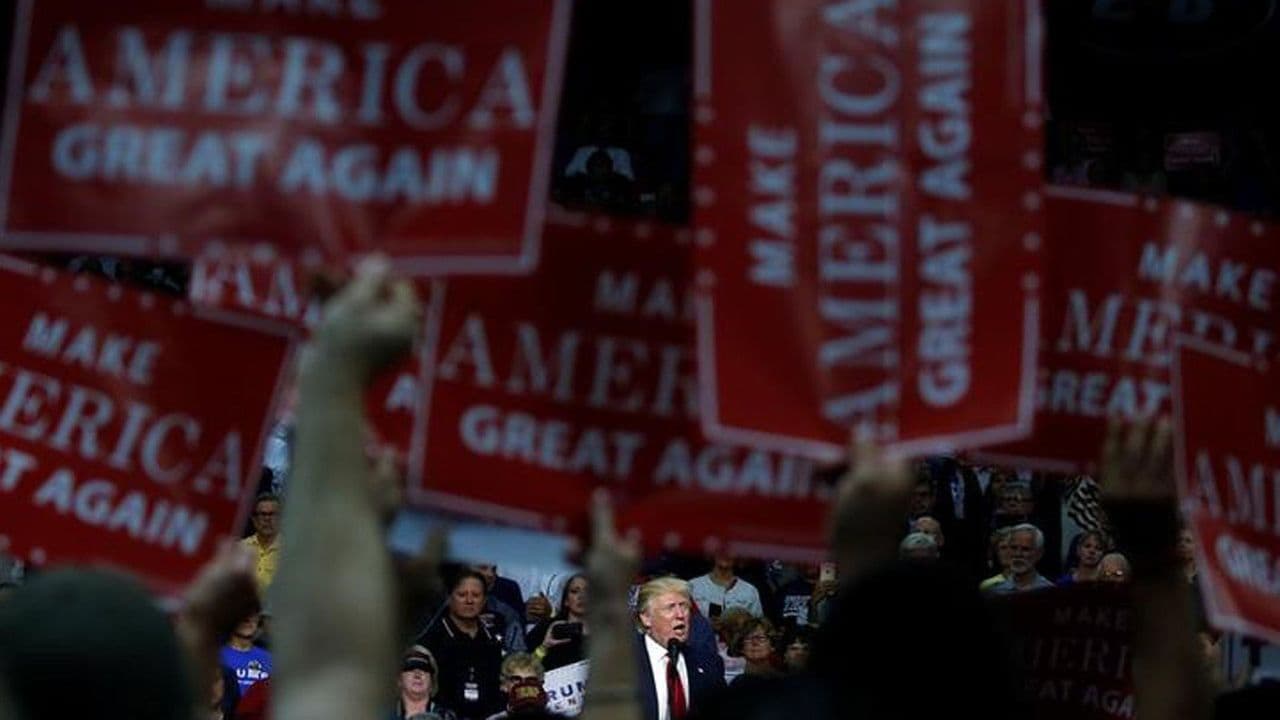
When President-elect Donald Trump fired off a Tweet accusing Toyota’s new auto plant investment in Mexico of hurting US production, he got his facts wrong, as he often does. In November, Toyota started construction on a $1 billion assembly plant in Mexico to make Corollas. But it is not moving any production from the US to build this plant. It is moving some production from Canada.
The larger point is this: when it comes to growth in US auto production, transplants from Japan, Korea and Germany are the drivers. Thirty-five years after the first made-in-America Honda rolled off the assembly line in Ohio, vehicles made by the Japanese transplants alone now account for a third (31%) of all motor vehicle production in the US. In fact, they account for virtually all of the growth in US auto output in the past 35 years.
Back in 1980, US motor vehicle output (cars plus trucks) totaled 8.01 million units. By 2015, total output had increased by 4.1 million units to 12.1 million. But 94% of that 4 million unit increase came from the Japanese transplants. The hike in production by the Detroit Three, Volkswagen, Hyundai and all the rest amounted to a tiny 240,000 units. And all of that increase came from the Korean and German firms. US companies closed nearly a couple dozen factories.
Moreover, some firms, like Honda, now export more cars from the US than they import from Japan.
Life has changed a lot since the early 1980s, when the Reagan administration got Tokyo to put a limit on car exports to the US via a deal called a “Voluntary Export Restraint” pact. In response to that, Japanese firms shifted from exporting to the US from Japan to building cars in the US, and buying parts from firms located on US soil. In 2015, the transplants produced 3.85 million vehicles, 71% of all Japanese auto sales in the US.
If we looked at just passenger cars alone, and did not include light trucks, the Japanese transplant account for 42% of all production—more than Detroit’s 37%. That’s because Detroit no longer knows how to make profits on small and medium-sized cars. So, it now focuses on larger cars, luxury models, and light trucks, from SUVs to pickups.
In 2016, three-quarters of all the vehicles sold by the Detroit Three were light trucks like SUVs and pick-ups. Conversely, 55% of the foreign brand vehicles were cars. So, Detroit does better in times like the present, when gasoline prices are low and people go for SUVs and pickup trucks. The foreign brands gain share when gasoline prices are high.
There is yet another point missed by Trump. Yes, US auto employment is down, but very little of that is because of imports taking away American jobs, or Detroit sending jobs off to Mexico. Rather, automation and other productivity-enhancers took away those jobs.
In 2016, factories on American soil produced more vehicles than they did back in 2000, but did so with 30% fewer workers in auto parts and auto assembly put together. This figure underestimates the impact of productivity because a larger share of the US output are the more expensive and complex SUVs and pickup trucks. Back in 2000, it took 12 workers laboring for a year to produce $1 million worth of auto parts and vehicles; now, it half that many.
If it still took as many workers to produce $1 million worth of auto output as in 2000, jobs would be up 44% (up 610,000) instead of down 30% (down 390,000). This dwarfs the impact of imports and “runaway factories.” Suppose there had been no trade deficit in either 2000 or 2015. In that case, jobs would have fallen 27% instead of 30%. There’s hardly any difference.
Tweeting is easy. Solving problems—like what does a 45-year-old laid off auto worker with just a high school diplomat do?— is hard. Trump doesn’t seem to know the difference.