには、どうすればいいのでしょうか。
加藤 まさしく「言うは易(やす)く行うは難(かた)し」で、現実の調達活動において暗黙知からすぐに脱却するのは困難だと思います。実際、「新しいサプライヤーに依頼したとき、品質不良やコストアップなどの困り事が起きていますか?」と調達担当者にお聞きすると、全員がイエスと答えるわけですよ。
サプライヤーにしてみれば、「図面に描かれていない情報が多い」「言われていたよりも工数がかかる」から仕方ないのですが、問題は、そういう課題が顕在化して何十年も経っているということです。そんな簡単に解決できる話じゃないんですね。
小橋 設計と調達、製造それぞれが分断されていて、サプライチェーンの中でデータがシェアされていないのが大きな問題なんです。だからお互いにフィードバックされないし、「共通言語」もつくれない。
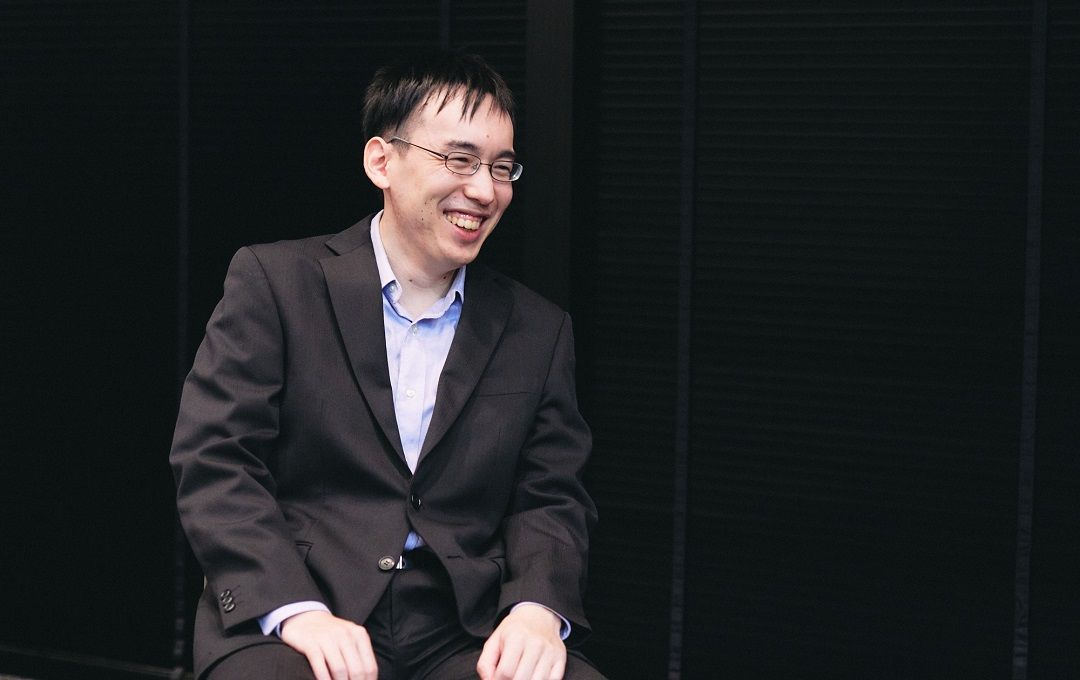
1990年生まれ。スタンフォード大学・大学院にて電子工学を専攻。在学中から米航空宇宙企業で勤務する。その後、米半導体企業で半導体セキュリティーの強化に従事したほか、米大手IT企業ではシニアエンジニアとして組み込み製品の開発をリード。2017年11月にキャディ創業に参画
加藤 製造業の現場と向き合い続けた結果、そういった現実がわかってきたので、私たちが暗黙知を「共通言語」に翻訳する役割を果たそうと考えました。それが、「調達・製造のワンストップパートナー」と位置づけている「CADDi MANUFACTURING(キャディ マニュファクチュアリング)」です。
――もともとキャディは、3D CADデータから「最短7秒」で見積もりを算出できる受発注プラットフォームを展開されていました。「CADDi MANUFACTURING」は、その発展形なのでしょうか。
加藤 はい。調達・製造機能のQCDを担保しつつ納品責任を負うサービスとして徐々に進化してきたため、「サプライチェーン変革をテクノロジーで支える存在になろう」という意思を込め、2022年10月に名称も刷新しました。
われわれは、単なるプラットフォームではなく、お客様から図面をいただいてから、図面解析や仕様翻訳、品質基準の標準化、そして検査、納品まで行っています。いわば世界中のサプライヤーをパートナーに持つ巨大な工場のような存在として、自分たちを「仮想工場=バーチャルファクトリー」と位置づけています。

補足をすると、お客様は変わらずに従来の暗黙知に頼った発注をしていただくことができます。暗黙知の部分の共通言語化をキャディが代わりに背負っているためです。
例えば、「傷なきこと」と記載があったとして、各社でその「傷がない」基準が異なります。そこでキャディが「A社はレベル1、B社はレベル2……」と基準を作って適用したうえで、サプライヤーに発注しています。また、お客様へのフィードバック機能を備えていますので、少しずつ業界全体の共通言語化が進んでいき、サプライチェーン変革の後押しもできることが特徴です。
