製造現場のデジタル化がもたらす本当の価値とは 身近な現場業務から始めるデジタル変革のカギ
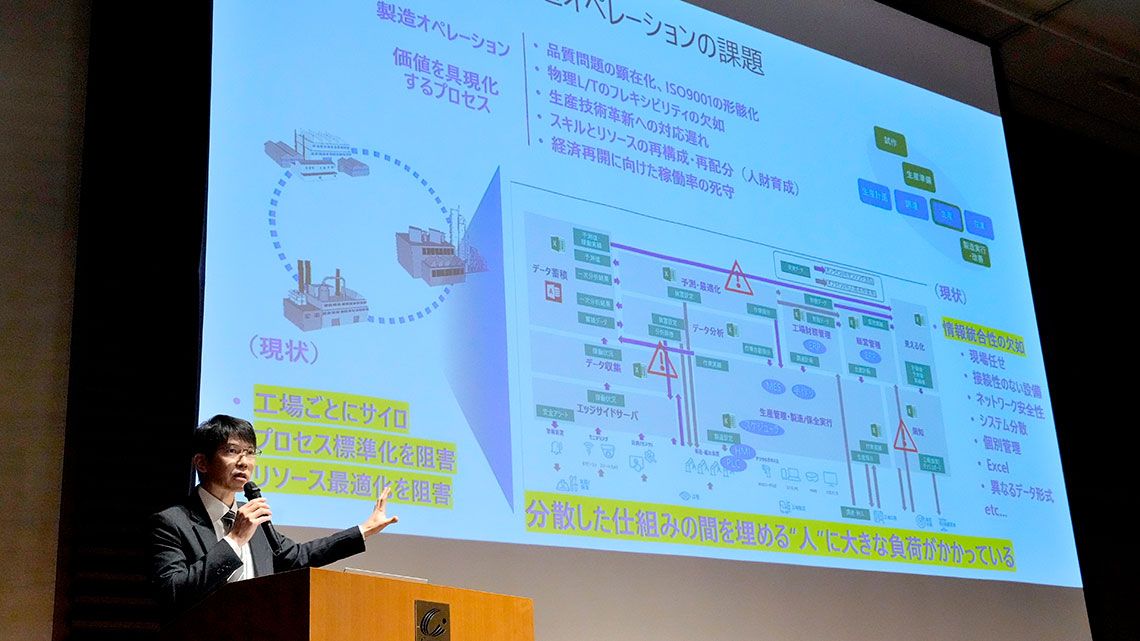
デジタル化へ向き合う3つのポイントとは
「家事労働を劇的に軽減した洗濯機には、実はより大きな歴史的意義があります」と指摘するのは東京大学大学院工学系研究科の森川博之教授。それは、「人々の衛生観念を変え、毎日の着替えを習慣化し、衣類市場を飛躍的に拡大させたことです」。
コロナ禍のデジタル化進展にも、今は気づけない大きな意義を100年後の歴史家は見いだすかもしれない。重要なのは、「潜在的な意義に気づくこと」だ。
では、どうすれば気づきを得られるのか。森川氏は、デジタル化へ向き合う3つのポイントを挙げる。
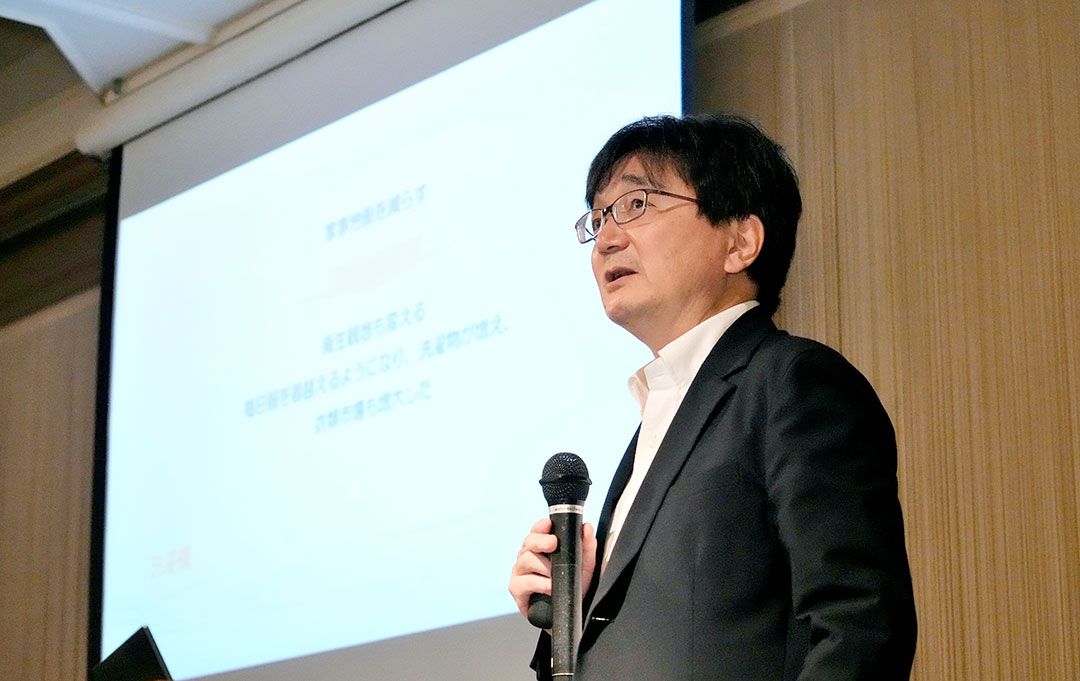
森川博之氏
まず、やってみること。「少々突飛なアイデアであっても、走りながら考え、ダメならやめればいいのです」。2つ目は多様性の尊重。森川氏は、性別などの属性より能力や知識など内面の多様性を重視することを勧めている。「テクノロジー企業がわざわざテクノロジーに疎い人を採用して、素人のような質問から気づきを得ることもあるのです」。そして、最後。「デジタル時代の幅広いステークホルダーそれぞれを、パズルゲームのピースに見立て、全体を俯瞰しながら適所に当てはめていく。いわば、つなげる価値創造です」。
