製造業のデジタル変革実現を本気で考える! DXプロジェクトを成功に導くポイント
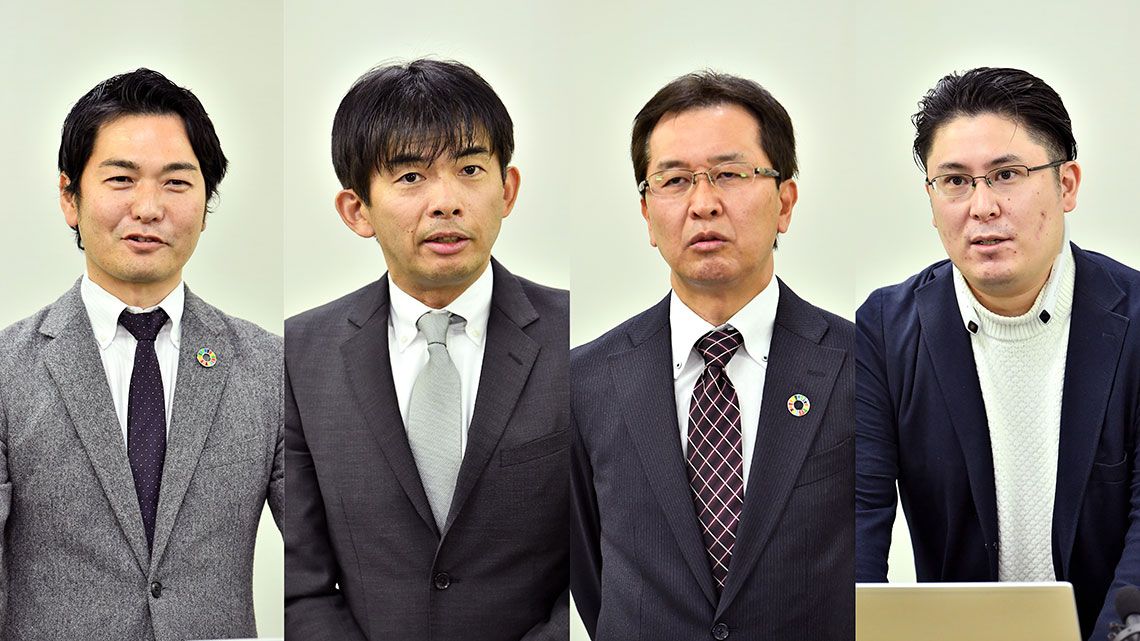
主催:東洋経済新報社
協賛:マクニカ
基調講演
ソフトパワーのデジタル化でグローバル競争力を高める現場力DX「コネクテッド・ワーカー」の紹介
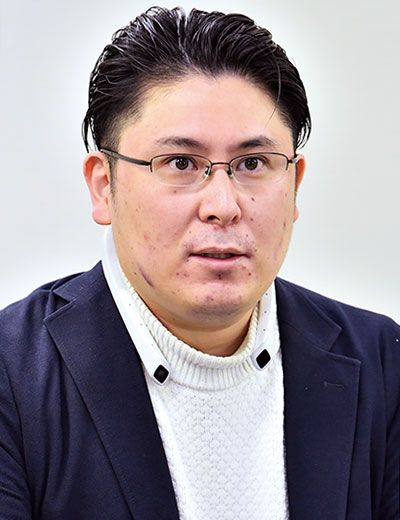
執行役員 COO
久池井 淳氏
先進的なウェアラブル機器と音声技術などを使って現場のDX支援に取り組むフェアリーデバイセズの久池井淳氏は、デジタルツインの実現には、IoTなど機器のデジタル化と同時に、人の業務をデジタル化してデータを取得する必要があると指摘した。現場の作業員が装着するウェアラブル端末から、作業視界の映像や現場のやり取りの音声をテキスト化したデータなどを取得。これら現場データを活用して、工場などの現場作業の効率化・高度化を図るソリューション「コネクテッド・ワーカー」を紹介した。
現場作業の改善や、熟練工による新人作業員の遠隔支援に使えるほか、マニュアルや日報を半自動的に作成して現場の非コア業務の負担を軽減。また、データを蓄積してAIに学習させれば、熟練者の経験・ノウハウといった暗黙知を形式知化して継承できる「熟練工AI」につなげられる。久池井氏は「日本の高度な現場力を再現できる熟練工AIをデジタルツイン上で働かせれば、日本から海外現場を制御することも可能。属人的とされてきた日本水準の操業を世界中で可能にする熟練工AIによって、グローバルに稼げるようになるかもしれない」と訴えた。
特別講演
ニューノーマルな時代におけるデジタルマニュファクチュアリング(DM)による働き方変革
~グローバル展開の考え方と人に着目したものづくり現場の可視化&改善事例をご紹介~
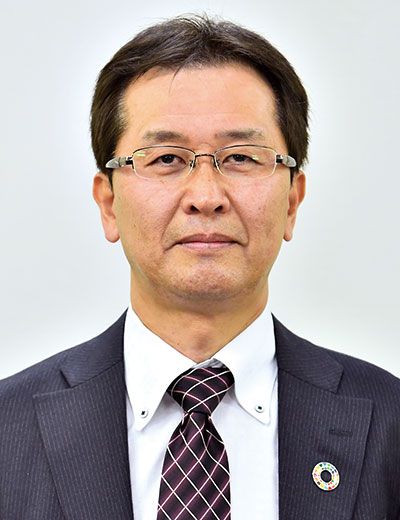
生産本部
デジタルものづくり革新センター
DM開発・推進室 室長
森田 雅則氏
リコーの森田雅則氏は、これまでの製造現場の「日常」をデジタル技術で変革。現場は自動化や高付加価値業務に注力し、管理はリモート化してリアルタイムでモニタリングを行い、経営は国内外に散らばる生産拠点を1つの工場として認識できるようにするバーチャル・ワン・ファクトリーを目指す「デジタルマニュファクチュアリング」(DM)の取り組みを説明した。同社は、世界主要8拠点で同時にDMを推進するため、QCD(品質・コスト・納期)向上などの共通目的を策定。現場業務を13領域・44モデル業務に分類した基本フレームワークを作って取得するデータを明確にした。データ蓄積もルールを決めて標準化。月12万3000時間の工数削減を目指して252の施策を推進している。