テクノロジーを支える「業界への深い理解」
――「暗黙知を代わりに背負う」というのは、各社各様の図面を適切に読み取るということだと思います。それを実現したキャディのテクノロジーの源泉はどこにあるのでしょうか。
小橋 テクノロジー以前に、製造業という業界・業務への理解がやはり重要です。不世出の天才プログラマーがいたからといって、課題の解決はできません。当社では「CADDi MANUFACTURING」の開発運営を通して、製造業の現場の悩みや苦しみを肌で感じ、エンジニアも入り込むことで、実際に解決してきました。事業的な観点をリアリティーを持って理解できているからこそ、最適なソリューションが開発できると思っています。
具体的に言うと、無数の図面を見てきたことが大きいです。図面は暗黙知の塊のようなもので、設計者のクセがいろいろと出ているのですが、数多く見ることでどんな思いが込められているのかわかるようになりました。そうした深い理解が、キャディにとってのいちばんのアセットとなっています。
加藤 それによって結実したソリューションの1つが、図面データ活用クラウド「CADDi DRAWER(キャディ ドロワー)」です。創業から5年間ため続けてきたデータと知見を生かした独自の画像解析アルゴリズムを搭載しているので、高精度で探したい図面を検索・参照できます。
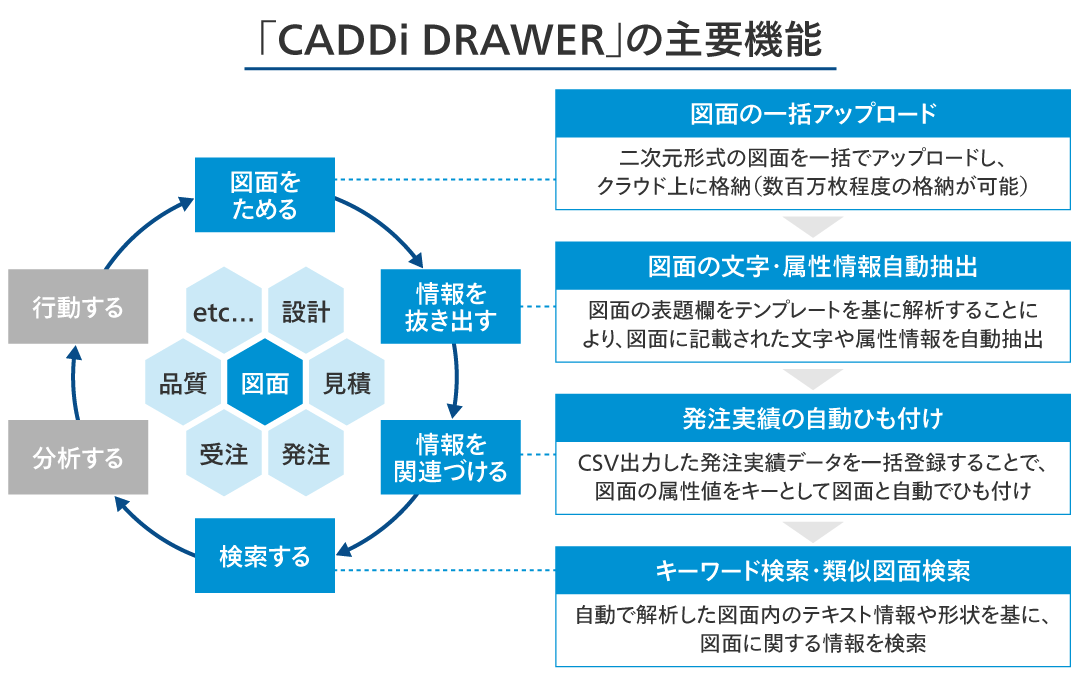
このソリューションはもともと、自社が膨大な図面を扱うに当たって「図番はもちろん、形状や部材、発注先などで図面を検索できるようにしたい」と考えたことが発端でした。このことをお客様にお話ししたところ、大きな反響をいただいたため、ご提供に踏み切った経緯があります。
モノづくりの現場では、「似た部品を1週間前に別の部署で設計した」ということがよくあります。でもそれがシェアされていなかったり、サーバー上にその図面データがあってもうまく探せなかったりして、またゼロから図面を描いている。
価格データも同様で、同じ部品を調達するのにまた相見積もりを取って、コスト交渉をして、結果的に2割も価格が高くなったということが普通に起きています。
「CADDi DRAWER」によって、図面データや発注データをアセット化できる。何度もゼロから図面を描いたり、不要な相見積もりを取ったりする手間をなくし、サプライチェーン全体のデータをアセット化できる未来を創りたいと考えています。
「ROIが高い」と導入を即決した経営トップも
――設計・調達の上流工程からサプライチェーンでのデータ共有・活用を可能とする「CADDi DRAWER」は、DXの推進にもつながりそうです。
