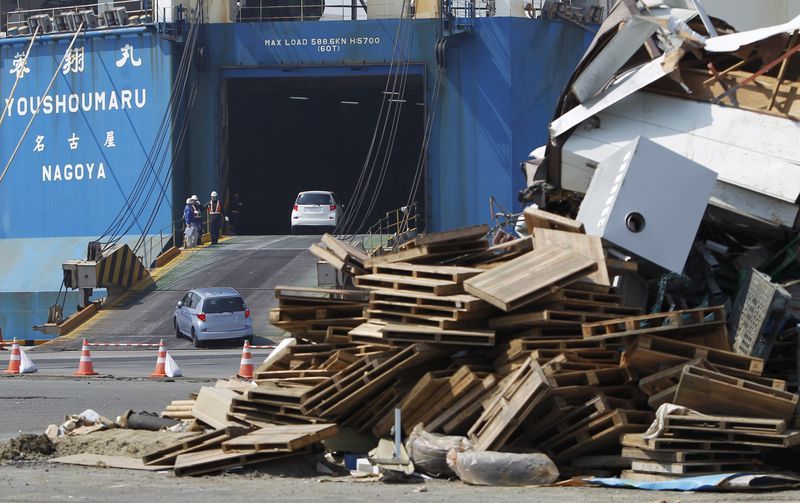
TOKYO (Reuters) - Five years after a huge earthquake temporarily crippled parts of Japan's auto supply chain, some companies have adjusted the industry's famed "Just in Time" production philosophy in a bid to limit any repeat of the costly global disruption.
The quake exposed the vulnerability of a system pioneered after World War Two by Toyota Motor, under which companies aim to boost efficiency by receiving small quantities of parts from suppliers only when needed.
But even with the risk of new disasters in one of the world's most seismically active countries businesses have had to balance efforts to disaster proof the supply chain due to concerns of the cost of, say, storing more inventory in case of an emergency which may or may not strike.
"Holding more inventory, or adding another production line as a business contingency measure may improve a company's robustness in the face of disaster, but it won't necessarily improve its global competitiveness," said supply chain expert Takahiro Fujimoto.
"Companies which take such steps at the cost of competitiveness would probably go bust even before the next disaster occurs," said Fujimoto, a professor and executive director at Tokyo University's Manufacturing Management Research Center.
Since the 2011 disaster, global auto suppliers have changed the way they produce and source the 30,000 parts required to assemble a single car, including raising stocks, diversifying production and creating alternative manufacturing capabilities.
German drugs and chemicals maker Merck said it has "significantly" increased its supplies of Xirallic, a pigment which creates the shimmery effect in vehicle paint, since the quake.
Merck's plant in Fukushima Prefecture, which at the time produced the firm's global Xirallic supply, escaped major damage, but its warehouse was inaccessible immediately after the quake, prompting automakers including Ford and Chrysler to suspend sales of vehicles in certain colors.
Nils Oldenburg, head of Merck's global pigments production, who was in charge of operations in Japan at the time of the quake, said Merck now keeps "multi-month" stocks of Xirallic at warehouses in Japan and other regions around the world.
Merck in 2012 also began a second Xirallic production line in Germany.
Dual sourcing, dual capacity
Other auto parts companies are also giving themselves more leeway on inventories. German-U.S. supplier ZF-TRW said it had increased stocks of some parts procured from single sources to last six days, double the three days it held before the quake.
But industry experts say that many Japanese firms are sticking to "Just in time", opting not to increase inventories.
"The costs of maintaining extra inventory, or the view that extra inventory may be wasteful are considered to be reasons not to hold more stock," said Hiroaki Mochida, an analyst at Marusan Securities.
A spokesman at Japan's Renesas Electronics whose plant in Ibaraki Prefecture that produces microcontrollers used in automobiles was devastated in 2011, said it had not increased its inventories as a risk management strategy.
However, he said it had begun to standardize more parts across vehicle models to improve efficiency and enable alternative production during emergencies.
Tokyo University's Fujimoto said having capacity to transfer production to other lines was key to a quick recovery from disasters.
TRW, which specializes in vehicle safety systems and was acquired by ZF Automotive last year, now stores back-up production equipment at more of its suppliers' plants.
"In the past we believed that having moulds for some plastic parts at only one of our suppliers' plants, say either in the U.S. or China, would suffice, but now we have backups at other locations," said Yoshihiro Nakane, president of TRW Automotive Japan.
The quake was also a wake-up call for automakers to keep better track of procurement.
Toyota Motor, which spent weeks identifying how its suppliers had been affected by the quake, and Nissan Motor have both developed supply chain databases.
Nissan now also requires prospective suppliers to include alternative sourcing plans for parts for new models.
(Reporting by Naomi Tajitsu; Additional reporting by Maki Shiraki and Makiko Yamazaki; Editing by Ed Davies)