Yamaha’s Toyooka Plant is located in Iwata City, Shizuoka Prefecture, which offers a view of Japan’s emblematic Mt. Fuji nearby. This is a production center for musical instruments that boasts a worldwide scale. A variety of instruments including trumpets, clarinets, saxophones, and tubas are manufactured here.
In a corner of this enormous plant is a space no larger than a school classroom which is filled with well-worn equipment and molds. With these, craftsmen shape a single sheet of metal into a distinctive curved form.
Here is where they manufacture the custom-made Vienna horns used by the Vienna Philharmonic Orchestra, greatest of all the world’s orchestras. This author was given the opportunity to report on the factory floor.
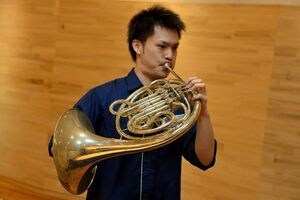
Normal horn
The difference between a Vienna horn and an ordinary horn is, in a manner of speaking, “like the difference between a wagon and an automobile” (Yamaha Publicity Department). In addition to the horns, the Vienna Philharmonic uses a variety of antique-style instruments that differ from off-the-shelf items in order to accurately reproduce the sound at the time the pieces were composed. The differences in the construction of the instruments impart completely different nuances to the sound.
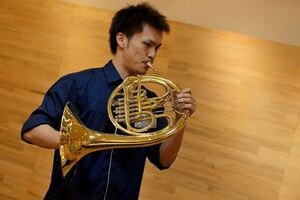
Vienna horn
Even a complete layman such as the author was able to tell the difference when comparing the sounds. In contrast to the soft, slightly hollow sound of an ordinary horn, a Vienna horn has a crisp, firm sound. The difference is particularly striking in long, drawn-out notes.
Yamaha first began working on instruments for the Vienna Philharmonic in the 1970s.The Vienna Philharmonic’s instruments are custom-made items, but the factories that had manufactured them in Europe suffered from financial difficulties and a lack of new craftsmen entering the trade, going out of business one after another. In order to preserve the traditional sound, some orchestra musicians commissioned Yamaha to manufacture them.
“Can we entrust our sound to craftsmen outside Europe?”
At the time, many orchestra members voiced opposition. Of course, these were mainly instruments with which Yamaha had no prior experience, and there was no guarantee that they could manufacture high level instruments. Yamaha was first sounded out regarding Vienna-style trumpets. The manufacturing process took two years, but their level of performance received high praise from the orchestra. This led to them commissioning Vienna horns as well.
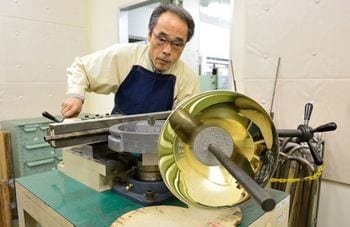
Shigeto Saito, who has 36 years of experience making wind instruments.
They currently work on other Vienna-style instruments such as the oboe and bassoon. In 2012, Director and Managing Executive Officer Hiroo Okabe received the Merit Award of the Province of Vienna in recognition for his contributions to the development of Viennese musical culture.
In contrast to the approximately 5,000 commercially marketed horns produced annually at the Toyooka Plant (a rate of roughly 25 per day), only 10 to 15 Vienna horns are made in a year. It takes about one month to manufacture each one.
Even at Yamaha, which employs around 700 craftsmen making wind instruments, there are only two technicians that handle the entire production process for a horn alone. If you narrow it down to just the manufacturing of Vienna horns, then there is only Shigeto Saito, who has 36 years of experience making wind instruments. Mr. Saito himself says, “Even now there are still some points that present difficulties, such as continually applying the same force to the press.”
At the Toyooka Plant, mechanization has advanced in order to produce a large quantity of instruments efficiently, with some aspects of the process like coating and washing being automated. However, there is still much work that relies on human hands. Take a single weld for example. In a musical instrument, even the slightest slip will change the sound quality, so using robots is problematic. The welding is done by workers using the soldering method who understand how the metal expands and contracts when subjected to heat.
Assembly, the final step of the process, is also done entirely by hand. There are dozens of workers in rows, and each is responsible for a single type of instrument, silently assembling each by hand. The assembly floor is lit by more than double the number of lights than other floors to ensure that even minor imperfections are not overlooked
Following assembly, each instrument is inspected and actually played to ensure there are no defects. For this reason, you can perpetually hear the sound of instruments being played, from high notes to low notes, coming from a corner of the floor. Instruments manufactured here are not shipped without passing through this final inspection by human hands.
The Toyooka Plant produces instruments in a wide range of grades, from the instruments of the world’s greatest orchestra to those used by an elementary school fife and drum corps. What supports this organization is the expert techniques of its craftsmen.