小橋 製造を中心とした下流工程を仕組み化する「CADDi MANUFACTURING」と組み合わせることで、サプライチェーン全体の最適化にもつながります。おかげさまで「CADDi MANUFACTURING」は、産業機械業界における上位企業にQCD担保のメリットを感じていただいていますが、2022年6月に正式提供を開始したばかりの「CADDi DRAWER」も、すでに多くの大企業に導入いただいています。
加藤 キャディのミッションは「モノづくり産業のポテンシャルを解放する」ですが、とくに大企業には膨大な量の図面があり、アセット化されていない現状があります。いわば相当高いポテンシャルが眠っている状態ですので、「ROI(投下資本利益率)がすぐ出る」と大企業の経営トップが導入を即決した例もあります。
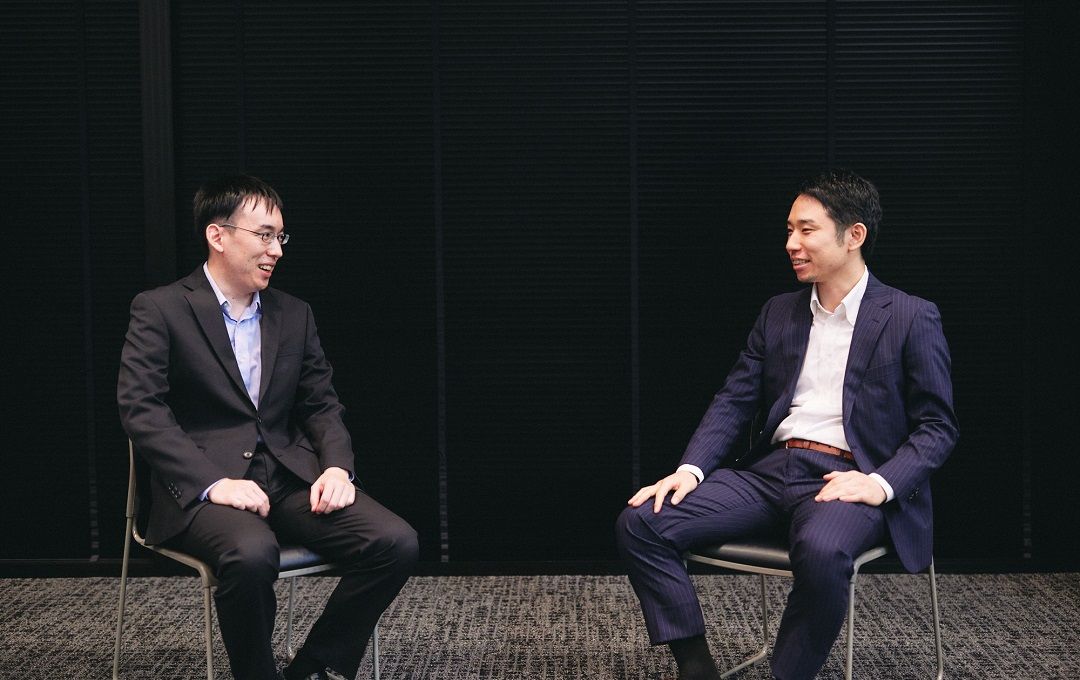
――サプライチェーン変革はもちろん、現状を取り巻く課題を打破したいと考える企業にとって有効なソリューションと言えそうです。一方で、変革したくてもどう進めていけばいいのか悩んでいる人も少なくないと思います。
小橋 そうした方に、変革の事例や奮闘している方々の取り組みを知っていただくため開催するのが、「Manufacturing DX Summit 2023」(23年1月25日~27日、オンライン開催)です。スピーカーとして東京エレクトロン元会長・社長の東哲郎さんや東芝社長の島田太郎さん、ソニーグループシニアアドバイザーの平井一夫さんなどそうそうたる方々に登壇いただき、製造業の未来について語っていただきます。
加藤 アメリカに滞在すると痛感するのは、人材の流動性の高さです。調達部門に20人いたら、それぞれ数社以上のバックグラウンドがあり、数十社以上のサプライヤーネットワークを築いています。つまり、それだけ多彩な情報とベストプラクティスが社内にあるということです。
日本はまだ人材の流動性が低く、同じことは望めません。ならば、擬似的であってもいろいろな知見に触れる機会を提供したい。そして、自社で変革を起こすきっかけにしていただきたい。それが、「Manufacturing DX Summit」を開催する理由です。
初めて開催した22年は予想を超える約1万人に参加いただきましたが、今回は3万人を目指しています。それだけ多くの人が同じ志を持っていると知ることにも大きな意味があると思いますので、ぜひご参加ください。
「Manufacturing DX Summit 2023 製造業DXとモノづくりの未来」
製造業界トップランナーの方々、企業経営や研究機関、製造業の新たな可能性に取り組む方々にご登壇いただき、デジタルを取り入れたビジネスモデル変革の挑戦や、業務プロセス刷新事例、そして事業のDXに踏み出すための経営論や思考方法など、幅広いセッションをご用意しています。本カンファレンスを通じて、進み続ける製造業×デジタルの今を体感してください。特設サイトはこちら