生産管理ダッシュボードでは、作業員の出勤、製造工程のトラブルを現場で確認しなくてもリモートでリアルタイムに把握できる。また、すべての工程は常時、ウェブカメラでモニタリングして、トラブル発生前後の映像を検証作業に役立てている。コロナ禍で働き方が変わる今、森田氏は「アナログ時代の当たり前を変革するチャンスだ」と語った。
パートナー企業講演
Industrie4.0を推し進めるドイツから学ぶ、製造業DX成功の秘訣
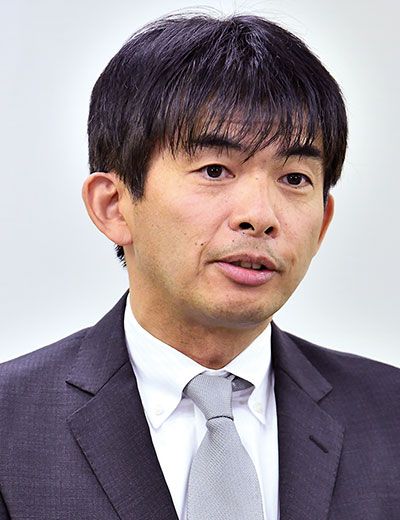
技術本部
製造ソリューション部
部長
野田 智孝氏
自社で推進するDXの成果を基に、産業のデジタル化を支援するシーメンスの野田智孝氏は、顧客ニーズの高度化や製品ライフサイクルの短命化で「ものづくり企業は大きなプレッシャーにさらされている」と指摘。製品開発・工程設計から製造現場までのエンジニアリングチェーンの情報の標準化を目指す同社の考え方を紹介した。これにより、製造現場から開発・工程設計へのフィードバックを速く確実にすることで、製品開発力と品質向上、市場投入スピード向上による受注拡大や収益拡大などの全社的価値を創出する。
組織横断で進みにくいDXについて、企画にかかる時間を抑えて効果を引き出す同社の「Prescriptive(模範的)アプローチ」の考え方を紹介した。部門ごとに課題を「見える化」して改善を積み上げる従来の記述的アプローチに対し、模範的アプローチでは、各部門が連携して、最初に定めた全社的目標を達成する。市場競争で生き残りノウハウと最新テクノロジーが蓄積された最新パッケージソフトやITの使いこなし、全社的目標を達成することを主眼としたフィット・トゥ・スタンダードな新たな業務プロセスを作り上げる。
中国の同社スマート工場では、情報基盤を整えたことで、生産量が増えても改善などに関わる間接工人員を増やさない仕組みを実現したと紹介。「製造現場に魔法はない」と述べて、合理的変革とともに地道な現場啓蒙活動の重要性も訴えた。
協賛企業講演
難解な製造業DXのはじめの一歩