デジタル変革には企業変革も同時に必要になる。「工場への電気導入は、蒸気機関前提の体制を再編しなければならなかったため、当初はなかなか進まなかった」と森川氏。デジタル化から、どのような気づきを得るのか。そこからどのように企業そのものを変革していくのか。デジタル化への向き合い方が問われているともいえるだろう。
デジタルツインは何を可視化するのか
実際、デジタル変革が急務な現場も少なくない。「人手不足、変種変量生産、原価高騰、脱炭素といった課題への対応を迫られて疲弊し、熟練従業員の退職で現場ノウハウも失われる危機にあります」。デジタルファクトリー構築を支援してきたコンソーシアム「Team Cross FA」の天野眞也氏は、日本の製造現場の現状に危機感を抱いている。
「ピンチをチャンスに変えるには製造現場のDXが急務です。デジタルツインで投資対効果を算出すればDX投資も加速できる。デジタルツインは身近に使われているテクノロジーで難しいことではありません」と天野氏。実際、現実の道路の混雑状況を把握して到着時刻を予想するカーナビアプリはデジタルツインの一例ともいえるが、すでに多くの人が使っている。
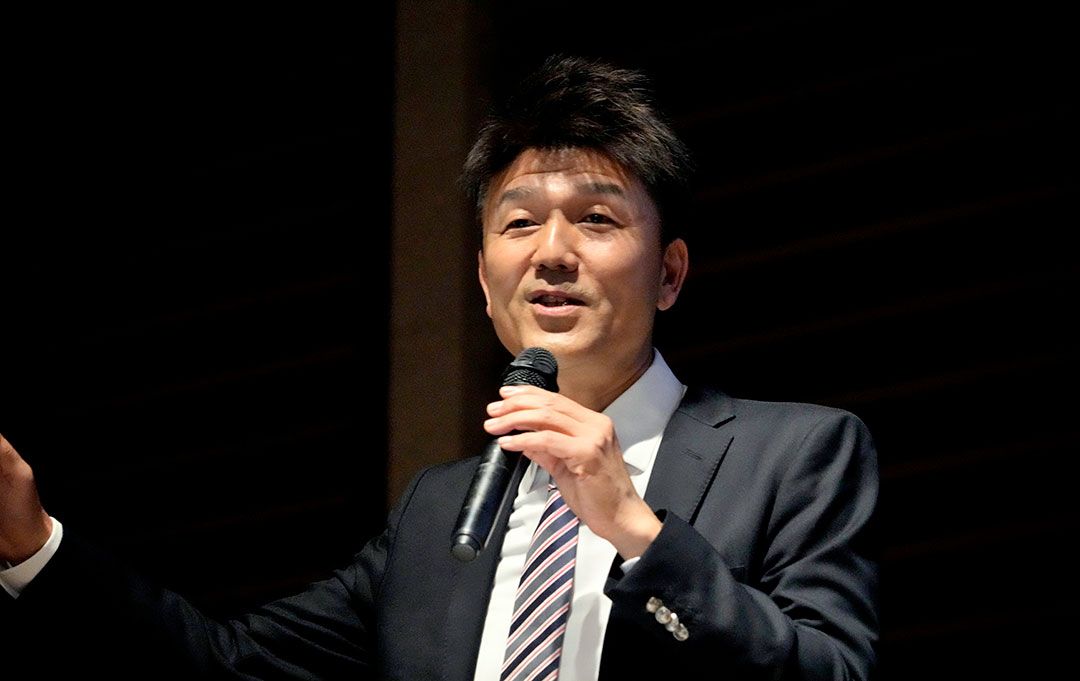
天野眞也氏
天野氏は続ける。「工場設備を含むサプライチェーンをデジタルツインでシミュレーションすれば、生産能力のボトルネックが明らかになり、全体最適化のために解決すべき課題、投資が必要な箇所もわかるでしょう」。
デジタルツインで各部門・従業員の貢献度を測れば、適切な報酬、優秀な人材の維持も可能だ。しかも、最適化された工場はグリーントランスフォーメーションへの道を開いていく。天野氏は「デジタルツインの推進は、日本のものづくりの復権に必ずつながる」と信じて疑わない。
デジタルツインの日本版「トリプレット」とは何か
「デジタルツイン」に、さらに「知的活動世界」を加えた「デジタル・トリプレット」の必要性を説くのは、東京大学大学院工学系研究科人工物工学研究センターの梅田靖教授だ。
競争力を向上させるためには、工場のデジタル化プラスアルファが重要。「しかし」と梅田氏は「日本のものづくりは、まだデジタル時代の新たな価値創造のあり方を見いだせずにいます」と指摘する。
「日本メーカーの強みを生かしてIoTデータから価値を生み出す戦略を考える必要があるでしょう」。そこで、梅田氏が提案するのが、冒頭で紹介した「デジタル・トリプレット」だ。
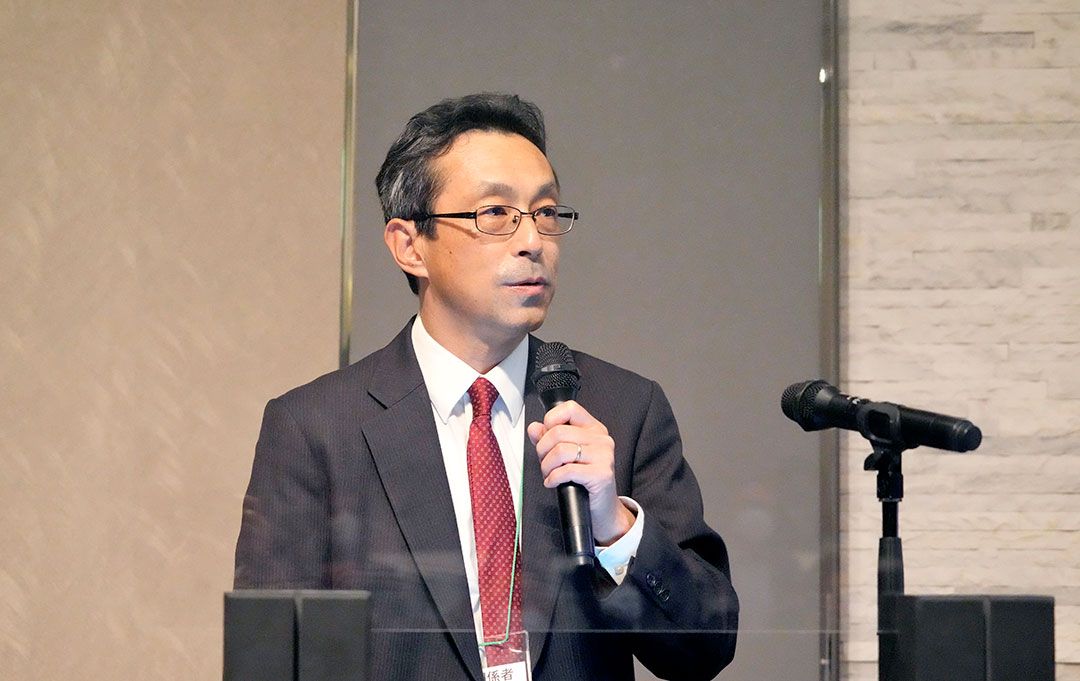
梅田 靖氏
「生産システムの自動制御を志向する欧州型デジタルツインに、現場の工夫が関われる余地はありません。現場のカイゼンを強みとする日本は、熟練技術者がデジタルツインの中に生産システムを進化させる『知的活動』を取り入れることで価値を生み出せるはずです」と梅田氏は言う。
知的活動は問題解決のノウハウをあらかじめ用意することで、熟練者でなくても可能になる。「学習用の自動化工場を舞台にした研究では、発生したトラブルに対する熟練技術者の解決法を観察してデジタルに記述。その蓄積を基に作った問題解決プロセスモデルを学んだ学生は、熟練者と同じ解決案にたどり着く確率が上がりました」と研究の成果を披露。「熟練者の暗黙知を形式知化して知識継承するアプローチとしても有効」と期待している。