~経営と現場をつなぐデジタルツイン~
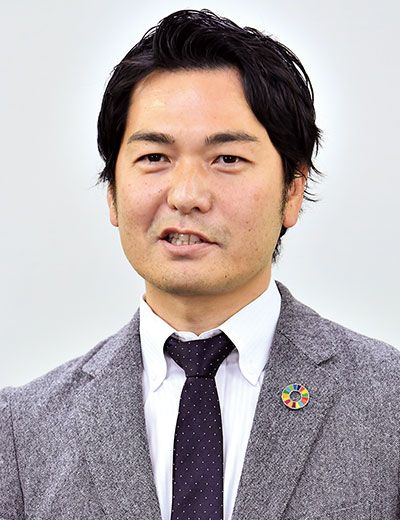
イノベーション戦略事業本部
ソリューション事業部
事業部長
阿部 幸太氏
多くの企業のDXプロジェクトを支援してきたマクニカの阿部幸太氏は、DXの最大の障害は、経営層、各部門との間に立って、業務プロセス変更や部門間連携を調整するDXプロジェクトチームが抱えるコミュニケーションの困難さにあると指摘。「はじめの一歩」としてデジタルでコミュニケーションのハードルを下げることを提案した。
プロジェクトは、健康診断(現状分析)、シミュレーション、フィット・トゥ・スタンダードの3つがポイントになる。最初の健康診断では、テンプレートを使い、現状業務プロセスの迅速で低コストな可視化を提案。次に「体験に勝るコミュニケーションはない」として、デジタルツイン技術のシミュレーションを使って経営層、各部門とコミュニケーションを図ることを推奨した。精度は「大まかな傾向をつかめれば十分。時間、コストをかけて作り込みすぎないことが重要」と強調。さまざまなシミュレーションのテンプレートを持つ同社のようなエンジニアリングパートナーの活用を促した。フィット・トゥ・スタンダードでは、製造業向けデジタル基盤のパッケージシステムに合わせて業務プロセスを変更するか、バージョンアップに追従できなくなるアドオンを開発するかという議論は机上では結論が出ない。まずは標準業務を体験してみることから始める例が増えていると説明した。
Q&Aセッション
ニューノーマル時代到来!
製造業のデジタル変革実現を本気で考える!
講演者が視聴者の質問に答えた。容量が膨大なカメラのモニタリングデータの扱いについて、森田氏は、ルールを決め、保存するデータ以外は一定期間経過後に捨てていると説明。「DXの目的はあくまでカイゼンで、ツールがアナログからデジタルに変わるだけ。必要なデータは現場主導で決めることが大事」と答えた。新システム導入の際に既存システムをどうしたらいいか、という質問には、野田氏が「すべて刷新することはありえないので、目的に合わせてコア部分から進める。既存システムとの連携は、マスターデータをどこで作り、どう利用するかという観点が大事」と回答。久池井氏も「規模が大きくない企業の場合は、人と既存システムで動いている部分のうち、人の部分からDXを行うというやり方もある」と答えた。
アーカイブ配信についてはこちら