製造現場のデジタル化を可能にする環境変化とは
デジタルツインをはじめとするテクノロジーの有効性は理解できても、実際の運用に不安を抱く声もあるだろう。専門知識のない現場担当者が新しいデジタルテクノロジーを使いこなし、投資に見合った成果を得るのは難しいのではないか、と。しかし、日本マイクロソフトで製造業ソリューションに携わる鈴木靖隆氏は「状況は変わりました」と語る。
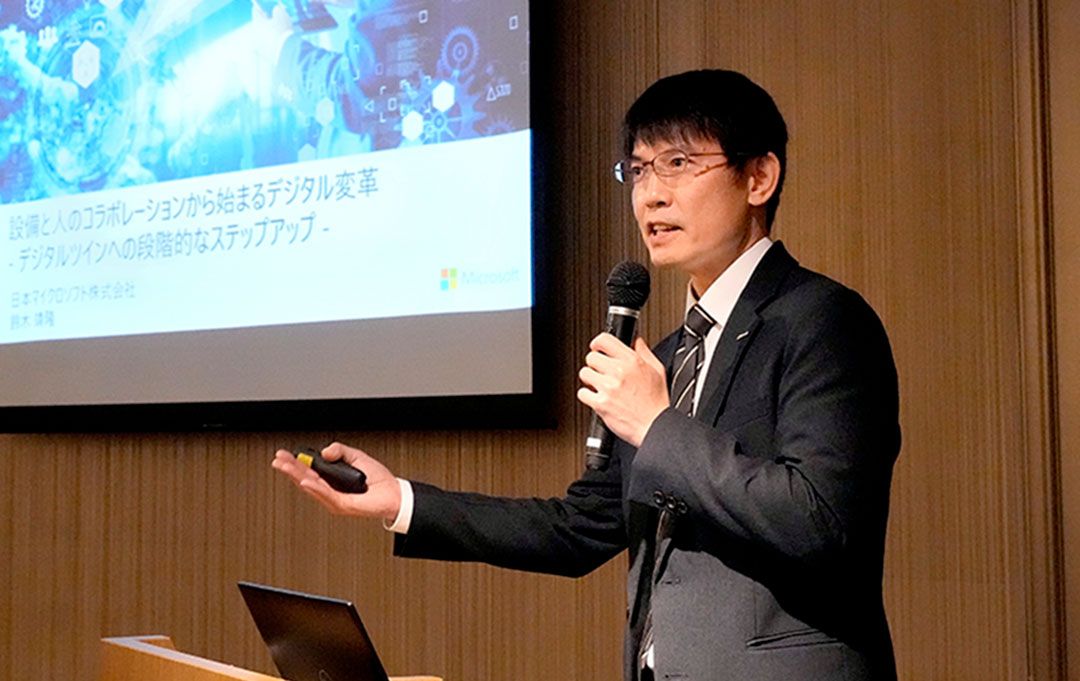
鈴木靖隆氏
「テクノロジーを扱うハードルが下がり、AI(人工知能)、機械学習でさえ、高度な知識がない現場担当者でもマウス操作でデザインできます。必要な機能だけを課金制クラウドサービスで使えば、多額の初期投資も不要です」
製造現場のデジタル化着手に当たって考えるべきポイントは、まずデジタルツインで設備からデータを収集し、それを分析して解釈する人につなげる仕組みをつくること。分析にはAIを使うことも容易だ。実際、実践に移したリコーやコマツ産機では成果を上げているようだ。
「製造現場でやりたいことを可能にする使いやすいサービスはここにあります。ぜひトライしてください」と鈴木氏は語りかける。
(日本マイクロソフトの講演動画は本ページ末尾のリンクから視聴できる)
カギは、現場による現場のためのツール開発
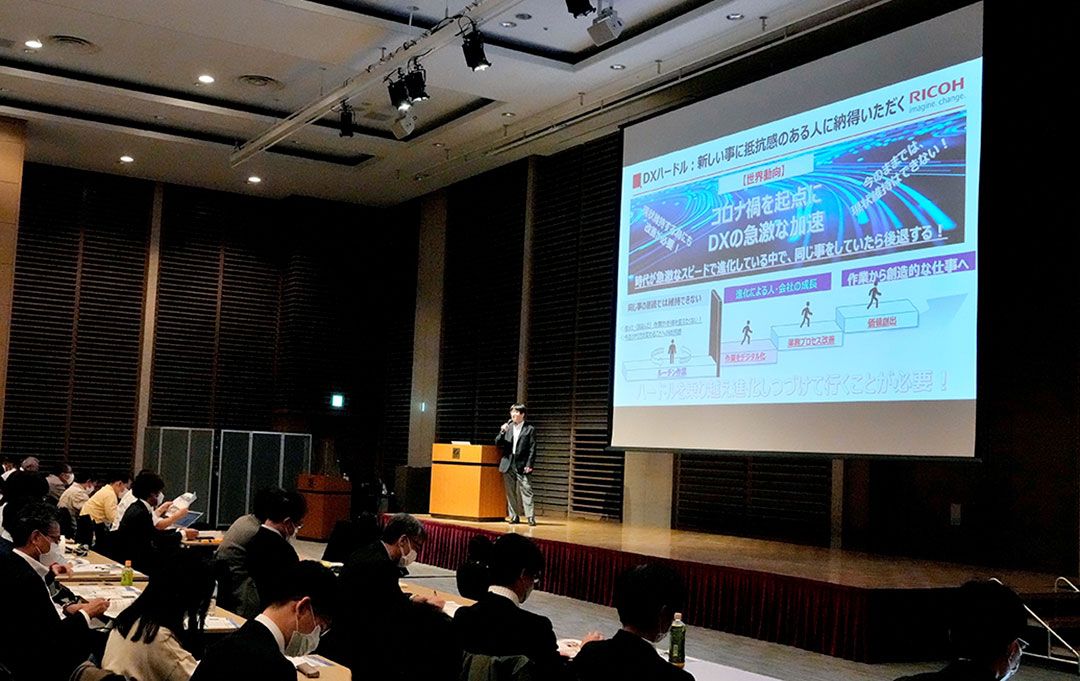
実際に、現場の強い関与で製造現場のやりたいことを実現しているのがリコーだ。
リコーの増田彰氏が振り返る。「一般的に、効率化やコスト削減といった会社都合の目的が前面に出るDXでは、現場が疲弊し、協力も得にくくなります。そこで、経営から示される会社としてのDX戦略にプラスして、ボトムアップ型DX活動に取り組んできました」。
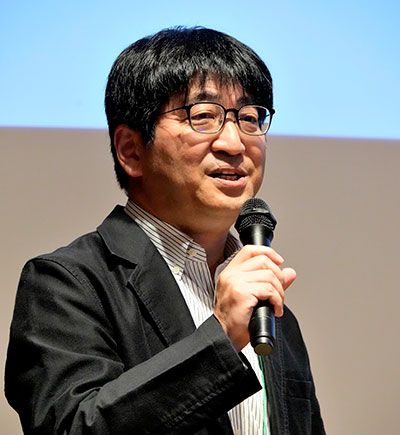
経営管理本部 経営管理センター
品質システム統括室 室長
増田 彰氏
ボトムアップ型DXでは、『マンネリ、面倒くさい、ミスできない』の3Mをはじめ、現場の困り事の解決を目指した。
その成果の1つが、出荷検査で発見された不具合への対応に関する情報を一元管理するアプリの開発だ。「従来は、不具合があると該当機種の担当者が、電話などで技術部門に原因調査を依頼し、後で調査結果を問い合わせて報告をまとめる煩雑なプロセスが必要でした」と増田氏。リコーの中島崇氏が後を受ける。
「電話が主流だったやり取りが、ほぼチャットに置き換わったように、コミュニケーションがデータとして記録されるようになりました。このデータを業務アプリと連携させれば、仕事が劇的に変わるはず、という発想が、アプリ開発のきっかけでした」
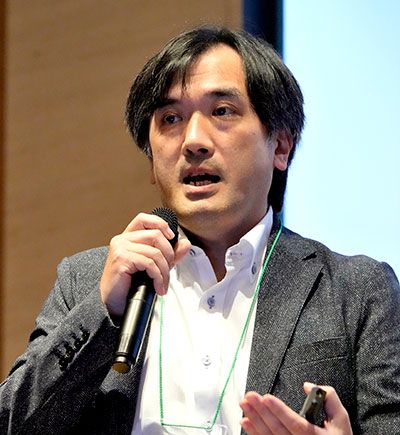
商品事業統括本部 技術開発センター
DX推進グループ 業務改善エキスパート
中島 崇氏
このアプリ開発に当たっては、専門知識がない人でも開発ができるローコードアプリ作成ツール「Microsoft Power Apps」を使い、品質保証の現場が大きな役割を果たした。まず、社内で現場業務改善のアイデアを募集。埋もれていたデジタルを活用してカイゼンしたいという意欲を持つ“デジタル人材”を発掘しつつ、寄せられたアイデアをソリューションにする取り組みを進めた。
「ITが生活に浸透してアイデアを持つ人も増え、DXという追い風も大きな後押しとなりました。ローコード開発ツールの存在が、現場による現場のためのデジタル化を進められる環境を可能にしたと実感しています」と中島氏。
結果、「情報一元化により対応を簡潔・迅速化でき、調査報告も充実できました」と増田氏は成果を語る。
「困り事が身近にある現場は、デジタル化のチャンスであふれています。カイゼンマインドを持つ現場は、人々をワクワクさせるというIT本来の魅力を備えたアプリを開発できるはずです」と中島氏は、その次を見据えているようだ。
AI評価モデルで適切なメンテナンスを実現
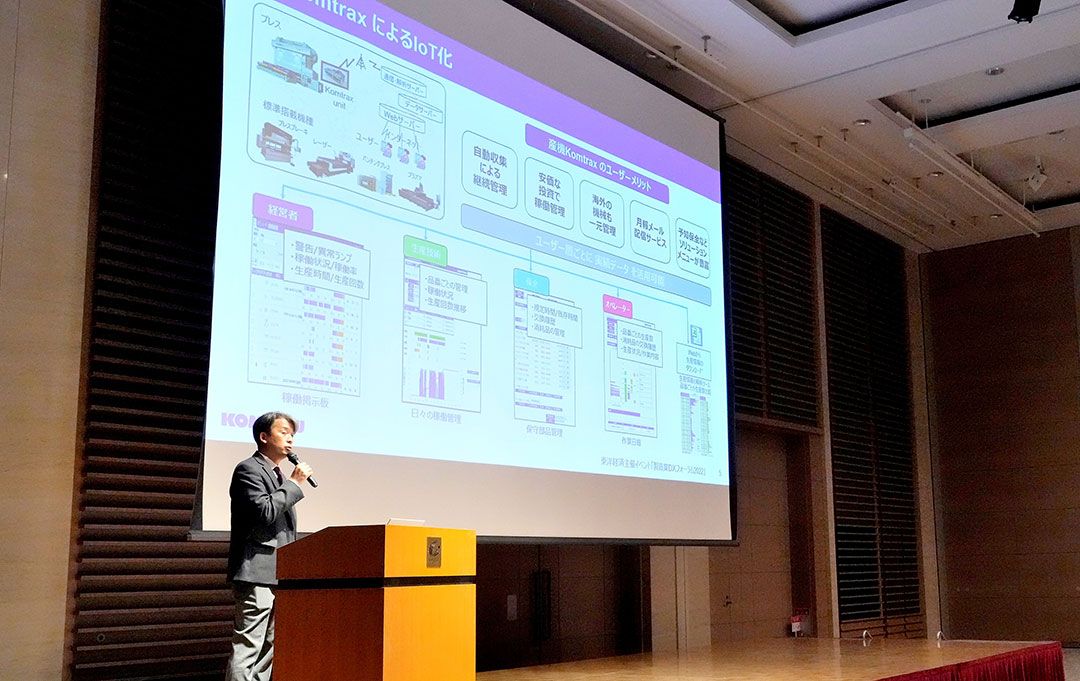
IT活用の先進的な企業も、デジタル化による改革の手綱を緩めてはいないようだ。
建機の遠隔稼働管理システム「Komtrax(コムトラックス)」で知られるコマツ。そのグループの産業機械メーカー・コマツ産機も2009年にIoT化に舵を切った。同年、プレス機械および板金機械の量産機に「産機Komtrax」を搭載。稼働状況のデータなどをユーザーと共有する一方、故障の予兆を検知してメンテナンスを行う「予知保全」の実現に向けた取り組みを進めてきた。
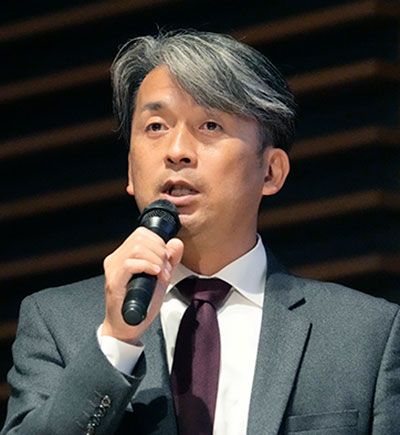
ICTビジネス推進室 副室長
大関慎也氏
「故障後に対応する『事後保全』は生産ライン停止に伴う損失が生じます。そこで定期的に部品を交換する『定期保全』をするのですが、交換サイクルが短く、コストがかさむという課題がありました。『予知保全』なら保全コストを最適化できます」とコマツ産機 ICTビジネス推進室の大関慎也副室長は説明する。
ただ、機械にセンサーを外付けして状態を監視しようとすると機械がセンサーだらけになり保全コストがかかるなどの問題が生じ、うまくいかなかった。そこで、Komtraxを搭載した機械の自動制御装置駆動部からデータを収集し、「Microsoft Azure Machine Learning」のクラウドサーバーに送信する仕組みを構築。まずは振動波形の特徴量から異常の有無を機械側のKomtraxで判断できるようにした。
「さらにAzureのAIを使って振動波形を解析し、劣化部位を特定できる評価モデルを作成し、部位の特定が可能になりました。評価モデルは新しいデータを加えた学習を繰り返すことで継続的に更新され、精度をさらに高めています」
各駆動部の部品の状態は、劣化レベルに応じて青から黄、赤へと変化するグラフをユーザー向けウェブサイトに掲載。寿命低下を知らせるお知らせメール機能なども備えた。
大関氏は「当社の予知保全はAzureの各種サービスを利用することで成り立っています。この仕組みはほかのさまざまなシーンに応用できると思います」と語った。
(コマツ産機の講演動画は本ページ末尾のリンクから視聴できる)